Industrial Adsorbents Recover Lanthanum
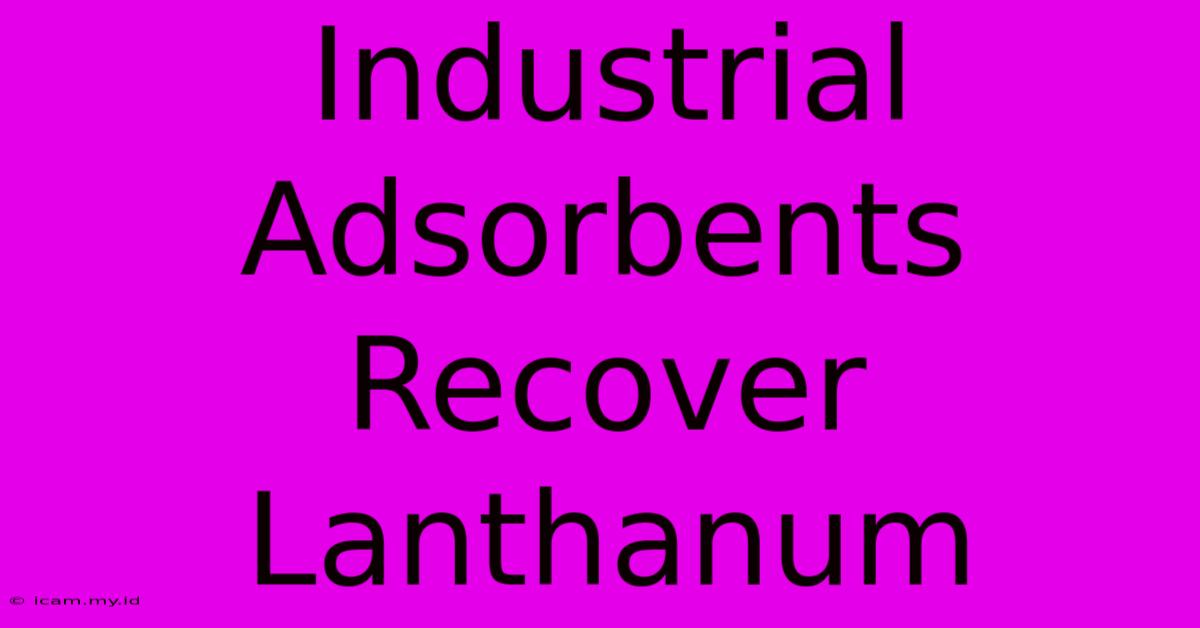
Find more detailed and interesting information on our website. Click the link below to start advanced information: Visit Best Website meltwatermedia.ca. Jangan lewatkan!
Table of Contents
Industrial Adsorbents Recover Lanthanum: A Comprehensive Guide
The recovery of rare earth elements (REEs) like lanthanum from industrial waste streams is crucial for sustainable resource management and reducing reliance on primary mining. Lanthanum, specifically, finds extensive applications in various industries, including catalysis, electronics, and energy storage. This article delves into the effective utilization of industrial adsorbents for the efficient and environmentally friendly recovery of lanthanum. We will explore different adsorbent materials, their mechanisms of action, and the optimization strategies for maximizing lanthanum recovery.
Understanding the Importance of Lanthanum Recovery
Lanthanum, a vital REE, is not readily available in its pure form. Traditional mining methods are often energy-intensive and environmentally damaging. Furthermore, geopolitical factors can significantly impact the supply chain, highlighting the need for alternative and sustainable sourcing strategies. Industrial waste streams, such as those generated from the processing of electronic waste (e-waste), spent catalysts, and metallurgical processes, often contain significant amounts of lanthanum. Recovering this lanthanum from waste presents a significant opportunity for:
- Resource Conservation: Reducing the demand for primary mining, thus minimizing environmental impact.
- Economic Benefits: Extracting valuable resources from waste streams, generating economic value from waste materials.
