Building A Smart Manufacturing System
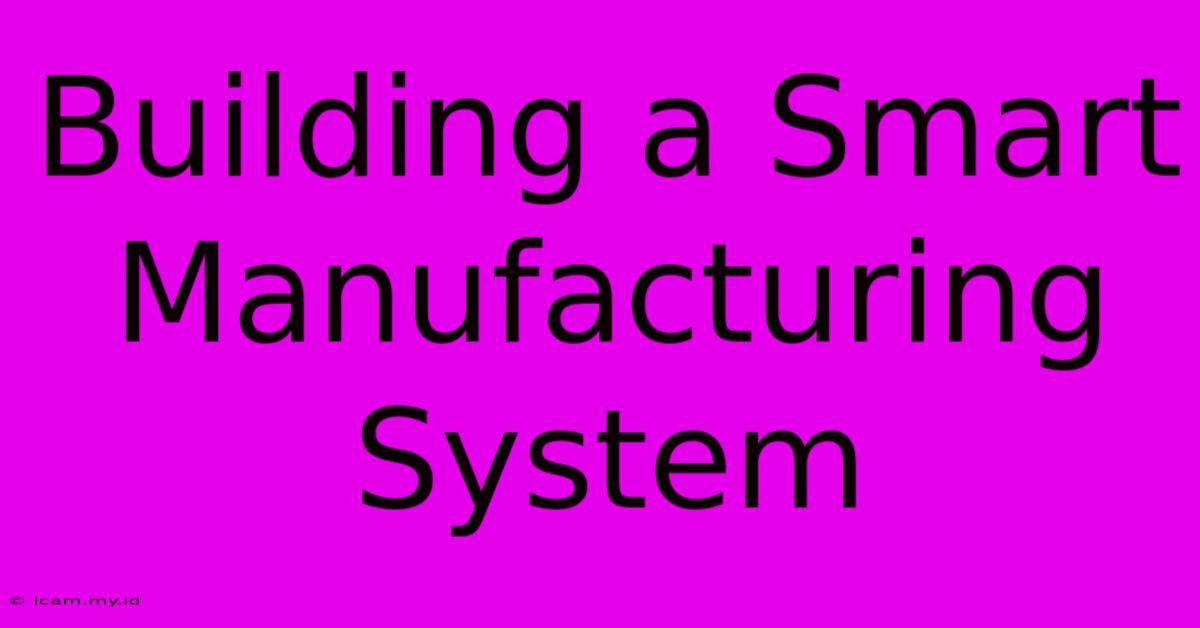
Find more detailed and interesting information on our website. Click the link below to start advanced information: Visit Best Website meltwatermedia.ca. Jangan lewatkan!
Table of Contents
Building a Smart Manufacturing System: A Comprehensive Guide
The manufacturing industry is undergoing a dramatic transformation, driven by the convergence of technologies like Artificial Intelligence (AI), Internet of Things (IoT), cloud computing, and big data analytics. This revolution is leading to the rise of smart manufacturing, a data-driven approach that optimizes processes, improves efficiency, and enhances overall productivity. Building a smart manufacturing system, however, is a complex undertaking, requiring careful planning, strategic investment, and a commitment to continuous improvement. This comprehensive guide explores the key aspects of building a successful smart manufacturing system.
Understanding the Core Components of a Smart Manufacturing System
A truly smart manufacturing system isn't just about installing new technology; it's about integrating various technologies to create a cohesive and intelligent ecosystem. Here are the core components:
1. Internet of Things (IoT) Devices: The foundation of any smart manufacturing system lies in the deployment of IoT devices across the factory floor. These devices, ranging from sensors and actuators to robots and programmable logic controllers (PLCs), collect real-time data on various aspects of the manufacturing process. This data includes machine performance, environmental conditions, material flow, and product quality. The sheer volume of data generated by these devices is a crucial aspect of the system's intelligence.
2. Data Acquisition and Management: Collecting data is only the first step. Effective data management is crucial. This involves establishing a robust infrastructure for collecting, storing, processing, and analyzing the massive amounts of data generated by IoT devices. This often requires the implementation of advanced data management systems, including cloud-based platforms, data lakes, and data warehouses. Choosing the right platform and ensuring data security are paramount.
