Impact Of Automated Factories On Manufacturing
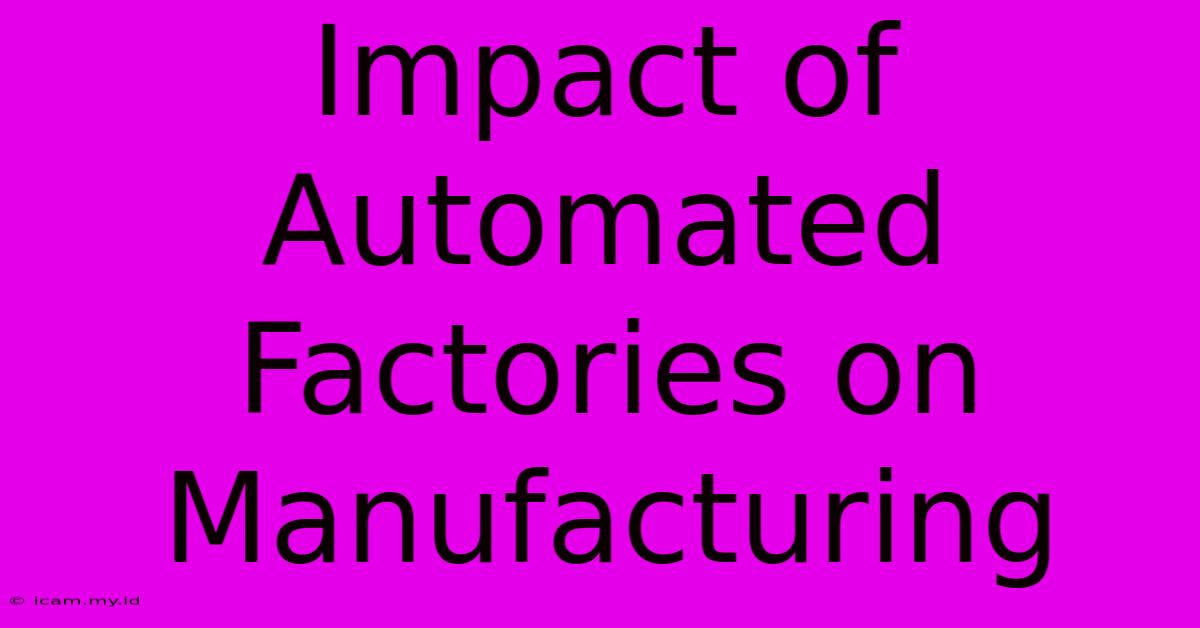
Find more detailed and interesting information on our website. Click the link below to start advanced information: Visit Best Website meltwatermedia.ca. Jangan lewatkan!
Table of Contents
The Impact of Automated Factories on Manufacturing: A Deep Dive into the Fourth Industrial Revolution
The manufacturing landscape is undergoing a dramatic transformation, driven by the rapid advancement and adoption of automation technologies. This shift, often referred to as the Fourth Industrial Revolution (Industry 4.0), is fundamentally altering how goods are produced, impacting everything from production efficiency and worker roles to global supply chains and economic competitiveness. This article delves into the profound impact of automated factories on manufacturing, exploring both the benefits and challenges associated with this technological revolution.
The Rise of the Automated Factory: Key Technologies Driving Change
Automated factories leverage a range of cutting-edge technologies to optimize production processes. These include:
- Robotics: Industrial robots perform repetitive tasks with greater speed, precision, and consistency than human workers. From welding and painting to assembly and packaging, robots are transforming manufacturing operations across diverse sectors.
- Computer Numerical Control (CNC) Machines: CNC machines use computer programs to guide their movements, enabling the precise machining of complex parts. This enhances accuracy, reduces waste, and allows for greater flexibility in production.
- Artificial Intelligence (AI) and Machine Learning (ML): AI and ML algorithms are increasingly integrated into factory systems, enabling predictive maintenance, quality control, and process optimization. These technologies analyze vast datasets to identify patterns and anomalies, leading to improved efficiency and reduced downtime.
