Fundamentals Of Smart Manufacturing
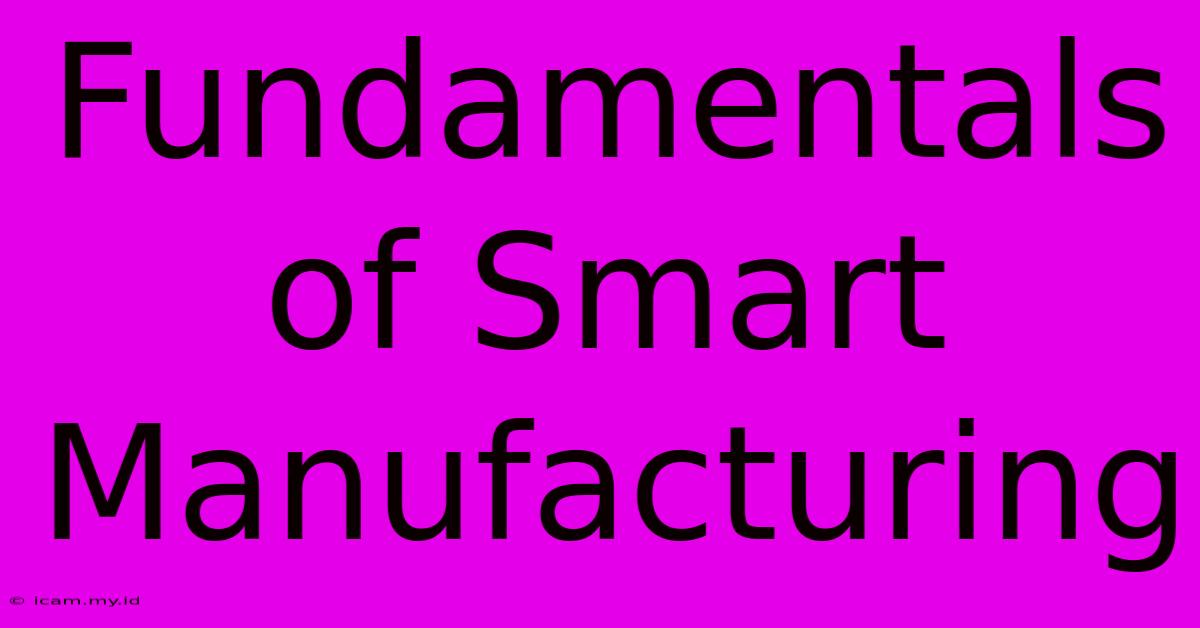
Find more detailed and interesting information on our website. Click the link below to start advanced information: Visit Best Website meltwatermedia.ca. Jangan lewatkan!
Table of Contents
Fundamentals of Smart Manufacturing: A Deep Dive into Industry 4.0
Smart manufacturing, also known as Industry 4.0, represents a significant evolution in how goods are produced. It leverages cutting-edge technologies to create a more efficient, adaptable, and responsive manufacturing environment. Understanding the fundamentals of smart manufacturing is crucial for businesses looking to stay competitive in today's rapidly changing industrial landscape. This comprehensive guide delves into the core principles, key technologies, and benefits of implementing smart manufacturing strategies.
Defining Smart Manufacturing
Smart manufacturing is more than just automating processes; it's about creating an interconnected, data-driven ecosystem within a manufacturing facility. This involves integrating various technologies to optimize every stage of production, from design and planning to manufacturing, delivery, and even product lifecycle management. The ultimate goal is to achieve greater efficiency, flexibility, quality, and profitability. Key characteristics of smart manufacturing include:
- Real-time data visibility: Comprehensive data collection and analysis provides a clear picture of the entire production process, enabling proactive decision-making.
- Predictive maintenance: Sensors and data analytics predict potential equipment failures, minimizing downtime and maintenance costs.
- Automated processes: Robotic process automation (RPA) and other automation technologies reduce manual labor and improve accuracy.
- Enhanced connectivity: The seamless integration of various systems and devices across the value chain facilitates efficient communication and collaboration.
- Data-driven decision making: Data analytics provides insights to optimize production processes, improve quality control, and reduce waste.