3. Data Analytics and Business Intelligence: The collected data becomes valuable only when analyzed effectively. Advanced analytics techniques, including machine learning (ML) and artificial intelligence (AI), are employed to extract meaningful insights from the data. This allows manufacturers to identify patterns, predict potential problems, and optimize processes for improved efficiency and quality. Business intelligence (BI) tools then translate these insights into actionable information for decision-making.
4. Cloud Computing: Cloud computing plays a critical role in enabling smart manufacturing. It provides the scalability and flexibility needed to handle the vast amounts of data generated by IoT devices and analytics tools. Cloud platforms offer robust storage, processing power, and security features, making them an ideal solution for managing the complex data infrastructure of a smart manufacturing system.
5. Advanced Automation and Robotics: Smart manufacturing leverages automation and robotics to optimize production processes. Robotic systems, guided by data-driven insights, can perform tasks with greater precision, speed, and consistency than human workers. This enhances efficiency, reduces errors, and improves overall product quality. The integration of robots with other smart manufacturing components is crucial for maximizing their effectiveness.
6. Cybersecurity: The increased connectivity inherent in smart manufacturing systems also increases the vulnerability to cyberattacks. A robust cybersecurity framework is essential to protect sensitive data and prevent disruptions to operations. This includes implementing security protocols, access controls, and threat detection systems to safeguard the entire system.
7. Human-Machine Collaboration: Despite the advancements in automation, human expertise remains crucial in smart manufacturing. Smart systems should empower human workers by providing them with real-time insights and decision support tools. This collaborative approach allows humans to focus on higher-level tasks such as problem-solving, innovation, and strategic decision-making.
Steps to Building a Smart Manufacturing System
Building a successful smart manufacturing system is an iterative process that requires a well-defined roadmap. Here are the key steps involved:
1. Define Clear Objectives and KPIs: Before embarking on the implementation, clearly define the goals you aim to achieve with your smart manufacturing system. This includes identifying specific areas for improvement, such as reducing production time, enhancing product quality, or minimizing waste. Define Key Performance Indicators (KPIs) to track progress and measure the success of your implementation.
2. Conduct a Thorough Assessment of Your Current Infrastructure: Assess your existing manufacturing processes, equipment, and IT infrastructure. Identify areas where improvements are needed and determine the feasibility of integrating smart technologies. This assessment will help guide your investment decisions and ensure that the new system seamlessly integrates with your existing infrastructure.
3. Select Appropriate Technologies and Platforms: Based on your assessment, choose the appropriate technologies and platforms for your smart manufacturing system. Consider factors such as scalability, cost, security, and vendor support. Selecting the right technology is crucial for the long-term success of your implementation. Choosing cloud platforms that fit your security and compliance standards is critical.
4. Develop a Phased Implementation Plan: Rather than attempting a complete overhaul of your manufacturing processes at once, implement your smart manufacturing system in phases. This allows you to test and refine your system gradually, minimizing disruption to your operations and reducing the risk of costly errors. Start with a pilot project in a limited area before expanding to other parts of your factory.
5. Integrate Data Sources and Establish Data Pipelines: Ensure that all data sources, including IoT devices, machines, and enterprise systems, are integrated into your smart manufacturing platform. Develop robust data pipelines to collect, process, and analyze data efficiently and securely. This involves investing in data management tools and establishing appropriate data governance policies.
6. Develop and Deploy Analytics and AI/ML Models: Develop and deploy advanced analytics and AI/ML models to extract meaningful insights from your data. This involves collaborating with data scientists and engineers to create models that accurately predict outcomes and optimize processes. Experimentation and continuous improvement are vital in this stage.
7. Implement Robust Cybersecurity Measures: Throughout the implementation process, prioritize cybersecurity. Implement strong security protocols, access controls, and threat detection systems to protect your data and prevent cyberattacks. Regular security audits and employee training are essential to maintain a secure system.
8. Continuous Monitoring and Improvement: Once your smart manufacturing system is operational, continuously monitor its performance and make necessary adjustments. Regularly review your KPIs and identify areas for improvement. Embrace a culture of continuous improvement to ensure that your system remains effective and efficient in the long term.
Challenges and Considerations in Building a Smart Manufacturing System
While the benefits of smart manufacturing are substantial, several challenges must be addressed:
- High Initial Investment: Implementing a smart manufacturing system requires significant upfront investment in hardware, software, and expertise.
