New Era Of Manufacturing: Automated Factories
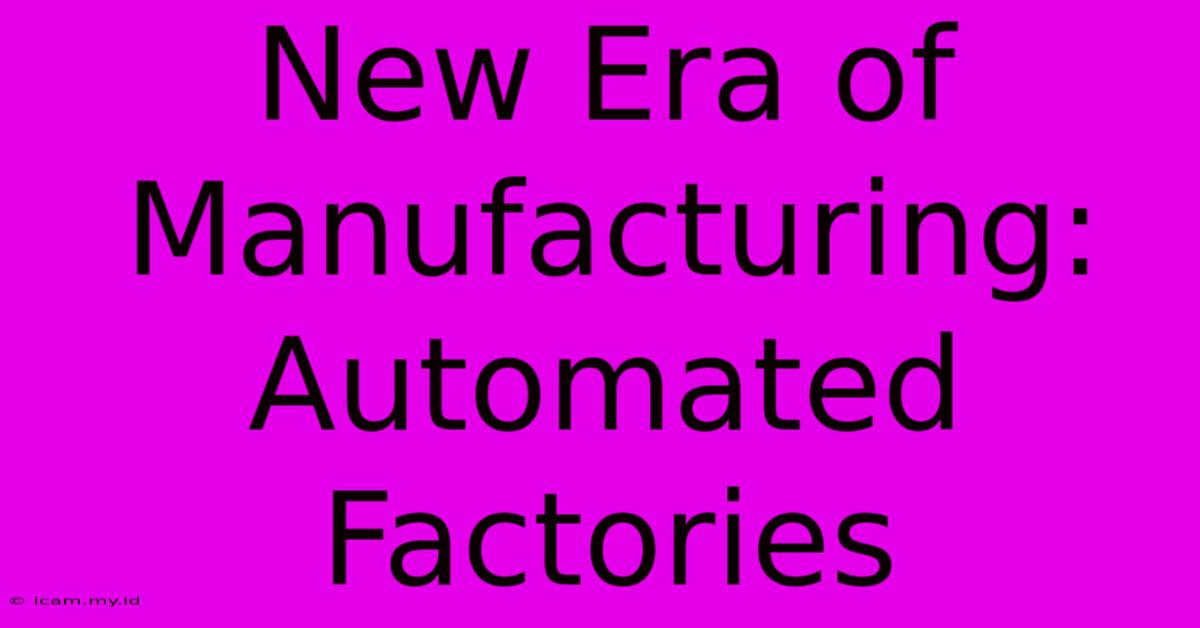
Find more detailed and interesting information on our website. Click the link below to start advanced information: Visit Best Website meltwatermedia.ca. Jangan lewatkan!
Table of Contents
New Era of Manufacturing: Automated Factories
The manufacturing landscape is undergoing a dramatic transformation, driven by the rapid advancements in automation technology. We're entering a new era where automated factories are becoming the norm, not the exception. This shift promises increased efficiency, productivity, and competitiveness, but also presents challenges that need careful consideration. This article delves deep into this exciting new era, exploring the key technologies driving the change, the benefits and drawbacks, and the future implications for manufacturers and the global economy.
The Driving Forces Behind Factory Automation
Several key technological advancements are fueling the rise of automated factories:
1. Robotics and Automation Systems:
Industrial robots are no longer just large, clunky machines performing repetitive tasks. Modern robots are agile, adaptable, and collaborative, working alongside human workers (cobots) to enhance efficiency. These advancements are driven by improvements in:
- Artificial Intelligence (AI): AI enables robots to learn, adapt, and make decisions autonomously, increasing their versatility and problem-solving capabilities. AI-powered vision systems allow robots to identify and manipulate objects with greater precision.
- Machine Learning (ML): ML algorithms allow robots to improve their performance over time based on experience, reducing errors and increasing efficiency.
- Advanced Sensors and Actuators: Sophisticated sensors provide robots with real-time feedback on their environment, allowing them to react to changes and avoid collisions. Advanced actuators enable smoother, more precise movements.