Core Technologies Driving Smart Manufacturing
Several technologies underpin the success of smart manufacturing initiatives. Understanding these technologies is crucial for effective implementation:
1. Internet of Things (IoT)
The IoT is foundational to smart manufacturing. It involves connecting machines, sensors, and other devices to a network, enabling real-time data collection and communication. This data provides critical insights into operational efficiency, equipment performance, and product quality. Examples include sensors monitoring machine performance, temperature, and pressure; connected robots sharing data on their operations; and smart devices tracking inventory levels.
2. Cloud Computing
Cloud computing provides the infrastructure for storing, processing, and analyzing the massive amounts of data generated by IoT devices. Cloud platforms offer scalability, flexibility, and cost-effectiveness, making them ideal for supporting smart manufacturing initiatives. Benefits include reduced IT infrastructure costs, enhanced data security, and improved accessibility to data for decision-making.
3. Big Data Analytics
Big data analytics plays a crucial role in extracting meaningful insights from the vast amounts of data collected in smart manufacturing environments. Advanced analytics techniques like machine learning and artificial intelligence are used to identify patterns, predict failures, and optimize processes. This allows manufacturers to make data-driven decisions that improve efficiency and reduce costs. Applications include predictive maintenance, quality control, and supply chain optimization.
4. Artificial Intelligence (AI) and Machine Learning (ML)
AI and ML are transforming smart manufacturing by automating complex tasks, optimizing production processes, and improving decision-making. AI-powered systems can learn from data and adapt to changing conditions, leading to increased efficiency and productivity. Examples include AI-powered quality control systems that automatically identify defects and AI-driven robots that adapt to changing production needs.
5. Cybersecurity
With increased connectivity comes increased risk. Robust cybersecurity measures are essential to protect sensitive data and prevent cyberattacks. This includes implementing strong authentication protocols, using encryption, and regularly updating software. A strong cybersecurity framework is non-negotiable for successful smart manufacturing implementation.
6. Additive Manufacturing (3D Printing)
3D printing offers significant advantages in prototyping, customization, and on-demand manufacturing. It allows for rapid prototyping of new products and components, reducing lead times and costs. Benefits include reduced material waste, increased design flexibility, and the ability to produce highly customized products.
7. Augmented Reality (AR) and Virtual Reality (VR)
AR and VR technologies enhance training, maintenance, and troubleshooting processes. AR overlays digital information onto the real world, guiding technicians through repairs or providing real-time data on equipment performance. VR creates immersive simulations for training purposes, allowing employees to practice complex tasks in a safe environment. Improved efficiency and reduced error rates are key outcomes.
Benefits of Implementing Smart Manufacturing
Implementing smart manufacturing strategies offers a wide range of benefits, including:
- Increased efficiency and productivity: Automation and optimized processes lead to significant improvements in production efficiency and output.
- Improved product quality: Real-time data monitoring and analysis enable early detection and correction of defects, resulting in higher product quality.
- Reduced costs: Predictive maintenance, waste reduction, and optimized resource allocation lead to significant cost savings.
- Enhanced flexibility and agility: Smart manufacturing systems can quickly adapt to changing demands and market conditions.
- Improved supply chain management: Real-time visibility and data analysis improve the efficiency and responsiveness of the supply chain.
- Better decision-making: Data-driven insights empower manufacturers to make more informed and effective decisions.
- Increased innovation: The data collected allows for continuous improvement and the development of new and innovative products and processes.
- Enhanced worker safety: Automation of hazardous tasks and real-time monitoring of equipment improve worker safety.
- Improved customer satisfaction: Higher product quality and faster delivery times lead to improved customer satisfaction.
Challenges in Implementing Smart Manufacturing
Despite the numerous benefits, implementing smart manufacturing faces several challenges:
- High initial investment costs: The implementation of new technologies and infrastructure can require significant upfront investments.
- Integration complexities: Integrating various systems and technologies can be complex and time-consuming.
- Data security concerns: Protecting sensitive data from cyberattacks is crucial, requiring robust cybersecurity measures.
- Lack of skilled workforce: Implementing smart manufacturing requires a skilled workforce capable of operating and maintaining new technologies.
- Legacy systems incompatibility: Integrating new technologies with existing legacy systems can be challenging.
