Automation 2024: IIoT And Smart Factories
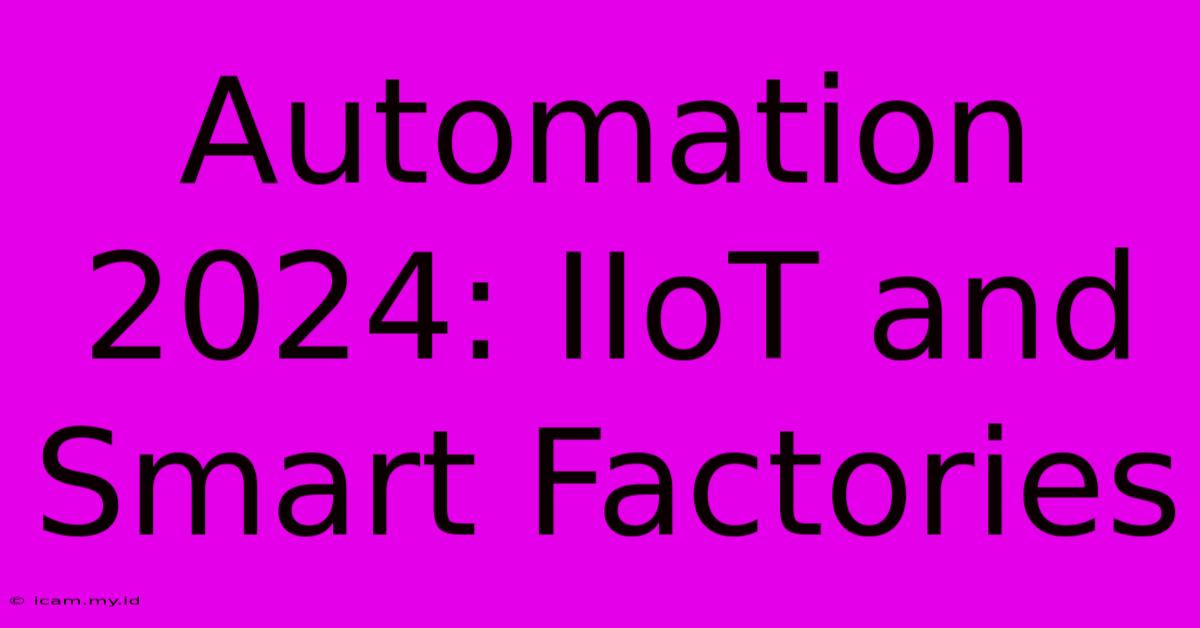
Find more detailed and interesting information on our website. Click the link below to start advanced information: Visit Best Website meltwatermedia.ca. Jangan lewatkan!
Table of Contents
Automation 2024: IIoT and Smart Factories – The Future of Manufacturing is Now
The manufacturing landscape is undergoing a radical transformation, driven by the convergence of Industrial Internet of Things (IIoT) and the rise of smart factories. 2024 represents a pivotal year in this evolution, with automation technologies rapidly advancing and reshaping how goods are produced. This article delves deep into the key trends shaping automation in 2024, focusing on the crucial roles played by IIoT and the smart factory paradigm.
What is the Industrial Internet of Things (IIoT)?
The IIoT is essentially the extension of the Internet of Things (IoT) to industrial settings. It involves connecting machines, sensors, and other devices within a manufacturing facility to a network, enabling data collection, analysis, and real-time monitoring. This interconnectedness fuels automation by providing the critical data needed for optimizing processes, predicting maintenance needs, and improving overall efficiency.
Key IIoT technologies driving automation in 2024 include:
- Edge computing: Processing data closer to the source (the factory floor) reduces latency and bandwidth requirements, enabling faster response times for automation systems.
- Cloud computing: Provides scalable storage and processing power for analyzing vast amounts of data generated by IIoT devices. This allows for advanced analytics and predictive modeling.
