Digital Transformation In Manufacturing: 2024
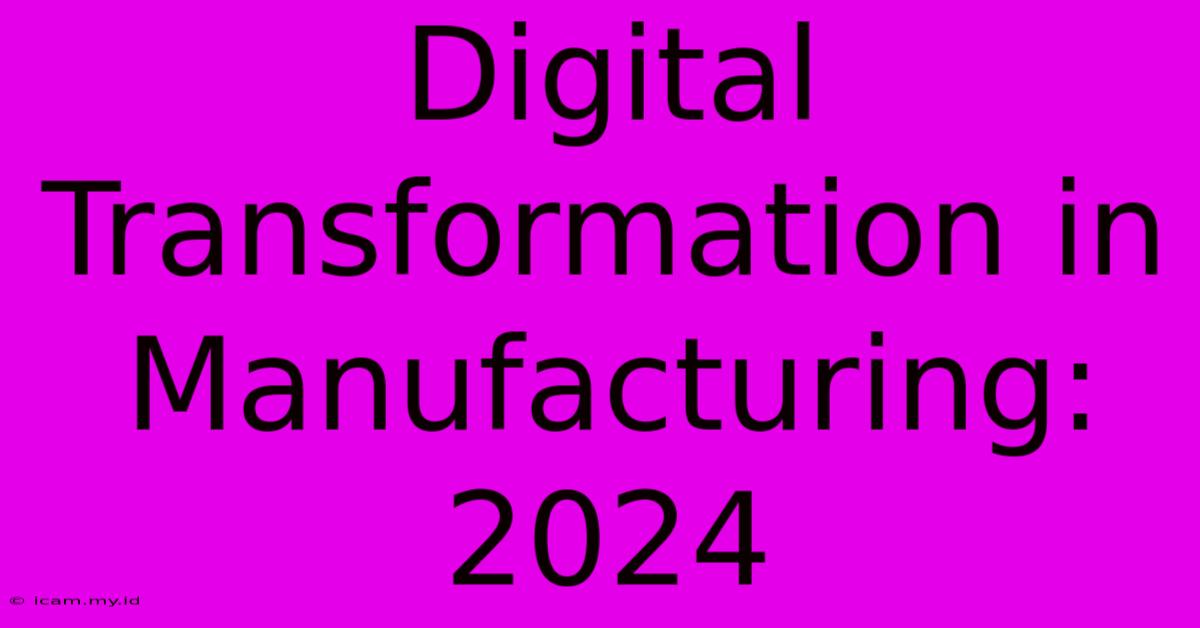
Find more detailed and interesting information on our website. Click the link below to start advanced information: Visit Best Website meltwatermedia.ca. Jangan lewatkan!
Table of Contents
Digital Transformation in Manufacturing: 2024 and Beyond
The manufacturing landscape is undergoing a dramatic shift, driven by the relentless march of digital technologies. 2024 marks a pivotal year in this digital transformation, with manufacturers facing both unprecedented opportunities and significant challenges. This article delves deep into the current state of digital transformation in manufacturing, exploring key trends, technological advancements, and the strategic imperatives for success in this evolving ecosystem.
The Driving Forces Behind Manufacturing's Digital Shift
Several powerful forces are accelerating the adoption of digital technologies within manufacturing:
-
Increased Competition: Globalization and the rise of agile competitors are forcing manufacturers to optimize efficiency, reduce costs, and enhance product quality at an unprecedented pace. Digital tools offer the precision and speed needed to stay ahead.
-
Customer Demands: Consumers increasingly expect personalized products, faster delivery times, and greater transparency throughout the supply chain. Digital technologies enable manufacturers to meet these demands by improving responsiveness and traceability.
-
Data-Driven Decision Making: The sheer volume of data generated in modern manufacturing plants provides invaluable insights into operations, allowing for data-driven decision making that improves efficiency and minimizes waste. Advanced analytics unlock this potential.
