Building Economic Strength: Smart Factories
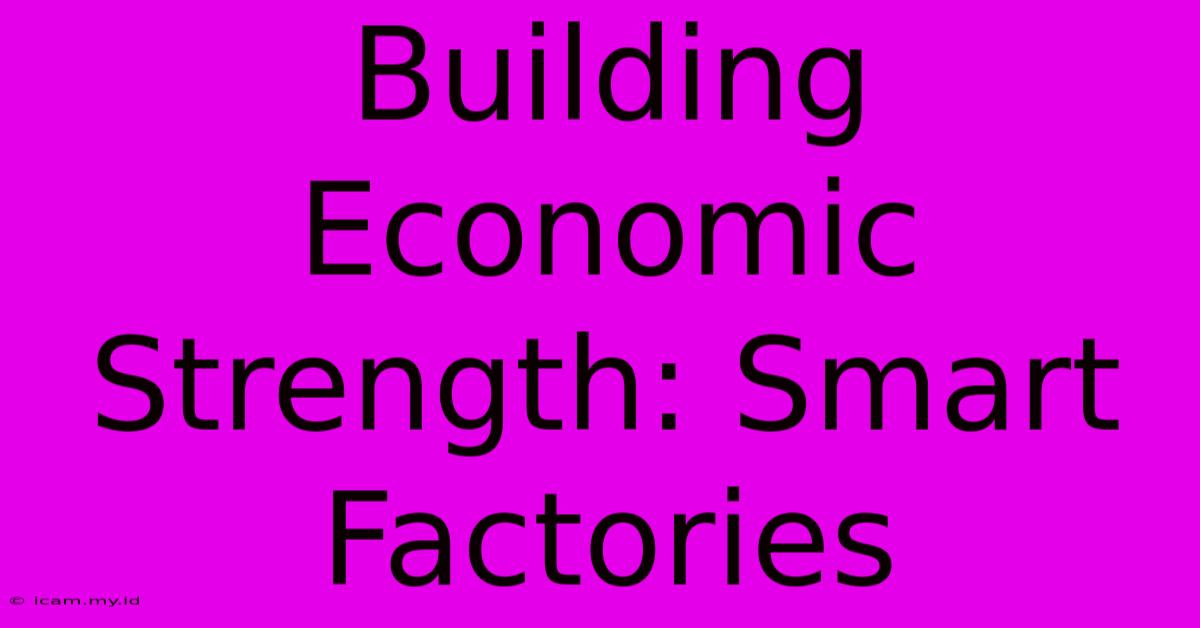
Find more detailed and interesting information on our website. Click the link below to start advanced information: Visit Best Website meltwatermedia.ca. Jangan lewatkan!
Table of Contents
Building Economic Strength: Smart Factories
The global economy is in constant flux, driven by technological advancements, shifting demographics, and evolving consumer demands. To thrive in this dynamic landscape, nations and businesses must embrace innovation and efficiency. One key driver of economic strength is the adoption of smart factories, also known as Industry 4.0 facilities. These advanced manufacturing environments leverage digital technologies to optimize production, improve quality, and enhance overall competitiveness. This article delves into the critical role smart factories play in building economic strength, exploring their benefits, challenges, and the necessary steps for successful implementation.
What is a Smart Factory?
A smart factory goes beyond traditional automation. It's a holistic approach to manufacturing that integrates various technologies, including:
- Internet of Things (IoT): Sensors and connected devices monitor equipment, processes, and products in real-time, providing crucial data for analysis and decision-making.
- Artificial Intelligence (AI): AI algorithms analyze data to predict equipment failures, optimize production schedules, and improve quality control. Machine learning plays a significant role in adapting to changing conditions and improving efficiency over time.
- Big Data Analytics: The massive amounts of data generated by connected devices are analyzed to identify trends, optimize processes, and improve decision-making across the entire supply chain.
- Cloud Computing: Cloud platforms provide scalable computing resources for data storage, processing, and analysis, allowing for flexibility and cost-effectiveness.
