Mastering Smart Manufacturing Basics
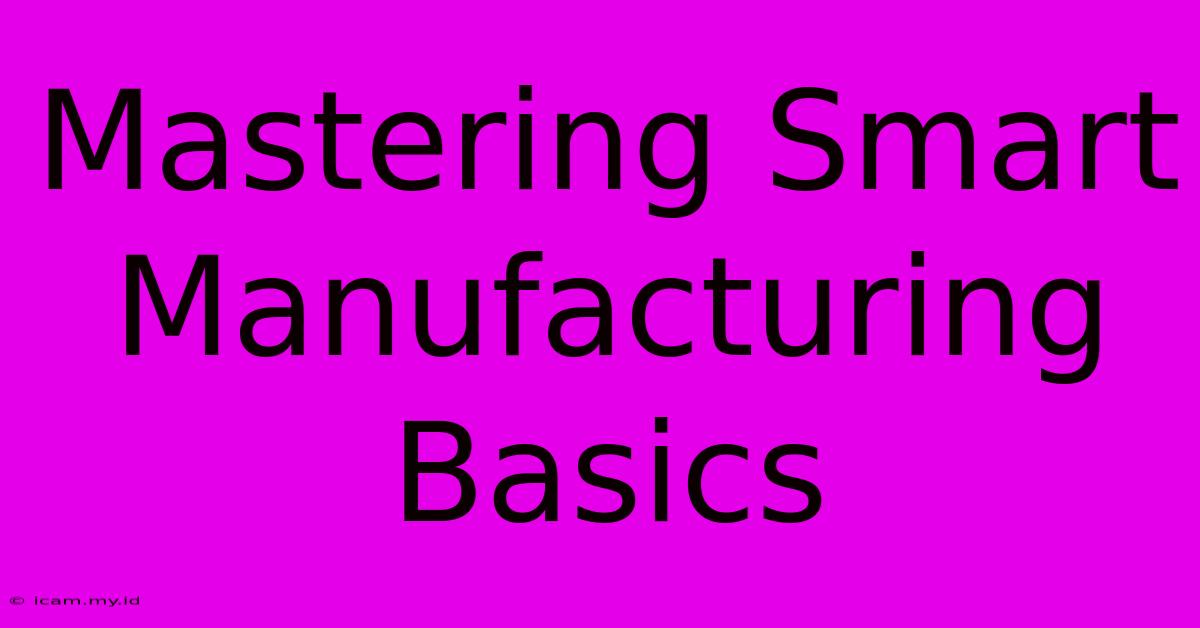
Find more detailed and interesting information on our website. Click the link below to start advanced information: Visit Best Website meltwatermedia.ca. Jangan lewatkan!
Table of Contents
Mastering Smart Manufacturing Basics: A Comprehensive Guide
Smart manufacturing, also known as Industry 4.0, is revolutionizing how goods are produced. It leverages advanced technologies to optimize processes, increase efficiency, and improve product quality. This comprehensive guide delves into the fundamental aspects of smart manufacturing, providing a solid foundation for understanding and implementing this transformative approach.
Understanding the Core Principles of Smart Manufacturing
Smart manufacturing isn't just about adopting new technologies; it's a holistic approach that reimagines the entire manufacturing process. At its core, it's about data-driven decision-making, automation, and connectivity.
-
Data-Driven Decision Making: The heart of smart manufacturing lies in the ability to collect, analyze, and interpret vast amounts of data from various sources throughout the production process. This data provides crucial insights into areas for improvement, predictive maintenance needs, and overall operational efficiency. Sensors embedded in machinery, ERP systems, and supply chain management software all contribute to this data pool. Effective data analysis enables proactive adjustments, minimizing downtime and maximizing output.
-
Automation: Smart manufacturing heavily relies on automation to streamline operations and reduce human error. This includes robotic process automation (RPA), automated guided vehicles (AGVs), and computer numerical control (CNC) machines. Automation not only increases speed and accuracy but also frees up human workers to focus on higher-value tasks like problem-solving and strategic planning.