2. Internet of Things (IoT) and Industrial IoT (IIoT):
The IoT connects machines, devices, and sensors within a factory, creating a network that allows for real-time data collection and analysis. This data is crucial for:
- Predictive Maintenance: IoT sensors can detect anomalies and predict equipment failures before they occur, minimizing downtime and reducing maintenance costs.
- Optimized Production: Real-time data on production processes allows manufacturers to identify bottlenecks and optimize workflows, maximizing output.
- Improved Quality Control: Data from sensors and machines can be used to monitor product quality and identify defects early in the production process.
3. Big Data Analytics and Cloud Computing:
The vast amounts of data generated by automated factories require powerful analytics tools to extract meaningful insights. Cloud computing provides the infrastructure needed to store, process, and analyze this data effectively. This enables:
- Data-Driven Decision Making: Manufacturers can use data analytics to improve production processes, optimize resource allocation, and make informed business decisions.
- Supply Chain Optimization: Data analytics can be used to optimize the entire supply chain, from procurement to delivery.
- Improved Customer Service: Data on customer preferences and product performance can be used to improve product design and customer service.
4. 3D Printing (Additive Manufacturing):
3D printing is revolutionizing manufacturing by enabling the creation of highly customized products on demand. This technology is particularly beneficial for:
- Rapid Prototyping: 3D printing allows manufacturers to quickly create prototypes and test new designs, accelerating the product development process.
- Customized Production: It enables the production of highly customized products, tailored to individual customer needs.
- On-Demand Manufacturing: Products can be printed on demand, reducing inventory costs and lead times.
Benefits of Automated Factories
The transition to automated factories offers numerous benefits:
- Increased Productivity and Efficiency: Automation streamlines processes, reduces human error, and allows for 24/7 operation, significantly increasing productivity.
- Improved Product Quality and Consistency: Automated systems consistently produce high-quality products with minimal variations, enhancing brand reputation.
- Reduced Labor Costs: While initial investment can be high, automation can reduce long-term labor costs and improve overall efficiency.
- Enhanced Safety: Automation eliminates many hazardous tasks, improving workplace safety for human workers.
- Greater Flexibility and Adaptability: Automated systems can be easily reprogrammed to produce different products, adapting quickly to changing market demands.
- Data-Driven Insights: Real-time data collection allows manufacturers to identify areas for improvement, leading to continuous optimization.
- Reduced Waste and Improved Sustainability: Automation minimizes material waste and optimizes resource utilization, contributing to a more sustainable manufacturing process.
Challenges of Implementing Automated Factories
Despite the many advantages, the transition to automated factories presents several challenges:
- High Initial Investment Costs: Implementing automation requires significant upfront investment in new equipment, software, and training.
- Integration Complexity: Integrating different automation systems and technologies can be complex and time-consuming.
- Cybersecurity Risks: Connected systems are vulnerable to cyberattacks, requiring robust cybersecurity measures.
- Job Displacement Concerns: Automation may lead to job displacement in some sectors, requiring retraining and workforce adaptation.
- Skills Gap: The increasing complexity of automated systems requires a workforce with specialized skills in areas like robotics, AI, and data analytics.
- Maintenance and Repair Costs: Automated systems require regular maintenance and repairs, which can be costly.
- Return on Investment (ROI): Achieving a positive ROI requires careful planning, execution, and ongoing monitoring.
The Future of Automated Factories
The future of manufacturing is undeniably automated. We can expect to see:
- Increased Collaboration Between Humans and Robots: Cobots will become increasingly common, working alongside human workers to enhance productivity and efficiency.
- Greater Use of AI and Machine Learning: AI and ML will play an increasingly important role in optimizing production processes, predicting failures, and improving decision-making.
- More Connected and Intelligent Factories: The use of IoT and IIoT will continue to grow, creating more connected and intelligent factories.
- Sustainable Manufacturing Practices: Automation will contribute to more sustainable manufacturing practices by reducing waste, optimizing resource utilization, and minimizing environmental impact.
