Lanthanum Recovery From E-waste
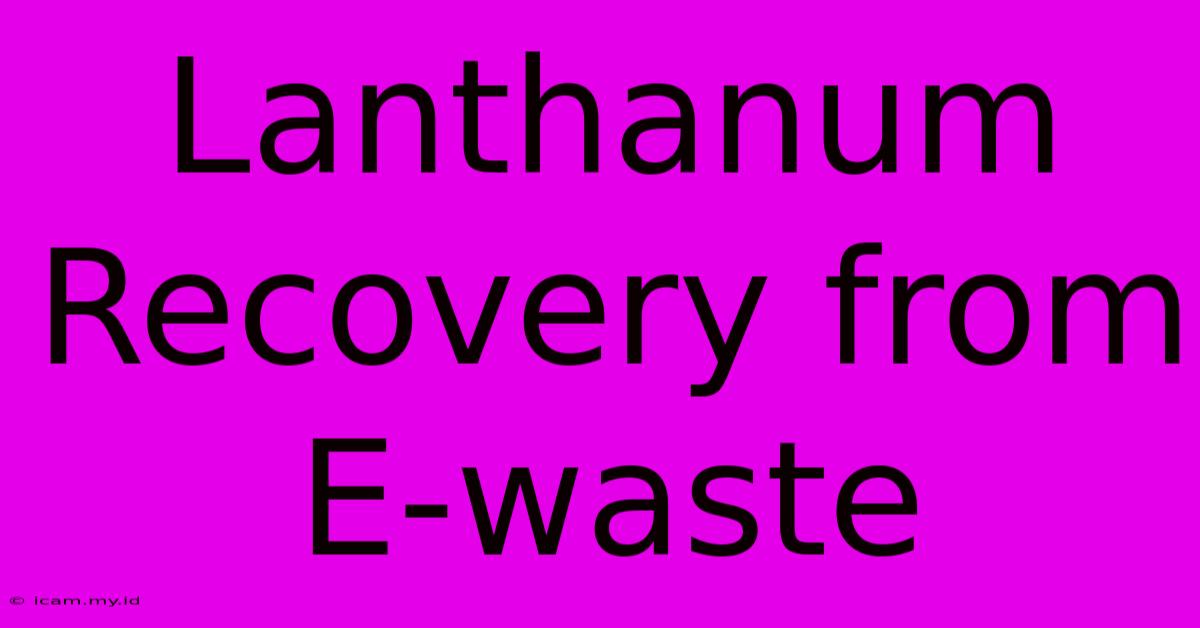
Find more detailed and interesting information on our website. Click the link below to start advanced information: Visit Best Website meltwatermedia.ca. Jangan lewatkan!
Table of Contents
Lanthanum Recovery from E-waste: A Comprehensive Guide
The growing demand for high-tech devices and the subsequent surge in electronic waste (e-waste) present both a significant environmental challenge and a lucrative opportunity. E-waste contains valuable materials, including rare earth elements (REEs) like lanthanum (La), crucial for various technological applications. This article delves into the crucial process of lanthanum recovery from e-waste, exploring the challenges, existing technologies, and future prospects of this environmentally responsible and economically viable endeavor.
Understanding the Importance of Lanthanum
Lanthanum, a silvery-white metal belonging to the lanthanide series, is not as widely known as other REEs like neodymium or dysprosium. However, its significance in modern technology is undeniable. Lanthanum finds applications in:
- Hybrid vehicle batteries: Lanthanum-based nickel-metal hydride (NiMH) batteries power numerous hybrid vehicles. The increasing demand for electric and hybrid vehicles directly translates to a greater need for lanthanum.
- Catalysis: Lanthanum oxide is used as a catalyst in various industrial processes, including petroleum cracking and the production of synthetic fuels.
- Ceramics and glass: Lanthanum improves the refractive index and durability of special glasses and optical lenses. It also enhances the strength and properties of various high-performance ceramics.