-
Connectivity: The seamless integration of different systems and devices is crucial for smart manufacturing. This involves the use of Industrial Internet of Things (IIoT) technologies, enabling real-time data exchange between machines, sensors, and software platforms. This interconnectedness allows for better coordination, improved visibility, and faster responses to changing conditions.
Key Technologies Driving Smart Manufacturing
Several key technologies underpin the success of smart manufacturing initiatives. Understanding these technologies is essential for effective implementation:
-
Internet of Things (IoT): The IoT connects physical devices to the internet, enabling data collection and remote monitoring. In manufacturing, IoT sensors on machines provide real-time data on performance, allowing for predictive maintenance and proactive adjustments.
-
Cloud Computing: Cloud-based platforms provide the necessary infrastructure for storing, processing, and analyzing the massive amounts of data generated by smart manufacturing systems. Cloud computing also facilitates collaboration and data sharing among different stakeholders.
-
Big Data Analytics: The ability to analyze vast datasets is critical for extracting valuable insights. Big data analytics techniques help identify patterns, predict future trends, and optimize processes.
-
Artificial Intelligence (AI) and Machine Learning (ML): AI and ML algorithms are increasingly used for tasks such as predictive maintenance, quality control, and process optimization. These technologies can analyze data to identify anomalies, predict potential failures, and make automated adjustments.
-
Robotics: Robots play a vital role in automating repetitive and dangerous tasks. Advanced robotics, including collaborative robots (cobots), are designed to work safely alongside human workers, enhancing productivity and safety.
-
Additive Manufacturing (3D Printing): 3D printing offers the ability to produce customized parts on demand, reducing lead times and inventory costs. This technology is particularly valuable for producing prototypes and low-volume, high-value components.
-
Cybersecurity: With the increased connectivity and reliance on data, robust cybersecurity measures are paramount. Protecting sensitive data and systems from cyber threats is crucial for maintaining operational integrity and preventing disruptions.
Implementing Smart Manufacturing: A Step-by-Step Approach
Implementing smart manufacturing is a complex undertaking that requires careful planning and execution. A phased approach is often recommended:
Phase 1: Assessment and Planning:
- Identify key challenges and opportunities: Analyze current manufacturing processes to pinpoint areas for improvement.
- Define specific goals and metrics: Establish clear objectives for the smart manufacturing initiative, such as reducing downtime, improving quality, or increasing efficiency.
- Choose appropriate technologies: Select technologies that align with specific goals and budget constraints.
- Develop a roadmap and timeline: Create a detailed plan outlining the implementation stages and timelines.
Phase 2: Pilot Projects and Proof of Concept:
- Start with small-scale projects: Implement pilot projects to test and validate chosen technologies before full-scale deployment.
- Gather data and analyze results: Monitor the performance of pilot projects and collect data to assess their effectiveness.
- Refine the approach based on results: Adjust the implementation strategy based on the findings from pilot projects.
Phase 3: Full-Scale Implementation and Integration:
- Deploy chosen technologies across the manufacturing process: Implement chosen technologies on a larger scale.
- Integrate different systems and data sources: Ensure seamless integration between various systems and data sources.
- Train employees on new technologies and processes: Provide adequate training to employees to ensure successful adoption.
Phase 4: Ongoing Monitoring and Optimization:
- Continuously monitor performance and identify areas for improvement: Regularly review performance metrics and make adjustments as needed.
- Leverage data analytics to optimize processes: Use data analytics to identify further opportunities for optimization.
- Stay updated on the latest technologies and trends: Remain aware of advancements in smart manufacturing technologies.
Overcoming Challenges in Smart Manufacturing Adoption
While the benefits of smart manufacturing are significant, several challenges can hinder its successful implementation:
- High initial investment costs: Implementing smart manufacturing technologies can require substantial upfront investment.
- Integration complexities: Integrating different systems and technologies can be challenging.
- Data security concerns: Protecting sensitive data from cyber threats is crucial.
- Lack of skilled workforce: A skilled workforce is essential for successful implementation and operation.
- Resistance to change: Overcoming resistance to change among employees is important for successful adoption.
The Future of Smart Manufacturing
Smart manufacturing is continuously evolving, with new technologies and approaches emerging regularly. Future trends include:
- Increased use of AI and ML: AI and ML will play an increasingly prominent role in optimizing manufacturing processes.
