Exploring Automated Factories In Manufacturing
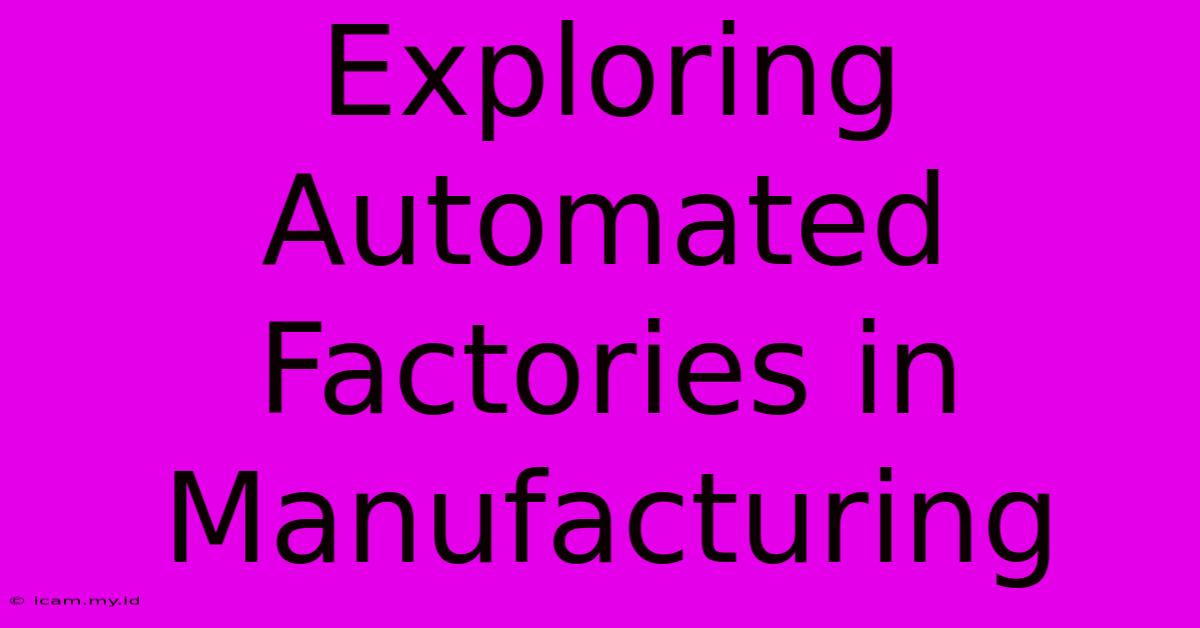
Find more detailed and interesting information on our website. Click the link below to start advanced information: Visit Best Website meltwatermedia.ca. Jangan lewatkan!
Table of Contents
Exploring Automated Factories in Manufacturing: The Future of Production
The manufacturing landscape is undergoing a dramatic transformation, driven by the relentless march of automation. Automated factories, once a futuristic fantasy, are rapidly becoming the norm, promising increased efficiency, reduced costs, and enhanced product quality. This exploration delves into the intricacies of automated factories, examining their components, benefits, challenges, and the future they represent for the manufacturing industry.
The Building Blocks of an Automated Factory
An automated factory is more than just robots on an assembly line. It's a complex ecosystem of interconnected systems working in harmony to optimize the entire production process. Key components include:
1. Robotics and Automation Systems:
- Industrial Robots: These programmable machines perform repetitive tasks with precision and speed, far exceeding human capabilities. From welding and painting to assembly and packaging, robots are transforming every aspect of factory operations. Collaborative robots (cobots) are also gaining traction, working alongside humans to enhance productivity and safety.
- Automated Guided Vehicles (AGVs): These self-navigating vehicles transport materials and goods throughout the factory floor, eliminating manual handling and optimizing logistics. Their use minimizes human error and increases efficiency in material flow.
- Computer Numerical Control (CNC) Machines: These programmable machines use computer-aided design (CAD) and computer-aided manufacturing (CAM) software to precisely manufacture parts according to specifications. CNC machines significantly improve accuracy and reduce waste.