- Robotics and Automation: Robots and automated systems perform repetitive tasks, increasing productivity and reducing human error. Collaborative robots (cobots) work alongside human workers, enhancing efficiency and safety.
- Cybersecurity: Robust security measures are essential to protect sensitive data and prevent cyberattacks that could disrupt operations.
Economic Benefits of Smart Factories
The adoption of smart factory technologies yields substantial economic benefits at both the individual company and national levels:
1. Increased Productivity and Efficiency: Automation and optimization techniques significantly boost production output while minimizing waste and downtime. Real-time data analysis enables proactive maintenance, preventing costly equipment failures and maximizing uptime.
2. Enhanced Product Quality: Smart factories improve quality control through rigorous data-driven monitoring and analysis. AI-powered systems detect defects early in the production process, minimizing scrap and rework. This leads to higher customer satisfaction and brand reputation.
3. Reduced Operational Costs: Optimized resource allocation, predictive maintenance, and reduced waste contribute to significant cost savings. Smart factories minimize energy consumption and material waste, lowering operational expenses and environmental impact.
4. Improved Supply Chain Management: Real-time data visibility across the supply chain allows for better inventory management, streamlined logistics, and improved responsiveness to market demands. This reduces lead times and improves overall supply chain efficiency.
5. Increased Innovation and Competitiveness: Smart factories foster a culture of innovation by providing access to advanced technologies and data-driven insights. This allows businesses to develop new products and services faster, gaining a competitive edge in the global marketplace.
6. Job Creation and Upskilling: While some fear job displacement due to automation, smart factories also create new, higher-skilled jobs in areas like data analytics, software development, and robotics maintenance. This necessitates investment in workforce training and upskilling programs to ensure a skilled workforce.
7. Economic Growth and Development: Widespread adoption of smart factories across a nation drives economic growth by increasing productivity, improving competitiveness, and fostering innovation. This leads to higher GDP, increased exports, and improved living standards.
Challenges in Implementing Smart Factories
Despite the numerous benefits, implementing smart factories presents several challenges:
1. High Initial Investment: The cost of implementing smart factory technologies can be substantial, requiring significant upfront investment in hardware, software, and integration services. This can be a barrier for small and medium-sized enterprises (SMEs).
2. Data Security and Privacy Concerns: The reliance on connected devices and data collection raises concerns about data security and privacy. Robust cybersecurity measures are crucial to protect sensitive information and prevent cyberattacks.
3. Integration Complexity: Integrating various technologies and systems can be complex and time-consuming. Careful planning and expertise are essential to ensure seamless integration and avoid operational disruptions.
4. Skill Gap and Workforce Training: The adoption of smart factory technologies requires a skilled workforce with expertise in data analytics, AI, robotics, and cybersecurity. Addressing the skill gap through training and upskilling programs is crucial for successful implementation.
5. Legacy Systems and Infrastructure: Upgrading legacy systems and infrastructure to support smart factory technologies can be challenging and costly. A phased approach may be necessary to avoid disrupting existing operations.
6. Lack of Standardization: The absence of industry-wide standards for data exchange and communication can hinder interoperability between different systems and technologies. Standardization efforts are crucial for promoting wider adoption.
Strategies for Successful Smart Factory Implementation
To successfully implement smart factories and reap their economic benefits, organizations should adopt a strategic approach that includes:
- Clearly Defined Goals and Objectives: Establishing clear goals and objectives for smart factory implementation is crucial for guiding decision-making and measuring progress.
- Phased Implementation: A phased approach allows organizations to gradually adopt smart factory technologies, minimizing disruption and managing costs effectively.
- Strong Leadership and Collaboration: Successful implementation requires strong leadership, cross-functional collaboration, and commitment from all stakeholders.
- Investment in Training and Development: Investing in training and development programs for employees is essential to build the necessary skills and expertise.
- Data Security and Privacy Measures: Implementing robust cybersecurity measures is crucial to protect sensitive data and prevent cyberattacks.
- Collaboration and Partnerships: Collaborating with technology providers, industry partners, and research institutions can accelerate implementation and facilitate knowledge sharing.
- Government Support and Incentives: Government policies and incentives can play a significant role in encouraging the adoption of smart factory technologies.
