Manufacturing's Future: Automated Factories
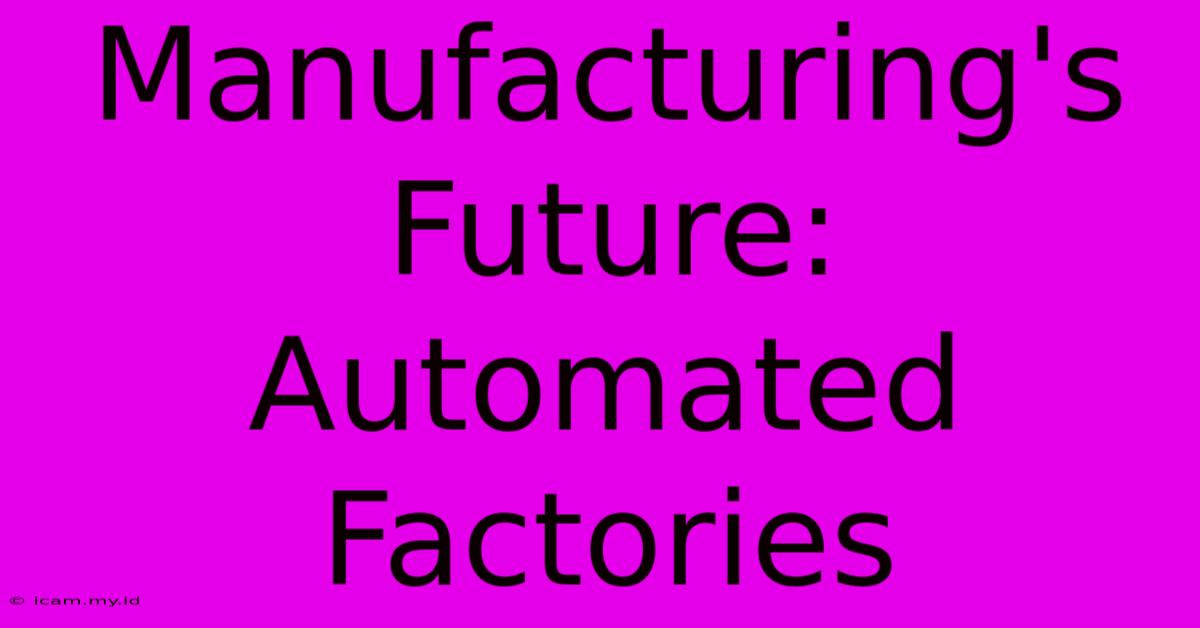
Find more detailed and interesting information on our website. Click the link below to start advanced information: Visit Best Website meltwatermedia.ca. Jangan lewatkan!
Table of Contents
Manufacturing's Future: Automated Factories
The manufacturing landscape is undergoing a dramatic transformation, driven by the relentless march of automation. Gone are the days of solely relying on human labor for repetitive, complex, or dangerous tasks. The future of manufacturing is automated, intelligent, and interconnected, promising increased efficiency, higher quality, and greater flexibility. This shift towards automated factories is not just a trend; it's a fundamental reshaping of how goods are produced, impacting everything from the factory floor to the supply chain and the very nature of manufacturing jobs.
The Driving Forces Behind Automation
Several key factors are accelerating the adoption of automation in manufacturing:
1. The Rise of Robotics and Artificial Intelligence (AI)
Robotics has evolved beyond simple repetitive tasks. Advanced robots now possess sophisticated sensors, computer vision, and machine learning capabilities, allowing them to adapt to changing conditions, handle complex assembly processes, and even collaborate with human workers. AI, meanwhile, plays a crucial role in optimizing production processes, predicting equipment failures, and managing complex logistics. The convergence of robotics and AI is creating truly intelligent factories.
2. The Demand for Increased Efficiency and Productivity
In today's competitive global market, manufacturers are constantly under pressure to reduce costs and increase productivity. Automation offers a powerful solution. Automated systems can work continuously, without breaks or fatigue, leading to significantly higher output and reduced production times. Furthermore, automation minimizes errors associated with human fatigue, resulting in improved product quality and reduced waste.