- Environmental Sustainability: Promoting a circular economy by recycling valuable REEs and reducing landfill waste.
Challenges in Lanthanum Recovery
Despite the advantages, recovering lanthanum from complex industrial waste streams poses several challenges:
- Low Concentrations: Lanthanum is often present in low concentrations, making its separation and recovery challenging.
- Matrix Complexity: Waste streams typically contain various other metals and compounds, creating a complex matrix that complicates the separation process.
- Cost-Effectiveness: The recovery process needs to be cost-effective to be commercially viable. The cost of adsorbents and the energy required for the process must be carefully considered.
Industrial Adsorbents: The Key Players
Industrial adsorbents play a pivotal role in efficiently separating and recovering lanthanum from complex waste streams. These materials have a high surface area and specific binding sites that selectively adsorb lanthanum ions from the solution. Several types of adsorbents are currently being explored, each with its own advantages and disadvantages:
1. Activated Carbon: A Versatile Choice
Activated carbon, a widely used adsorbent, possesses a highly porous structure with a large surface area, making it suitable for adsorbing various ions, including lanthanum. Its cost-effectiveness and availability contribute to its popularity. However, its adsorption capacity for lanthanum may be limited compared to other specialized adsorbents. Modifications, such as surface functionalization with specific groups, can enhance its lanthanum adsorption capacity.
2. Ion Exchange Resins: High Selectivity
Ion exchange resins are polymeric materials containing functional groups that can exchange ions with the surrounding solution. They offer high selectivity for specific ions, including lanthanum, depending on the nature of the functional groups. The selectivity can be tailored by choosing resins with specific functional groups, leading to efficient lanthanum separation even from complex matrices. However, the cost of ion exchange resins can be higher compared to activated carbon.
3. Metal-Organic Frameworks (MOFs): Tailor-Made Adsorption
Metal-organic frameworks (MOFs) are crystalline porous materials composed of metal ions or clusters coordinated to organic ligands. The highly customizable nature of MOFs allows for the design of materials with specific pore sizes and functional groups to achieve high selectivity and adsorption capacity for lanthanum. This tunability offers significant advantages in tailoring the adsorbent for specific waste streams and optimizing lanthanum recovery. However, the synthesis of MOFs can be complex and costly.
4. Bio-Adsorbents: Sustainable Solutions
Bio-adsorbents, derived from biological sources such as agricultural waste, algae, and bacteria, are emerging as sustainable and cost-effective alternatives to conventional adsorbents. These materials possess various functional groups that can bind to lanthanum ions. Their use contributes to waste reduction and promotes environmentally friendly recovery processes. However, their adsorption capacity and selectivity might need optimization for efficient lanthanum recovery.
Optimizing Lanthanum Recovery using Adsorbents
Optimizing the adsorption process is crucial for maximizing lanthanum recovery. Several factors influence the efficiency of the process:
- pH: The pH of the solution significantly impacts the adsorption capacity. The optimal pH needs to be determined experimentally for each adsorbent and waste stream.
- Contact Time: Sufficient contact time between the adsorbent and the solution is necessary to achieve equilibrium.
- Adsorbent Dosage: The amount of adsorbent used affects the adsorption capacity. An optimal dosage needs to be determined to balance efficiency and cost.
- Temperature: Temperature can influence the adsorption kinetics and equilibrium.
- Desorption: Efficient desorption of lanthanum from the loaded adsorbent is crucial for recovering the valuable metal. Various desorption techniques, such as acid leaching or using complexing agents, can be employed.