- Artificial Intelligence (AI) and Machine Learning (ML): AI and ML algorithms are crucial for analyzing IIoT data, identifying patterns, and making autonomous decisions, driving optimization and predictive maintenance.
- 5G and other advanced wireless technologies: High-speed, low-latency connectivity is essential for supporting the real-time data transfer required by IIoT applications. 5G promises to revolutionize IIoT deployments, enabling seamless communication between devices and systems.
The Smart Factory: A Data-Driven Ecosystem
A smart factory leverages IIoT technologies to create a highly interconnected and automated manufacturing environment. It's characterized by:
- Real-time visibility: Comprehensive monitoring of all aspects of the production process, providing insights into efficiency, bottlenecks, and potential issues.
- Predictive maintenance: AI-powered systems analyze sensor data to predict equipment failures, allowing for proactive maintenance and minimizing downtime.
- Automated decision-making: Intelligent systems automate tasks such as scheduling, resource allocation, and quality control, optimizing operations and reducing human error.
- Improved collaboration: Enhanced communication and data sharing between different departments and stakeholders, fostering collaboration and streamlining workflows.
- Increased flexibility and agility: Smart factories can adapt quickly to changing demands and market conditions, improving responsiveness and competitiveness.
Automation Trends Shaping Manufacturing in 2024
Several significant trends are shaping the automation landscape in 2024, significantly impacting how IIoT and smart factories are being implemented:
-
Rise of collaborative robots (cobots): Cobots are designed to work alongside human workers, enhancing productivity and safety. They are increasingly being deployed in smart factories to perform tasks that are repetitive, dangerous, or require high precision.
-
Increased adoption of AI-powered quality control: AI-driven vision systems and other advanced technologies are enhancing quality control processes, identifying defects with greater accuracy and speed than traditional methods. This leads to reduced waste and improved product quality.
-
Growing emphasis on cybersecurity: As factories become increasingly connected, cybersecurity becomes paramount. Robust security measures are essential to protect against cyberattacks that could disrupt operations or compromise sensitive data.
-
Focus on sustainability: Smart factories are increasingly incorporating sustainable practices, such as energy-efficient equipment and waste reduction strategies, to minimize their environmental impact.
-
Digital twins: Virtual representations of physical assets and processes are used for simulation, optimization, and predictive maintenance, reducing risks and improving efficiency.
Challenges in Implementing IIoT and Smart Factories
While the potential benefits of IIoT and smart factories are substantial, several challenges remain:
-
High initial investment costs: Implementing IIoT and smart factory technologies requires significant upfront investment in hardware, software, and integration services.
-
Data security and privacy concerns: Protecting sensitive data from cyberattacks and ensuring compliance with data privacy regulations are crucial concerns.
-
Integration complexities: Integrating different systems and technologies within a factory environment can be complex and require specialized expertise.
-
Skills gap: A shortage of skilled workers with expertise in IIoT, AI, and other relevant technologies is a major barrier to adoption.
-
Legacy systems compatibility: Integrating new technologies with existing legacy systems can be challenging, requiring careful planning and potentially significant upgrades.
Overcoming the Challenges: A Strategic Approach
Successfully implementing IIoT and smart factories requires a strategic approach that addresses these challenges proactively:
-
Phased implementation: A phased approach allows organizations to start small, gradually expanding their automation initiatives as they gain experience and build expertise.
-
Investing in employee training and development: Investing in training programs to upskill the workforce is essential for ensuring successful adoption of new technologies.
-
Partnering with technology providers: Collaborating with experienced technology providers can help organizations navigate the complexities of implementing IIoT and smart factory solutions.
-
Prioritizing cybersecurity: Implementing robust cybersecurity measures from the outset is crucial for protecting against cyberattacks.
-
Focusing on ROI: Demonstrating a clear return on investment (ROI) is crucial for securing buy-in from stakeholders and ensuring continued investment in automation initiatives.