- Automated Storage and Retrieval Systems (AS/RS): These systems automate the storage and retrieval of materials, optimizing warehouse space and minimizing handling time. They're crucial for efficient inventory management in automated factories.
2. Supervisory Control and Data Acquisition (SCADA) Systems:
SCADA systems monitor and control industrial processes in real-time. They collect data from various sensors and machines throughout the factory, providing a comprehensive overview of operations. This allows for proactive maintenance, rapid problem-solving, and continuous process optimization.
3. Manufacturing Execution Systems (MES):
MES software integrates data from various sources, including SCADA systems, ERP systems, and shop floor devices. It provides a holistic view of the production process, enabling better planning, scheduling, and control. MES facilitates real-time tracking of production, ensuring timely completion of orders.
4. Internet of Things (IoT) Integration:
The IoT plays a crucial role in connecting all elements of the automated factory. Sensors embedded in machines and equipment provide real-time data on performance, maintenance needs, and potential issues. This data-driven approach allows for proactive maintenance, reducing downtime and maximizing efficiency.
5. Artificial Intelligence (AI) and Machine Learning (ML):
AI and ML are rapidly transforming automated factories. AI-powered systems can analyze vast amounts of data to identify patterns, predict failures, and optimize production processes. Machine learning algorithms continuously improve their performance, adapting to changing conditions and enhancing efficiency over time.
The Advantages of Automated Factories
The adoption of automation in manufacturing offers numerous benefits:
- Increased Productivity and Efficiency: Automated systems work continuously, without breaks or fatigue, leading to significantly higher output compared to manual processes.
- Reduced Costs: While the initial investment can be substantial, automated factories ultimately reduce labor costs, waste, and defects, leading to long-term cost savings.
- Improved Product Quality and Consistency: Automated systems operate with precision and consistency, minimizing errors and ensuring high-quality products. This enhances brand reputation and customer satisfaction.
- Enhanced Safety: Automation minimizes human exposure to hazardous environments and tasks, reducing workplace accidents and improving safety.
- Increased Flexibility and Adaptability: Modern automated factories can be reprogrammed and reconfigured to produce different products or adapt to changing market demands. This agility is crucial in today's dynamic business environment.
- Better Data Analysis and Decision-Making: Automated systems generate vast amounts of data, providing valuable insights into production processes. This data can be used to optimize operations, improve efficiency, and make informed business decisions.
Challenges in Implementing Automated Factories
Despite the advantages, implementing automated factories presents significant challenges:
- High Initial Investment Costs: The upfront cost of acquiring and installing automation equipment can be substantial, requiring significant capital investment.
- Integration Complexity: Integrating different automation systems and software can be complex and require specialized expertise.
- Maintenance and Repair: Automated systems require regular maintenance and repairs, which can be costly and time-consuming.
- Cybersecurity Risks: Automated factories are vulnerable to cyberattacks, which can disrupt operations and compromise sensitive data. Robust cybersecurity measures are essential.
- Job Displacement Concerns: The automation of manufacturing processes can lead to job displacement for workers performing repetitive tasks. Reskilling and upskilling initiatives are necessary to mitigate this impact.
- Skills Gap: Implementing and maintaining automated factories requires skilled technicians and engineers. A shortage of qualified personnel can hinder the adoption of automation.
The Future of Automated Factories
The future of manufacturing is inextricably linked to the continued advancement of automation. Several key trends are shaping the evolution of automated factories:
- Increased Use of AI and ML: AI and ML will play an increasingly important role in optimizing production processes, predicting failures, and enhancing decision-making.
- Rise of Collaborative Robots (Cobots): Cobots will work alongside humans, enhancing productivity and safety, creating a more collaborative work environment.
- Greater Emphasis on Data Analytics: Data analytics will become even more crucial for optimizing factory operations, identifying bottlenecks, and improving efficiency.
- Focus on Sustainability: Automated factories will incorporate sustainable practices, reducing energy consumption and minimizing environmental impact.