3. The Need for Greater Flexibility and Adaptability
Consumer demand is becoming increasingly diverse and personalized. Automated factories, with their programmable systems and adaptable robots, are better equipped to handle this variability. They can quickly switch between different product lines, adjust to changing order volumes, and respond to market fluctuations more effectively than traditional manufacturing processes.
4. Addressing Labor Shortages and Rising Labor Costs
Many developed countries are facing labor shortages in the manufacturing sector. Automation offers a solution by taking over repetitive and strenuous tasks, freeing up human workers for more skilled and strategic roles. Moreover, automation can help mitigate rising labor costs by reducing reliance on manual labor.
5. Improving Safety and Working Conditions
Certain manufacturing processes are inherently dangerous, involving hazardous materials or repetitive movements that can lead to injuries. Automation can significantly reduce workplace accidents and improve worker safety by handling these hazardous tasks. This not only protects workers but also enhances overall productivity by minimizing downtime due to injuries.
Key Technologies Shaping Automated Factories
Several key technologies are at the forefront of this automation revolution:
1. Industrial Internet of Things (IIoT)
The IIoT connects machines, sensors, and systems within a factory, enabling real-time data collection and analysis. This data provides valuable insights into production processes, allowing manufacturers to identify inefficiencies, predict maintenance needs, and optimize operations. The IIoT is the nervous system of the automated factory, enabling seamless communication and data flow.
2. Computer-Aided Design (CAD) and Computer-Aided Manufacturing (CAM)
CAD/CAM systems play a critical role in designing and manufacturing products. CAD software allows engineers to create detailed 3D models, while CAM software translates these designs into instructions for automated machines. This integration ensures precision and consistency throughout the production process.
3. Computer Numerical Control (CNC) Machining
CNC machines are automated tools that precisely control the movement of cutting tools or other manufacturing processes. These machines are crucial for producing complex parts with high accuracy and repeatability, crucial for industries like aerospace and automotive manufacturing.
4. Additive Manufacturing (3D Printing)
3D printing is revolutionizing prototyping and manufacturing by enabling the creation of complex parts layer by layer. This technology offers greater design flexibility, reduced material waste, and the potential for on-demand manufacturing. It's particularly valuable for producing customized products or small-batch production runs.
5. Automated Guided Vehicles (AGVs) and Autonomous Mobile Robots (AMRs)
AGVs and AMRs are transforming material handling within factories. These robots autonomously navigate the factory floor, transporting materials and components between different workstations, significantly improving efficiency and reducing the need for manual material handling.
The Human Element in Automated Factories
Despite the significant advancements in automation, human workers remain essential in automated factories. While robots and automated systems handle repetitive tasks, human workers are needed for:
- Programming and Maintenance: Setting up, programming, and maintaining automated systems requires skilled technicians and engineers.
- Quality Control and Inspection: While automated systems can perform some quality checks, human inspection is often still necessary to ensure product quality and identify defects.
- Problem Solving and Decision Making: Automated systems are not always capable of handling unexpected situations or complex problems. Human intervention is often required to troubleshoot issues and make critical decisions.
- Strategic Planning and Management: Humans are responsible for overall factory planning, strategy development, and managing the integration of automated systems.
- Innovation and Development: The ongoing development and improvement of automated systems require human ingenuity and creativity.
Challenges and Considerations for Implementing Automation
While the benefits of automated factories are significant, implementing automation presents several challenges:
- High initial investment costs: The cost of purchasing and installing automated systems can be substantial, requiring significant upfront investment.
- Integration complexity: Integrating different automated systems and ensuring seamless communication can be complex and time-consuming.
- Skill gap: The increasing reliance on automation requires a workforce with specialized skills in robotics, AI, and other related technologies. Addressing the skill gap through training and education is crucial.
- Cybersecurity risks: Automated factories are increasingly vulnerable to cyberattacks, highlighting the need for robust cybersecurity measures.
- Ethical considerations: The widespread adoption of automation raises ethical concerns related to job displacement and the impact on the workforce. Careful planning and retraining initiatives are necessary to mitigate these risks.