The Future of Automation in Manufacturing
The future of manufacturing is inextricably linked to the continued advancement and adoption of IIoT and smart factory technologies. 2024 marks a significant milestone in this journey, with the trends outlined above shaping the direction of the industry. Companies that embrace these technologies and overcome the associated challenges will be better positioned to thrive in an increasingly competitive and dynamic global market. The ability to adapt, innovate, and leverage data will be the key differentiators for success in the age of smart factories and the IIoT. Continuous improvement, data-driven decision-making, and a skilled workforce will be critical factors in realizing the full potential of this technological revolution. The smart factory is not just a concept; it's the future of manufacturing, and that future is arriving faster than ever before.
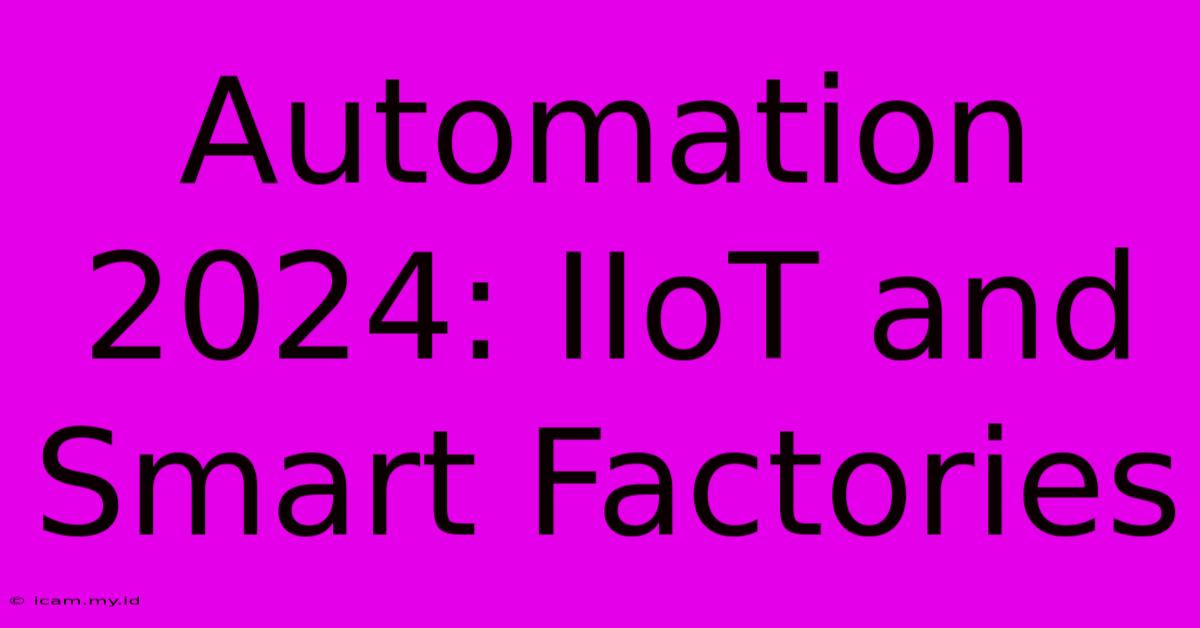
Thank you for visiting our website. Automation 2024: IIoT And Smart Factories. We hope the information we provide is helpful to you. Feel free to contact us if you have any questions or need additional assistance. See you next time, and don't forget to save this page!
Kami berterima kasih atas kunjungan Anda untuk melihat lebih jauh. Automation 2024: IIoT And Smart Factories. Informasikan kepada kami jika Anda memerlukan bantuan tambahan. Tandai situs ini dan pastikan untuk kembali lagi segera!
Featured Posts
-
New Findings Bioinformatics And Academic Publishing
Nov 28, 2024
-
Match Report Selangor Vs Mbpj
Nov 28, 2024
-
Tous Les Jours Bakery A Northpoint City Addition
Nov 28, 2024
-
Cadet Death Prompts Tudm Investigation
Nov 28, 2024
-
First A330neo Malaysia Airlines Receives
Nov 28, 2024