Future Directions and Conclusion
The recovery of lanthanum from industrial waste streams using advanced adsorbents holds immense potential for sustainable resource management. Further research focusing on developing novel adsorbents with enhanced selectivity and capacity, exploring innovative desorption techniques, and optimizing process parameters is vital. The development of cost-effective and environmentally friendly processes is crucial for widespread adoption of these technologies. The integration of these technologies into industrial recycling processes will significantly contribute to a circular economy and reduce our dependence on primary REE mining. Continued research and development in this area are essential for ensuring the long-term sustainability of lanthanum supply and minimizing environmental impact. The combination of effective adsorbents and optimized processes offers a promising pathway towards a more sustainable and secure future for lanthanum resource management. The ongoing exploration of novel materials and optimization strategies promises even greater efficiency and cost-effectiveness in the future, making lanthanum recovery from industrial waste streams a key element in a sustainable materials economy.
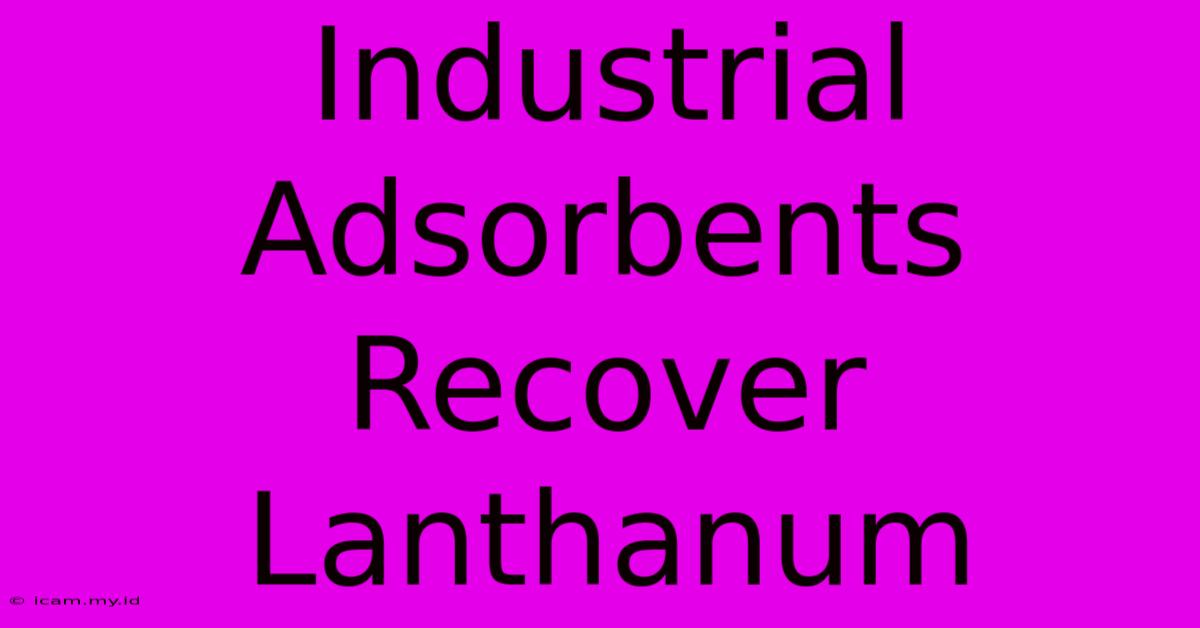
Thank you for visiting our website. Industrial Adsorbents Recover Lanthanum. We hope the information we provide is helpful to you. Feel free to contact us if you have any questions or need additional assistance. See you next time, and don't forget to save this page!
Kami berterima kasih atas kunjungan Anda untuk melihat lebih jauh. Industrial Adsorbents Recover Lanthanum. Informasikan kepada kami jika Anda memerlukan bantuan tambahan. Tandai situs ini dan pastikan untuk kembali lagi segera!
Featured Posts
-
Southern Thailand Floods Impact 100 Residences
Nov 28, 2024
-
Fast Changes Kinos Red Giant Strategy
Nov 28, 2024
-
Tycoon Ananda Krishnan Death Announced
Nov 28, 2024
-
Australias Kid Social Media Ban Imminent
Nov 28, 2024
-
Real Madrids Loss Vinicius Jr Vs Liverpool
Nov 28, 2024