- Growing Adoption of Digital Twins: Digital twins – virtual representations of physical assets – will be used for simulation, optimization, and predictive maintenance.
Conclusion: Embracing the Automated Future
Automated factories represent a significant step forward in manufacturing, offering numerous benefits for businesses and society. While challenges remain, the potential rewards are too significant to ignore. By addressing the challenges and embracing the opportunities, manufacturers can harness the power of automation to create more efficient, productive, and sustainable operations, shaping the future of the industry. The transition requires careful planning, strategic investments, and a commitment to continuous improvement. The future is automated, and those who embrace it will thrive.
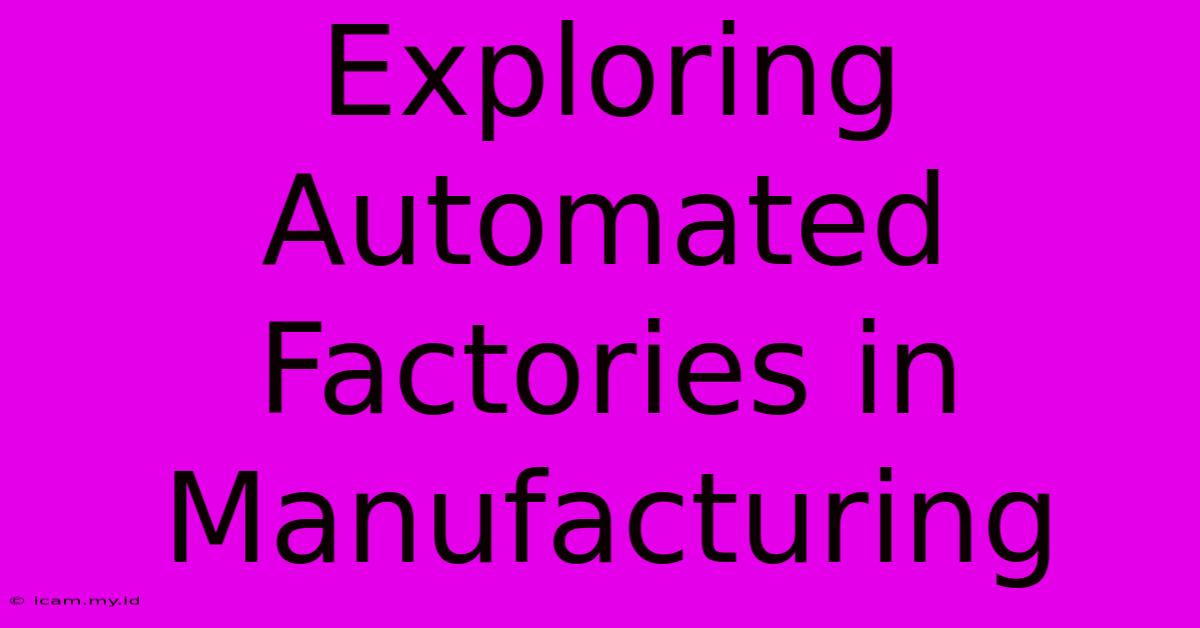
Thank you for visiting our website. Exploring Automated Factories In Manufacturing. We hope the information we provide is helpful to you. Feel free to contact us if you have any questions or need additional assistance. See you next time, and don't forget to save this page!
Kami berterima kasih atas kunjungan Anda untuk melihat lebih jauh. Exploring Automated Factories In Manufacturing. Informasikan kepada kami jika Anda memerlukan bantuan tambahan. Tandai situs ini dan pastikan untuk kembali lagi segera!
Featured Posts
-
Smart Manufacturing Key Concepts
Nov 28, 2024
-
Thailand Tests Selangors New Japanese Coach
Nov 28, 2024
-
Tudm Investigates Palapes Training Death
Nov 28, 2024
-
Autopsies Show Covid Vaccine Issues
Nov 28, 2024
-
Flood Update Km 26 1 South Jitra Closed
Nov 28, 2024