Gaining Economic Edge: Smart Factories
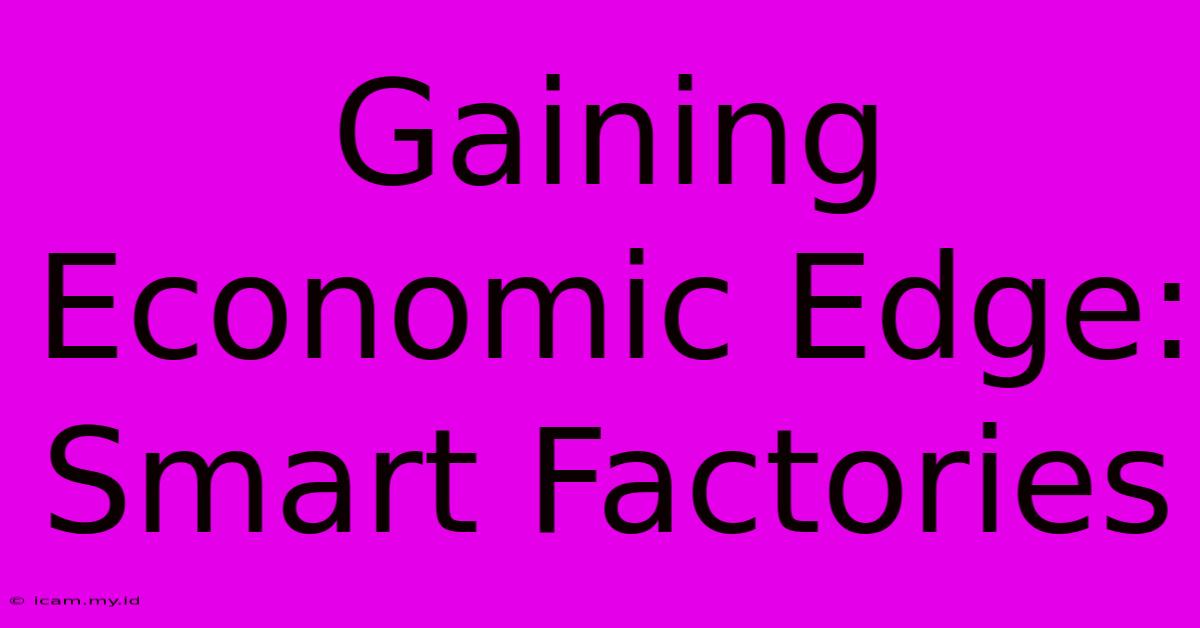
Find more detailed and interesting information on our website. Click the link below to start advanced information: Visit Best Website meltwatermedia.ca. Jangan lewatkan!
Table of Contents
Gaining an Economic Edge: Smart Factories – The Future of Manufacturing
The global manufacturing landscape is undergoing a dramatic transformation. No longer is it enough to simply produce goods efficiently; businesses need to be smart, adaptable, and deeply data-driven to thrive. This is where the smart factory comes into play, offering a powerful pathway to gaining a significant economic edge. This comprehensive guide delves into the intricacies of smart factories, exploring their key components, benefits, and the challenges involved in their implementation.
What is a Smart Factory?
A smart factory, also known as an intelligent factory or Industry 4.0 factory, leverages cutting-edge technologies to optimize every aspect of the manufacturing process. This goes beyond automation; it involves integrating data analytics, machine learning, the Internet of Things (IoT), cloud computing, and advanced robotics to create a highly interconnected and responsive production environment. Instead of isolated machines, a smart factory features a seamless network of interconnected systems communicating and collaborating in real-time.
Core Components of a Smart Factory:
Several key technologies form the backbone of a successful smart factory implementation:
-
Internet of Things (IoT): Sensors embedded in machines, equipment, and products constantly collect data on performance, maintenance needs, and production output. This real-time data flow is crucial for informed decision-making.
-
Big Data Analytics: The vast amounts of data generated by IoT devices are analyzed using sophisticated algorithms to identify trends, predict potential issues, and optimize processes for maximum efficiency. This predictive maintenance, for example, significantly reduces downtime.