- Lighting: Lanthanum-doped fluorescent lamps improve their efficiency and brightness.
The limited availability of lanthanum and its concentration in complex e-waste matrices make its recovery a critical area of research and development.
Challenges in Lanthanum Recovery from E-waste
Recovering lanthanum from e-waste presents several formidable challenges:
- Complexity of e-waste composition: E-waste is a heterogeneous mixture of various materials, including plastics, metals, and different types of electronic components. Separating lanthanum from this complex matrix is a significant hurdle.
- Low concentration of lanthanum: Lanthanum is often present in relatively low concentrations within e-waste components, requiring efficient and selective separation techniques.
- Co-existence of other REEs: E-waste contains other REEs, which often have similar chemical properties to lanthanum, making their separation challenging. The separation process needs to be highly selective to ensure high purity lanthanum recovery.
- Environmental concerns: Conventional methods of REE extraction can have significant environmental impacts. Developing sustainable and environmentally friendly lanthanum recovery methods is essential.
Existing Technologies for Lanthanum Recovery
Several methods are being explored for lanthanum recovery from e-waste, each with its own advantages and drawbacks:
1. Hydrometallurgical Processes: These processes involve leaching the e-waste with acidic or alkaline solutions to dissolve the lanthanum and other valuable metals. Subsequent steps involve separation and purification techniques, such as solvent extraction, ion exchange, and precipitation. Hydrometallurgy offers flexibility and can handle a variety of e-waste materials. However, it can generate significant amounts of wastewater requiring careful treatment.
2. Pyrometallurgical Processes: This method involves high-temperature treatments like smelting or incineration to separate and recover valuable metals from e-waste. Pyrometallurgy can achieve high recovery rates but often results in the formation of hazardous byproducts requiring effective management.
3. Bioleaching: This environmentally friendly approach utilizes microorganisms to dissolve metals from e-waste. Bioleaching is relatively slow but produces less waste and requires lower energy consumption compared to hydro- or pyrometallurgical methods. Research is ongoing to optimize bioleaching for lanthanum recovery from complex e-waste matrices.
4. Selective Dissolution: This method focuses on selectively dissolving lanthanum from the e-waste matrix, minimizing the dissolution of other unwanted materials. This approach aims to increase the efficiency and reduce the complexity of the subsequent separation steps. The specific approach depends on the chemical properties of the e-waste material and the chosen solvent.
5. Combined Methods: Often, a combination of different methods is used to maximize recovery efficiency. For instance, a combination of mechanical pre-treatment (e.g., shredding, sorting) followed by hydrometallurgical processes is common. This strategy helps to simplify the overall process and enhance the efficiency of lanthanum extraction.
Future Prospects and Research Directions
Research in lanthanum recovery from e-waste is focused on several key areas:
- Developing more efficient and selective separation techniques: Improving the efficiency of solvent extraction, ion exchange, and other separation methods is crucial for cost-effective lanthanum recovery. Research into novel separation technologies like membrane separation and supercritical fluid extraction is also underway.
- Minimizing environmental impact: The development of cleaner and more sustainable processes is essential. This includes minimizing waste generation, reducing energy consumption, and preventing the release of harmful pollutants.
- Improving the scalability and economic viability of recovery processes: Scaling up laboratory-scale processes to industrial-scale operations requires significant research and development efforts. The economic viability of lanthanum recovery needs to be carefully considered to ensure the long-term success of these technologies.
- Exploring new e-waste sources: Investigating new sources of lanthanum in e-waste, such as specific types of electronics or components with high lanthanum content, can significantly enhance the efficiency of recovery processes.
- Life cycle assessment of recovery processes: A comprehensive life cycle assessment (LCA) is essential to fully understand the environmental impact of different lanthanum recovery technologies, including energy consumption, waste generation, and greenhouse gas emissions.