- Resistance to change: Implementing new technologies often requires changes in processes and workflows, which may face resistance from employees.
Conclusion: Embracing the Future of Manufacturing
Smart manufacturing is not simply a trend; it is the future of manufacturing. By embracing these technologies and addressing the associated challenges, manufacturers can unlock significant improvements in efficiency, quality, and profitability. The journey towards smart manufacturing requires a strategic approach, careful planning, and a commitment to continuous improvement. Companies that successfully integrate these principles will be well-positioned to thrive in the increasingly competitive global marketplace. Investing in training, developing robust cybersecurity protocols, and focusing on data integration are critical steps towards successful implementation. The potential rewards far outweigh the challenges, making smart manufacturing a vital investment for the future of any manufacturing organization.
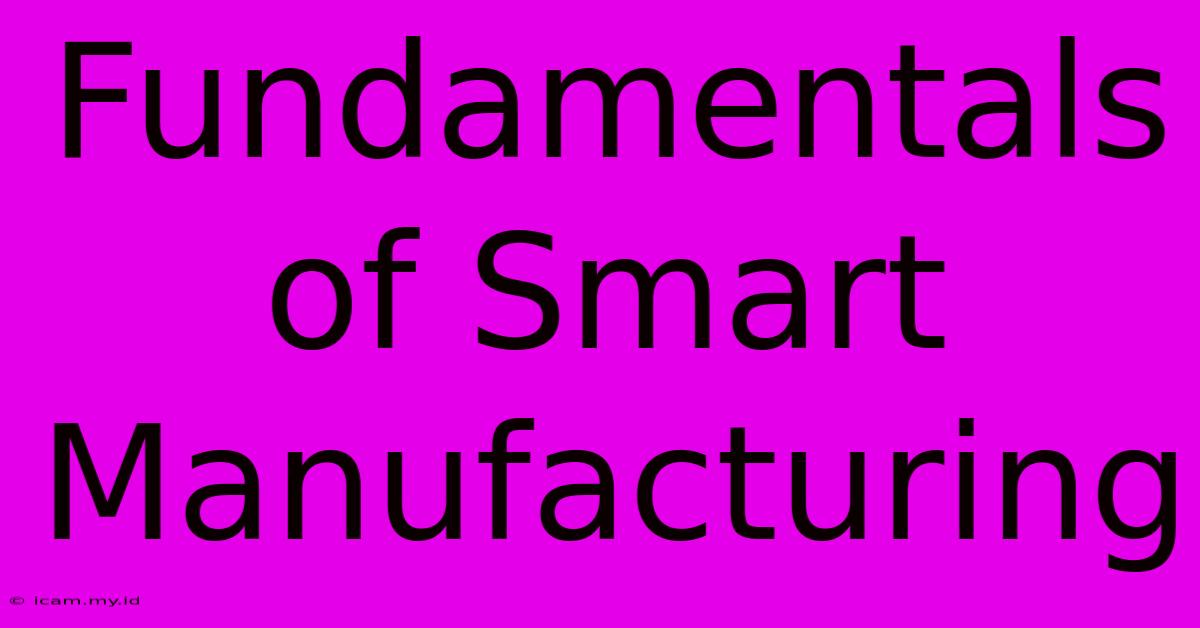
Thank you for visiting our website. Fundamentals Of Smart Manufacturing. We hope the information we provide is helpful to you. Feel free to contact us if you have any questions or need additional assistance. See you next time, and don't forget to save this page!
Kami berterima kasih atas kunjungan Anda untuk melihat lebih jauh. Fundamentals Of Smart Manufacturing. Informasikan kepada kami jika Anda memerlukan bantuan tambahan. Tandai situs ini dan pastikan untuk kembali lagi segera!
Featured Posts
-
Death Sentence Looms Vietnam Tycoons Debt
Nov 28, 2024
-
Smart Factories Economic Advantages
Nov 28, 2024
-
Passing Of Ananda Krishnan Malaysian Billionaire
Nov 28, 2024
-
Selangors Acl 2 Challenge Round 16 Qualification
Nov 28, 2024
-
Vietnam Tycoon Faces Death For 27 B Fraud
Nov 28, 2024