- Data Integration Complexity: Integrating data from various sources can be complex and require specialized skills.
- Lack of Skilled Workforce: Finding and training personnel with the necessary skills to operate and maintain a smart manufacturing system can be challenging.
- Cybersecurity Risks: The increased connectivity exposes manufacturers to greater cybersecurity risks.
- Legacy Systems Integration: Integrating new technologies with existing legacy systems can be difficult and costly.
Conclusion:
Building a smart manufacturing system is a journey, not a destination. It requires careful planning, strategic investment, and a commitment to continuous improvement. By addressing the challenges and implementing the steps outlined in this guide, manufacturers can reap the significant benefits of improved efficiency, productivity, and competitiveness in today's rapidly evolving market. Remember, the key to success lies in a holistic approach that considers not only the technology but also the people, processes, and organizational culture.
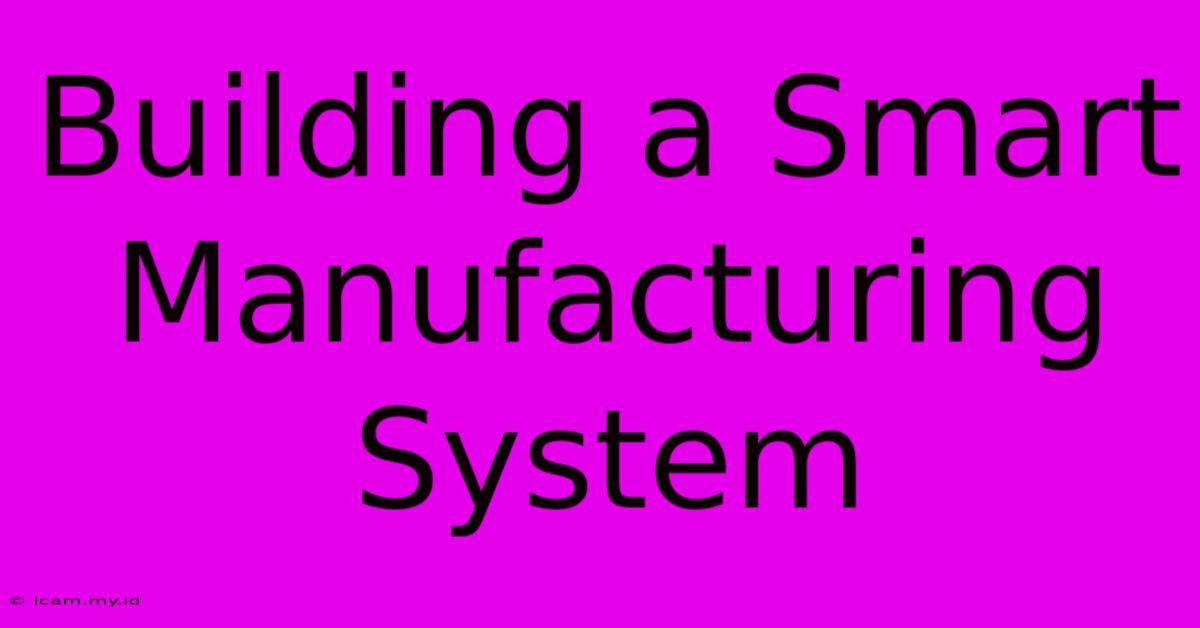
Thank you for visiting our website. Building A Smart Manufacturing System. We hope the information we provide is helpful to you. Feel free to contact us if you have any questions or need additional assistance. See you next time, and don't forget to save this page!
Kami berterima kasih atas kunjungan Anda untuk melihat lebih jauh. Building A Smart Manufacturing System. Informasikan kepada kami jika Anda memerlukan bantuan tambahan. Tandai situs ini dan pastikan untuk kembali lagi segera!
Featured Posts
-
Insurer Premium Hikes Under Scrutiny
Nov 28, 2024
-
Kinos Fast Red Giant Turnaround
Nov 28, 2024
-
Iona Falls To West Virginia
Nov 28, 2024
-
Four Provinces Face Severe Flooding
Nov 28, 2024
-
Vinicius Jr Out Real Vs Liverpool
Nov 28, 2024