- Hyper-Personalization of Products: Automated systems will enable the production of highly personalized products, tailored to individual customer needs.
Conclusion
The new era of manufacturing, characterized by automated factories, is transforming the global economy. While the transition presents challenges, the benefits – increased productivity, improved quality, and enhanced sustainability – are significant. By embracing automation strategically and addressing the associated challenges, manufacturers can position themselves for success in this rapidly evolving landscape. The future of manufacturing lies in the intelligent integration of human ingenuity and advanced automation technologies, creating a collaborative ecosystem that drives innovation and economic growth.
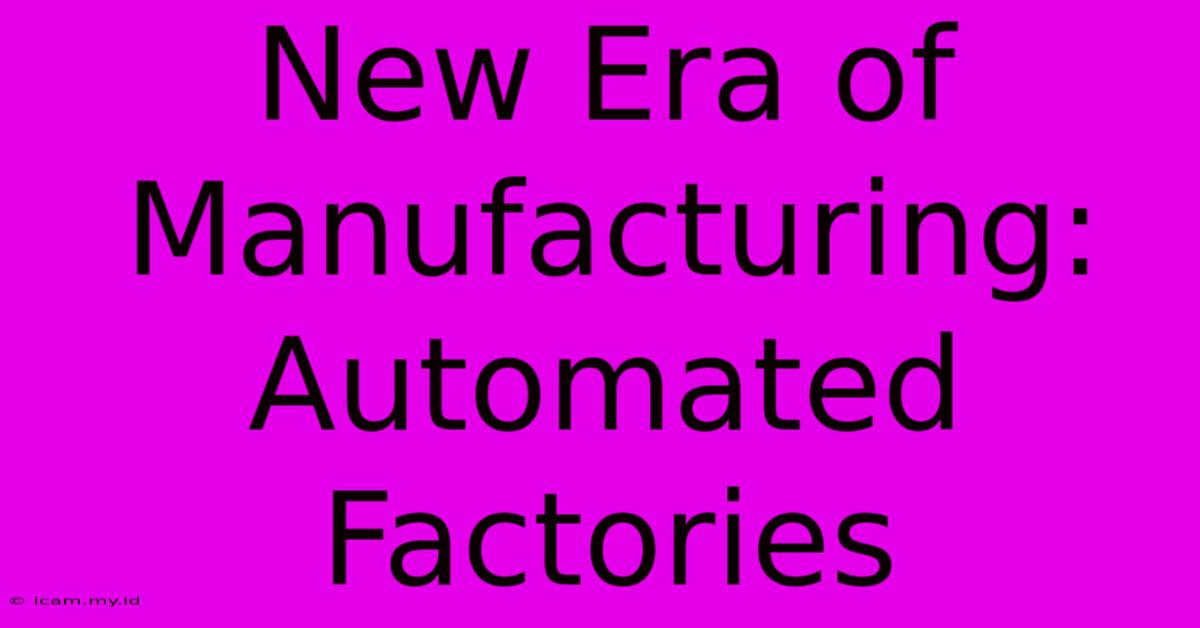
Thank you for visiting our website. New Era Of Manufacturing: Automated Factories. We hope the information we provide is helpful to you. Feel free to contact us if you have any questions or need additional assistance. See you next time, and don't forget to save this page!
Kami berterima kasih atas kunjungan Anda untuk melihat lebih jauh. New Era Of Manufacturing: Automated Factories. Informasikan kepada kami jika Anda memerlukan bantuan tambahan. Tandai situs ini dan pastikan untuk kembali lagi segera!
Featured Posts
-
Smart Factories Economic Analysis
Nov 28, 2024
-
Golden Man Award Ex Real Madrid Star Wins
Nov 28, 2024
-
Epl Round 12 Salah Leads Liverpool
Nov 28, 2024
-
New Law Australia Bans Under 16s From Social Media
Nov 28, 2024
-
The Rise Of Automated Factories In Manufacturing
Nov 28, 2024