Conclusion
Lanthanum recovery from e-waste is a critical area of research and development with significant environmental and economic benefits. While challenges remain, advancements in separation technologies and sustainable processing methods offer promising avenues for efficient and environmentally friendly lanthanum recovery. Continued research and development efforts are needed to overcome these challenges and realize the full potential of e-waste as a valuable source of this essential rare earth element. The successful implementation of these technologies will contribute to a circular economy, minimizing environmental damage and securing a sustainable supply of critical materials for future technological advancements. The future of lanthanum extraction will likely involve optimized combinations of existing techniques and the development of entirely novel approaches, driven by the increasing urgency of responsible resource management and the growing global demand for lanthanum.
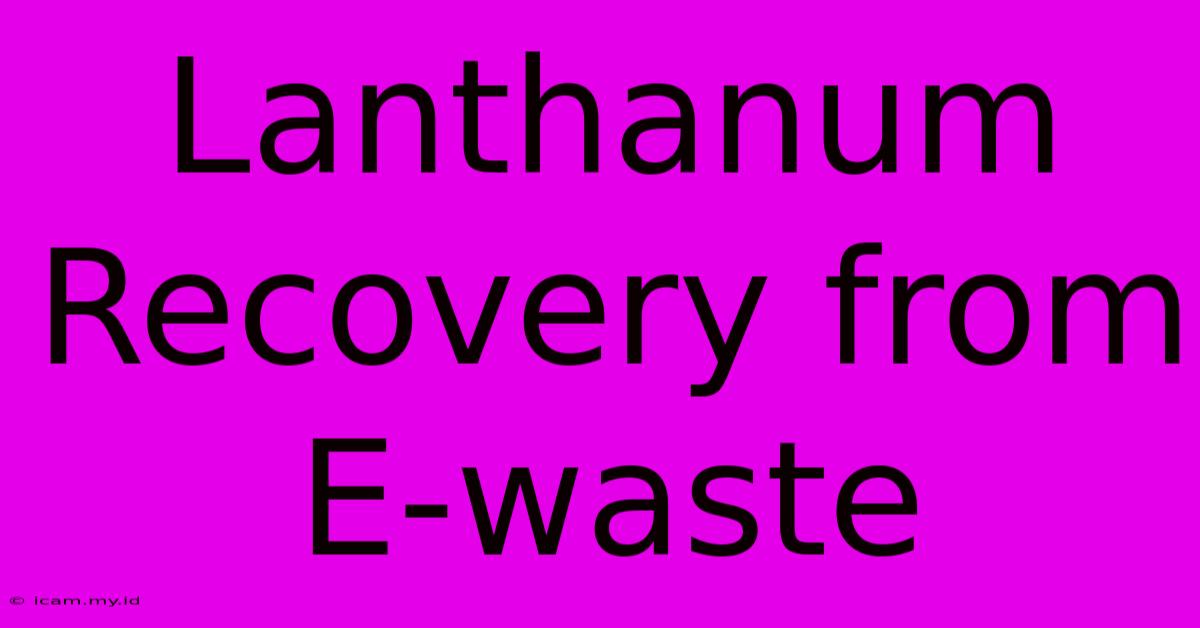
Thank you for visiting our website. Lanthanum Recovery From E-waste. We hope the information we provide is helpful to you. Feel free to contact us if you have any questions or need additional assistance. See you next time, and don't forget to save this page!
Kami berterima kasih atas kunjungan Anda untuk melihat lebih jauh. Lanthanum Recovery From E-waste. Informasikan kepada kami jika Anda memerlukan bantuan tambahan. Tandai situs ini dan pastikan untuk kembali lagi segera!
Featured Posts
-
Statement On Ananda Krishnans Passing
Nov 28, 2024
-
Extensive Flooding Affects 100 Homes In Two Provinces
Nov 28, 2024
-
Paper Straw Market Trends And Predictions
Nov 28, 2024
-
Thanksgiving 2024 Trash Pickup Schedule
Nov 28, 2024
-
Vinicius Junior Ballon D Or Snubbed Again
Nov 28, 2024