- Internet of Things (IoT): The IoT connects machines, sensors, and other devices within the factory, enabling real-time data collection and analysis. This facilitates better monitoring, control, and decision-making across the entire production process.
- 3D Printing (Additive Manufacturing): 3D printing allows for the creation of customized parts on demand, reducing lead times and inventory costs. This technology is particularly beneficial for prototyping and the production of low-volume, high-value components.
- Automated Guided Vehicles (AGVs): AGVs transport materials and products within the factory, optimizing logistics and reducing manual handling. These autonomous vehicles navigate using various technologies, including magnetic stripes, lasers, and vision systems.
- Computer-Aided Design/Computer-Aided Manufacturing (CAD/CAM): CAD/CAM software integrates design and manufacturing processes, streamlining the entire production cycle and reducing errors.
Benefits of Automated Factories: Enhanced Efficiency and Productivity
The adoption of automation technologies in manufacturing offers numerous benefits, significantly impacting productivity and efficiency:
- Increased Productivity: Automated systems operate continuously, without breaks or fatigue, leading to significantly higher output compared to manual labor. This increased productivity is crucial in meeting growing consumer demand and maintaining competitiveness in a global market.
- Improved Quality and Consistency: Automated systems consistently perform tasks according to pre-programmed specifications, minimizing errors and ensuring consistent product quality. This reduces waste, rework, and customer complaints.
- Reduced Costs: While the initial investment in automation can be substantial, the long-term cost savings can be considerable. Automation reduces labor costs, waste, and downtime, contributing to improved profitability.
- Enhanced Safety: Automation minimizes the risk of workplace accidents associated with repetitive or hazardous tasks. This creates a safer working environment for human employees.
- Improved Flexibility and Adaptability: Automated systems can be reprogrammed to adapt to changing production requirements, enabling manufacturers to respond quickly to market demands and produce a wider range of products.
- Data-Driven Decision Making: The data collected by automated systems provides valuable insights into production processes, enabling data-driven decision making and continuous improvement.
Challenges of Implementing Automated Factories: Costs and Workforce Transition
Despite the significant benefits, implementing automated factories presents several challenges:
- High Initial Investment Costs: The upfront cost of purchasing and installing automation technologies can be substantial, requiring significant capital investment. This can be a barrier to entry for smaller manufacturers.
- Integration Complexity: Integrating different automation technologies into a cohesive system can be complex and require specialized expertise. This necessitates careful planning and skilled technicians.
- Cybersecurity Risks: Automated factories rely heavily on networked systems, increasing their vulnerability to cyberattacks. Robust cybersecurity measures are crucial to protecting sensitive data and preventing disruptions.
- Workforce Transition: The adoption of automation can lead to job displacement in certain areas. Retraining and reskilling programs are essential to support workers in transitioning to new roles within the automated factory environment. This requires proactive planning and investment in education and training initiatives.
- Maintenance and Repair Costs: Maintaining and repairing automated systems requires specialized skills and expertise, leading to ongoing maintenance costs. This needs to be factored into the overall cost analysis.
- Lack of Skilled Labor: The increasing demand for skilled technicians and engineers to design, implement, and maintain automated systems creates a significant skills gap. Addressing this requires investment in education and training programs.
The Future of Automated Factories: Collaboration Between Humans and Machines
The future of manufacturing lies in a collaborative approach, where humans and machines work together to leverage their respective strengths. This involves:
- Cobots (Collaborative Robots): Cobots are designed to work alongside human workers, assisting with tasks that require both human dexterity and robotic precision. This allows for a synergistic combination of human intelligence and robotic capabilities.
- Human-Machine Interfaces (HMIs): Improved HMIs facilitate easier interaction between humans and machines, simplifying the operation and maintenance of automated systems.
- AI-Powered Training and Support: AI can provide real-time training and support to human workers, enhancing their skills and efficiency.