-
Technological Advancements: Breakthroughs in areas such as Artificial Intelligence (AI), Machine Learning (ML), Internet of Things (IoT), cloud computing, and robotics are providing manufacturers with powerful new tools to automate processes, improve quality control, and optimize resource allocation.
-
Sustainability Concerns: Growing awareness of environmental issues is pushing manufacturers to adopt more sustainable practices. Digital technologies can help reduce energy consumption, minimize waste, and improve the overall environmental footprint of manufacturing operations.
Key Technologies Shaping Digital Transformation in Manufacturing
Several key technologies are at the forefront of manufacturing's digital transformation:
-
Industrial Internet of Things (IIoT): IIoT connects machines, sensors, and other devices within a manufacturing facility, enabling real-time data collection and analysis. This data provides valuable insights into operational efficiency, equipment performance, and potential problems. Predictive maintenance, a key application of IIoT, allows manufacturers to anticipate and prevent equipment failures, minimizing downtime and improving productivity.
-
Artificial Intelligence (AI) and Machine Learning (ML): AI and ML algorithms can analyze vast amounts of data to identify patterns, predict outcomes, and optimize manufacturing processes. This includes applications such as quality control, where AI can detect defects with greater accuracy than human inspectors, and predictive maintenance, where ML can predict equipment failures based on historical data. Robotic Process Automation (RPA) also leverages AI to automate repetitive tasks, freeing up human workers for more complex and creative roles.
-
Cloud Computing: Cloud computing provides manufacturers with scalable and cost-effective access to computing resources, data storage, and software applications. This enables greater agility and flexibility, allowing manufacturers to adapt quickly to changing market conditions. Cloud-based platforms also facilitate collaboration and data sharing across the entire value chain.
-
Additive Manufacturing (3D Printing): 3D printing is revolutionizing prototyping and production, enabling manufacturers to create highly customized products on demand. This technology reduces lead times, lowers costs, and allows for greater design flexibility.
-
Digital Twins: A digital twin is a virtual representation of a physical asset, process, or system. Digital twins allow manufacturers to simulate and optimize processes before implementing them in the real world, reducing risk and improving efficiency.
Strategic Imperatives for Successful Digital Transformation
Successfully navigating the digital transformation requires a strategic approach encompassing several key elements:
-
Develop a Clear Digital Vision and Strategy: A well-defined digital strategy outlines specific goals, identifies key technologies, and establishes a roadmap for implementation. This strategy should align with the overall business objectives and take into account the unique needs and capabilities of the organization.
-
Invest in the Right Technologies and Talent: Digital transformation requires significant investment in both technology and skilled personnel. Manufacturers need to select technologies that align with their business needs and develop a workforce capable of utilizing these technologies effectively. This includes training existing employees and recruiting new talent with the necessary skills.
-
Foster a Culture of Innovation and Collaboration: Successful digital transformation requires a culture that embraces change and encourages collaboration across different departments and with external partners. This includes fostering open communication, sharing knowledge, and creating a safe space for experimentation.
-
Prioritize Data Security and Privacy: The increasing reliance on data requires robust security measures to protect sensitive information from cyber threats. Manufacturers need to implement strong cybersecurity protocols and comply with relevant data privacy regulations.
-
Embrace Agile Methodologies: Agile methodologies, with their iterative and flexible approach, are well-suited to the dynamic nature of digital transformation. These methodologies enable manufacturers to adapt quickly to changing requirements and learn from experience.
Challenges and Opportunities in 2024 and Beyond
While the opportunities presented by digital transformation are immense, several challenges remain:
-
Integration Complexity: Integrating new technologies with existing systems can be complex and time-consuming, requiring significant effort and expertise.
-
Data Management: Managing and analyzing the vast amounts of data generated by digital technologies can be challenging, requiring advanced analytics capabilities and robust data management infrastructure.
-
Skills Gap: The lack of skilled workers with expertise in digital technologies presents a significant challenge for many manufacturers.
-
Cost of Implementation: The initial investment required for digital transformation can be substantial, potentially posing a barrier for smaller manufacturers.