-
Cloud Computing: The cloud provides the scalable infrastructure needed to store, process, and analyze the massive datasets generated by a smart factory. It also facilitates remote access and collaboration.
-
Artificial Intelligence (AI) and Machine Learning (ML): AI and ML algorithms power predictive analytics, optimize production schedules, improve quality control, and automate complex tasks. This allows for continuous improvement and adaptation to changing demands.
-
Robotics and Automation: Robots and automated systems perform repetitive or hazardous tasks, increasing efficiency, productivity, and worker safety. Advanced collaborative robots (cobots) work alongside human employees, enhancing their capabilities.
-
Cybersecurity: With the increased connectivity comes the need for robust cybersecurity measures to protect sensitive data and prevent disruptions. This is paramount to maintain operational integrity and trust.
-
Advanced Manufacturing Execution Systems (MES): MES software integrates and manages various aspects of the manufacturing process, providing real-time visibility and control.
Economic Benefits of Smart Factories:
The transition to a smart factory offers compelling economic advantages:
-
Increased Productivity and Efficiency: Automation and optimized processes significantly boost production output while minimizing waste and reducing operational costs.
-
Improved Quality Control: Real-time data monitoring and AI-powered quality checks minimize defects and improve product consistency. This leads to enhanced customer satisfaction and reduced warranty claims.
-
Reduced Downtime and Maintenance Costs: Predictive maintenance, based on data analysis, allows for proactive interventions, preventing unexpected equipment failures and minimizing downtime.
-
Enhanced Flexibility and Adaptability: Smart factories are capable of quickly adapting to changing market demands and customer preferences, enabling faster response times and improved competitiveness.
-
Optimized Supply Chain Management: Improved data visibility across the supply chain allows for better inventory management, streamlined logistics, and reduced lead times.
-
Data-Driven Decision Making: Real-time data insights empower managers to make informed decisions, leading to more effective resource allocation and strategic planning.
-
Improved Employee Skillsets: Smart factories necessitate a workforce with advanced digital skills, creating opportunities for upskilling and reskilling initiatives. This also attracts and retains talent.
-
Enhanced Sustainability: Smart factories often incorporate energy-efficient technologies and processes, leading to reduced environmental impact and lower energy costs.
Challenges in Implementing Smart Factories:
Despite the numerous benefits, implementing a smart factory presents several challenges:
-
High Initial Investment Costs: The adoption of advanced technologies requires significant upfront investment in hardware, software, and integration services.
-
Data Security and Privacy Concerns: The increased connectivity and data sharing necessitate robust cybersecurity measures to protect sensitive information and comply with relevant regulations.
-
Integration Complexity: Integrating various systems and technologies can be complex and time-consuming, requiring specialized expertise.
-
Workforce Upskilling and Reskilling: The transition to a smart factory demands a workforce with the skills to operate and maintain advanced technologies. This requires substantial investment in training and development programs.
-
Lack of Skilled Personnel: A shortage of qualified personnel with expertise in areas such as data analytics, AI, and cybersecurity can hinder implementation efforts.
-
Legacy System Integration: Integrating new technologies with existing legacy systems can be challenging and costly.
-
Resistance to Change: Overcoming resistance to change from employees and management is crucial for successful implementation.
Strategies for Successful Smart Factory Implementation:
To maximize the chances of successful implementation, organizations should consider the following strategies:
-
Start Small and Scale Gradually: Begin with a pilot project focusing on a specific area or process to gain experience and identify potential challenges before undertaking a full-scale transformation.
-
Develop a Clear Roadmap and Strategy: Establish a well-defined roadmap with clear goals, timelines, and key performance indicators (KPIs) to guide the implementation process.
-
Invest in Employee Training and Development: Provide comprehensive training programs to equip employees with the skills needed to operate and maintain new technologies.
-
Choose the Right Technology Partners: Select reliable technology partners with proven expertise in smart factory solutions.
-
Prioritize Cybersecurity: Implement robust cybersecurity measures to protect sensitive data and prevent disruptions.
-
Foster Collaboration and Communication: Encourage collaboration and communication between different departments and stakeholders throughout the implementation process.