Conclusion: Embracing the Transformation
The impact of automated factories on manufacturing is undeniable. While challenges exist, the benefits of increased productivity, improved quality, and reduced costs are significant. By addressing the challenges proactively and focusing on a collaborative human-machine approach, manufacturers can harness the full potential of automation to thrive in the Fourth Industrial Revolution. The successful implementation of automation hinges on strategic planning, investment in technology and workforce development, and a willingness to embrace the transformative potential of this technological revolution. This evolution will not only redefine manufacturing processes but also reshape the very nature of work itself, requiring adaptability and a commitment to continuous learning and innovation.
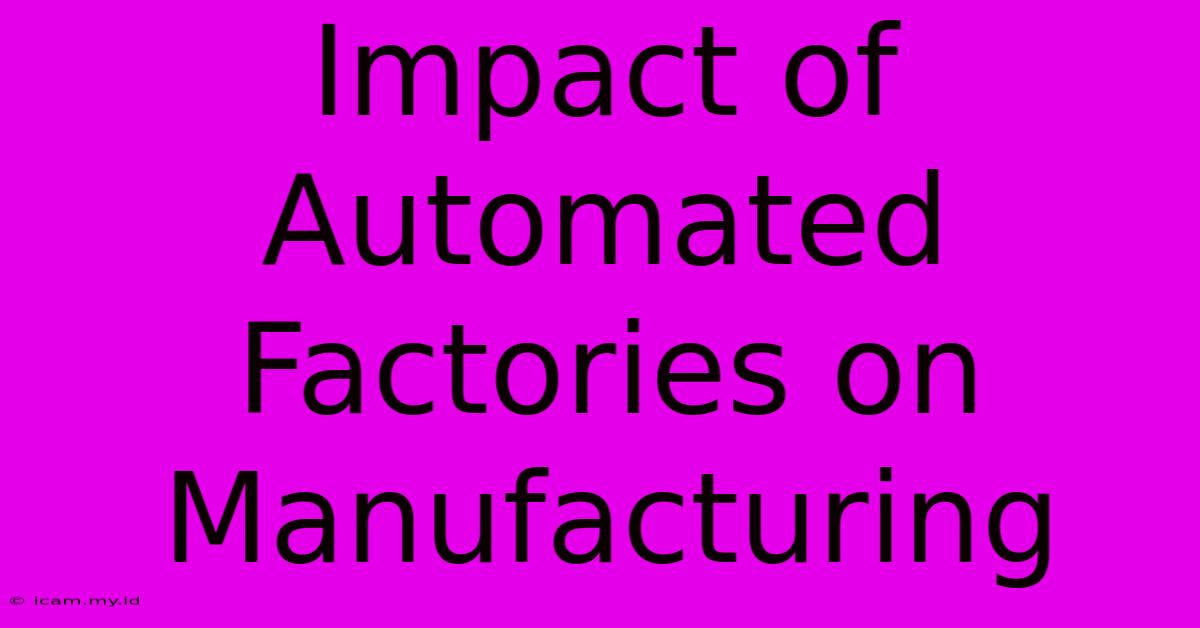
Thank you for visiting our website. Impact Of Automated Factories On Manufacturing. We hope the information we provide is helpful to you. Feel free to contact us if you have any questions or need additional assistance. See you next time, and don't forget to save this page!
Kami berterima kasih atas kunjungan Anda untuk melihat lebih jauh. Impact Of Automated Factories On Manufacturing. Informasikan kepada kami jika Anda memerlukan bantuan tambahan. Tandai situs ini dan pastikan untuk kembali lagi segera!
Featured Posts
-
Global Competition For Rare Earths
Nov 28, 2024
-
Report Malaysian Billionaire Krishnan Is Dead
Nov 28, 2024
-
Songkhla Yala Flooding Affects 100 Households
Nov 28, 2024
-
Former Real Madrid Player Wins Golden Man
Nov 28, 2024
-
2024 Bioinformatics Market Size Share
Nov 28, 2024