Conclusion: Smart Factories as a Driver of Economic Strength
Smart factories are not just a technological advancement; they represent a fundamental shift in how we manufacture goods and services. Their ability to boost productivity, improve quality, and enhance competitiveness makes them a critical driver of economic strength. While challenges exist, the potential benefits are substantial. By addressing these challenges through strategic planning, investment in training, and collaboration, nations and businesses can harness the power of smart factories to build a more resilient, innovative, and prosperous future. The journey towards a smart factory demands a commitment to continuous improvement, adaptation, and a willingness to embrace the transformative power of technology. The rewards, however, are undeniable, promising a future of heightened economic strength and global competitiveness.
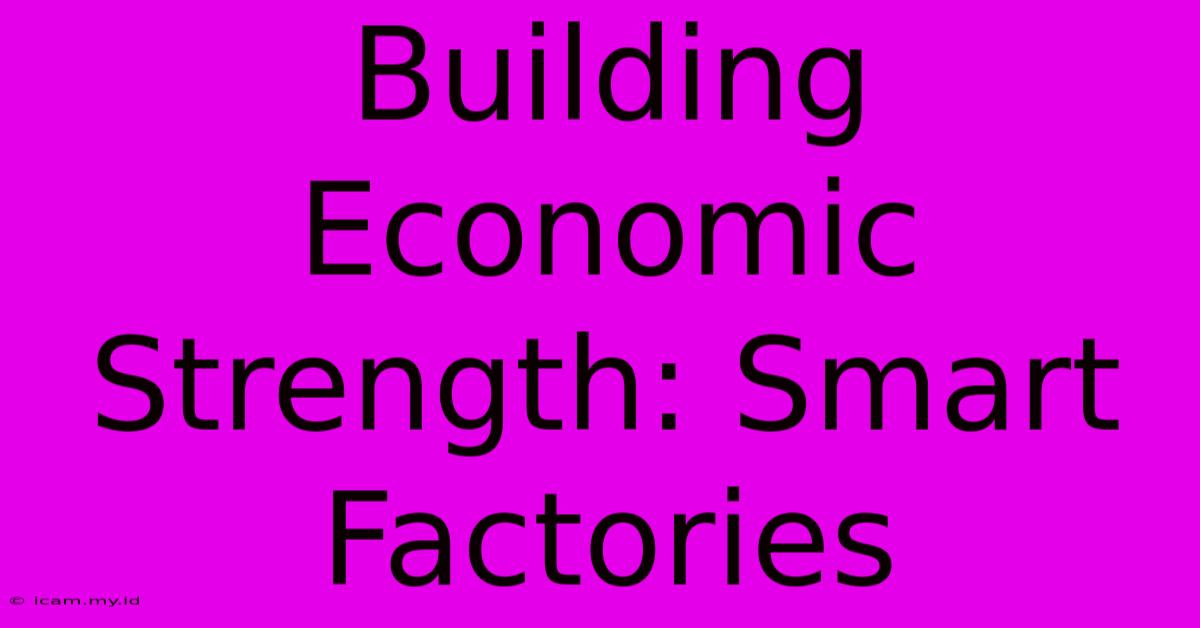
Thank you for visiting our website. Building Economic Strength: Smart Factories. We hope the information we provide is helpful to you. Feel free to contact us if you have any questions or need additional assistance. See you next time, and don't forget to save this page!
Kami berterima kasih atas kunjungan Anda untuk melihat lebih jauh. Building Economic Strength: Smart Factories. Informasikan kepada kami jika Anda memerlukan bantuan tambahan. Tandai situs ini dan pastikan untuk kembali lagi segera!
Featured Posts
-
Liverpool Transfer News Salah Replacement
Nov 28, 2024
-
Mountaineers Top Iona In Coliseum
Nov 28, 2024
-
Vinicius Jr Injury Liverpool Trip Doubtful
Nov 28, 2024
-
Ui Tm Cadet Death Under Investigation
Nov 28, 2024
-
Businessman Ananda Krishnan Dies At 86
Nov 28, 2024