-
Continuously Monitor and Improve: Regularly monitor performance, collect feedback, and make adjustments to optimize the smart factory's operation.
Conclusion:
Smart factories represent a paradigm shift in manufacturing, offering unparalleled opportunities for businesses to gain a significant economic edge in an increasingly competitive global market. While implementing a smart factory presents challenges, the potential benefits—increased productivity, improved quality, reduced costs, and enhanced adaptability—make it a worthwhile investment for companies seeking to thrive in the future of manufacturing. By carefully planning, investing wisely, and embracing a culture of continuous improvement, organizations can harness the power of smart factories to unlock new levels of efficiency and profitability. The future of manufacturing is smart, and businesses that embrace this transformation will be well-positioned for sustained success.
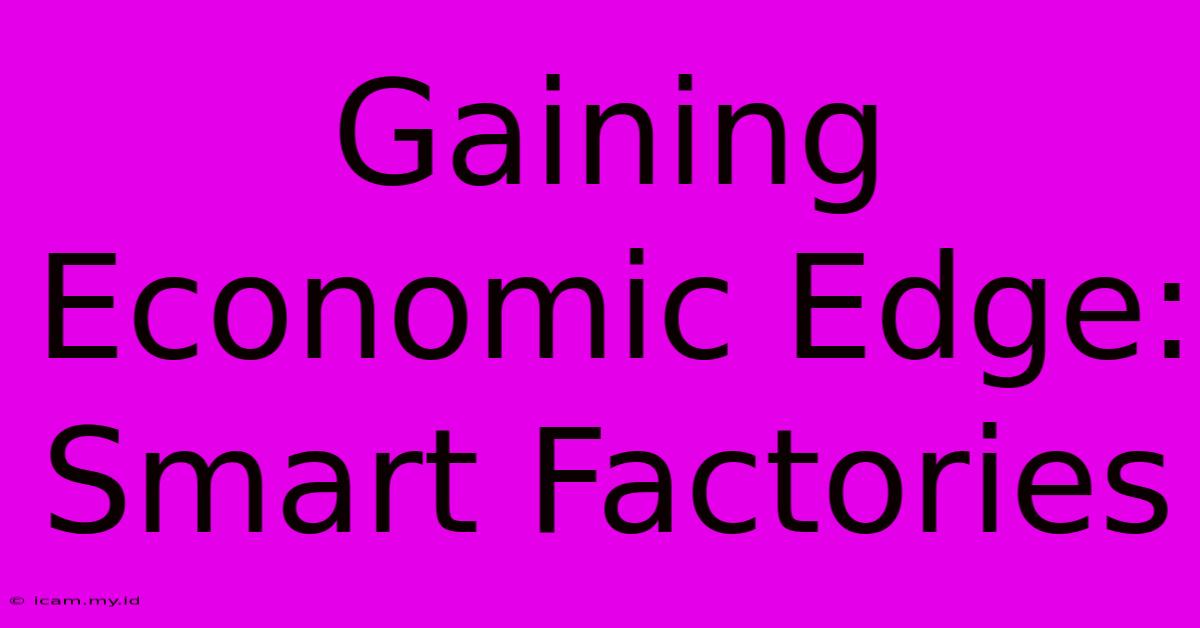
Thank you for visiting our website. Gaining Economic Edge: Smart Factories. We hope the information we provide is helpful to you. Feel free to contact us if you have any questions or need additional assistance. See you next time, and don't forget to save this page!
Kami berterima kasih atas kunjungan Anda untuk melihat lebih jauh. Gaining Economic Edge: Smart Factories. Informasikan kepada kami jika Anda memerlukan bantuan tambahan. Tandai situs ini dan pastikan untuk kembali lagi segera!
Featured Posts
-
New Social Media Law Australia Bans Under 16s
Nov 28, 2024
-
Salahs Away Goals 100 For Liverpool
Nov 28, 2024
-
Failure To Perform Cpr Palapes Coach Fined
Nov 28, 2024
-
Yishun Welcomes Tous Les Jours Bakery
Nov 28, 2024
-
Bioinformatics Market Future Growth Prospects
Nov 28, 2024