- Enhanced connectivity and data sharing: Greater connectivity and data sharing will improve collaboration and decision-making.
- Focus on sustainability and environmental responsibility: Smart manufacturing will increasingly focus on sustainable practices.
- Rise of digital twins: Digital twins, virtual representations of physical assets, will be used for simulations and optimization.
Mastering the basics of smart manufacturing requires a comprehensive understanding of the core principles, key technologies, and implementation challenges. By adopting a phased approach and addressing potential hurdles proactively, manufacturers can successfully leverage the power of smart manufacturing to enhance efficiency, improve quality, and achieve greater competitiveness in the global marketplace. This ongoing journey of technological integration and process optimization promises to redefine manufacturing as we know it.
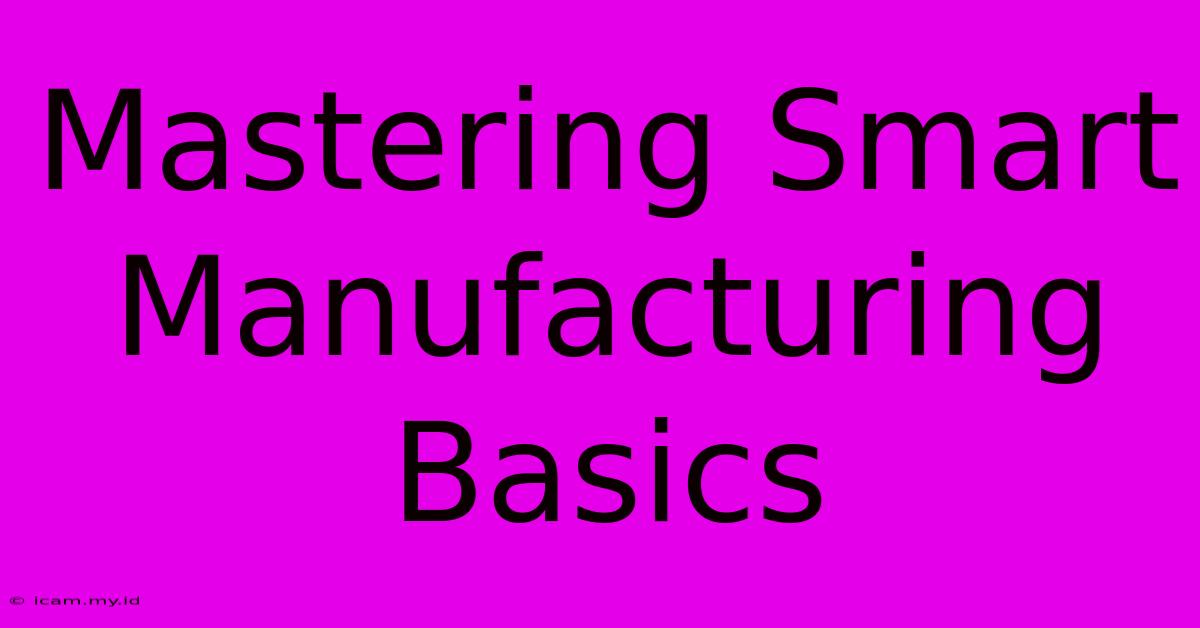
Thank you for visiting our website. Mastering Smart Manufacturing Basics. We hope the information we provide is helpful to you. Feel free to contact us if you have any questions or need additional assistance. See you next time, and don't forget to save this page!
Kami berterima kasih atas kunjungan Anda untuk melihat lebih jauh. Mastering Smart Manufacturing Basics. Informasikan kepada kami jika Anda memerlukan bantuan tambahan. Tandai situs ini dan pastikan untuk kembali lagi segera!
Featured Posts
-
Death During Military Training Atms Statement
Nov 28, 2024
-
Takaful Understanding Medical Premium Increases
Nov 28, 2024
-
Death And Covid Vaccine Autopsy Review
Nov 28, 2024
-
Rare Earth Metals Market Key Trends 2031
Nov 28, 2024
-
Man Citys Woes Liverpools Title Chances
Nov 28, 2024