The Future of Manufacturing: A Collaborative Approach
The future of manufacturing is not about replacing humans with robots; it's about creating a collaborative environment where humans and robots work together to achieve greater efficiency and productivity. This collaborative approach leverages the strengths of both humans and machines, resulting in a more agile, adaptable, and efficient manufacturing process. The success of automated factories will depend on a holistic approach that considers technological advancements, workforce development, and ethical considerations, ensuring a future where humans and machines work in harmony to create a more productive and sustainable manufacturing industry. This integration requires careful planning, investment in training programs, and a proactive approach to addressing the ethical and societal implications of automation. Only through this thoughtful and balanced approach can we truly harness the transformative potential of automated factories and usher in a new era of manufacturing excellence.
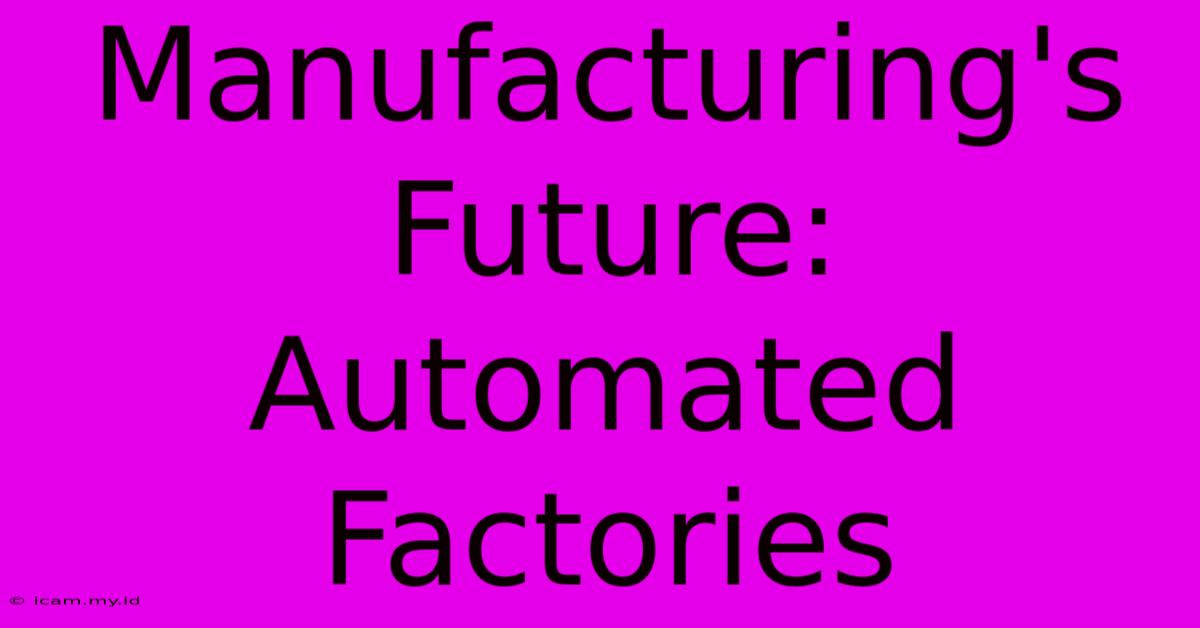
Thank you for visiting our website. Manufacturing's Future: Automated Factories. We hope the information we provide is helpful to you. Feel free to contact us if you have any questions or need additional assistance. See you next time, and don't forget to save this page!
Kami berterima kasih atas kunjungan Anda untuk melihat lebih jauh. Manufacturing's Future: Automated Factories. Informasikan kepada kami jika Anda memerlukan bantuan tambahan. Tandai situs ini dan pastikan untuk kembali lagi segera!
Featured Posts
-
Vinicius Jr Out Real Vs Liverpool
Nov 28, 2024
-
Real Madrid Ancelottis Vinicius Decision
Nov 28, 2024
-
Liverpools Post Salah Era 5 Potential Stars
Nov 28, 2024
-
Malaysian Businessman Ananda Krishnan Dead
Nov 28, 2024
-
Vietnamese Tycoons Holdings Sought By Firm
Nov 28, 2024