However, the potential rewards far outweigh the challenges. Manufacturers who successfully embrace digital transformation will be better positioned to compete in a rapidly evolving market, achieve greater efficiency, and create new opportunities for growth.
Conclusion: Embracing the Future of Manufacturing
Digital transformation is not just a trend; it's a fundamental shift in how manufacturing operates. 2024 and beyond will see an acceleration of this transformation, with manufacturers who embrace these changes poised for significant success. By developing a clear strategy, investing in the right technologies and talent, and fostering a culture of innovation, manufacturers can harness the power of digital technologies to achieve operational excellence, enhance product quality, and drive sustainable growth. The future of manufacturing is digital, and those who adapt will thrive.
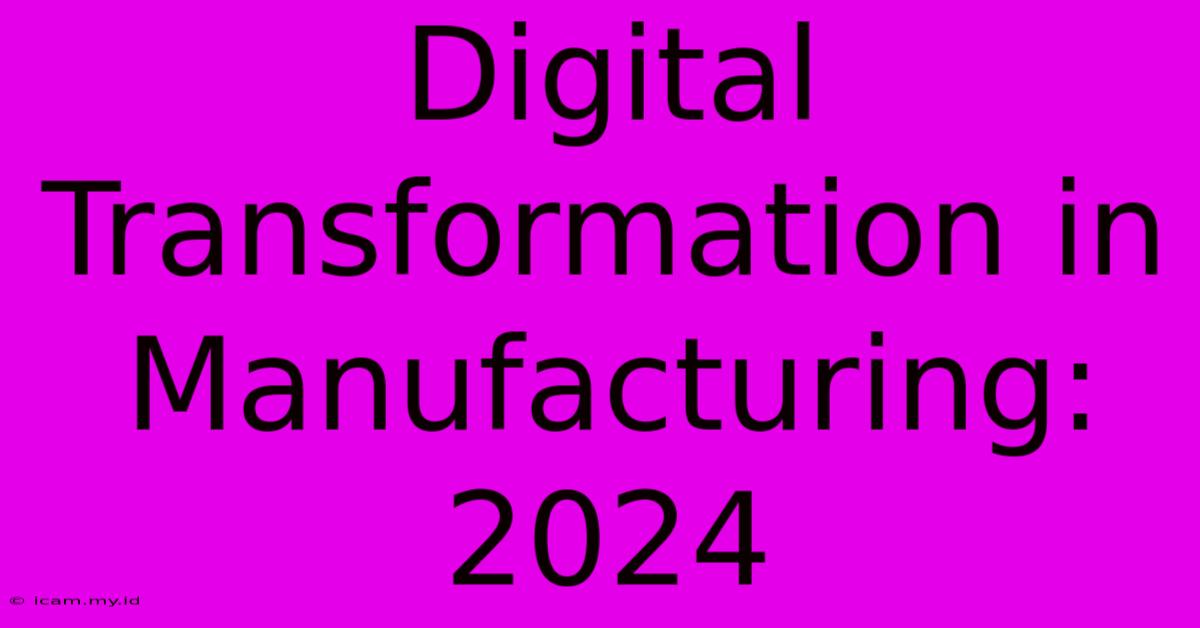
Thank you for visiting our website. Digital Transformation In Manufacturing: 2024. We hope the information we provide is helpful to you. Feel free to contact us if you have any questions or need additional assistance. See you next time, and don't forget to save this page!
Kami berterima kasih atas kunjungan Anda untuk melihat lebih jauh. Digital Transformation In Manufacturing: 2024. Informasikan kepada kami jika Anda memerlukan bantuan tambahan. Tandai situs ini dan pastikan untuk kembali lagi segera!
Featured Posts
-
Malaysian Billionaire Ananda Krishnan Passes Away
Nov 28, 2024
-
Red Giants 3 Kino Led Shifts
Nov 28, 2024
-
Australias Kids Social Media Ban Nears
Nov 28, 2024
-
Yishun Gets New Tous Les Jours Outlet
Nov 28, 2024
-
South Korea Targets Vietnam Real Estate Holdings
Nov 28, 2024