Revolutionizing Manufacturing: Automated Factories
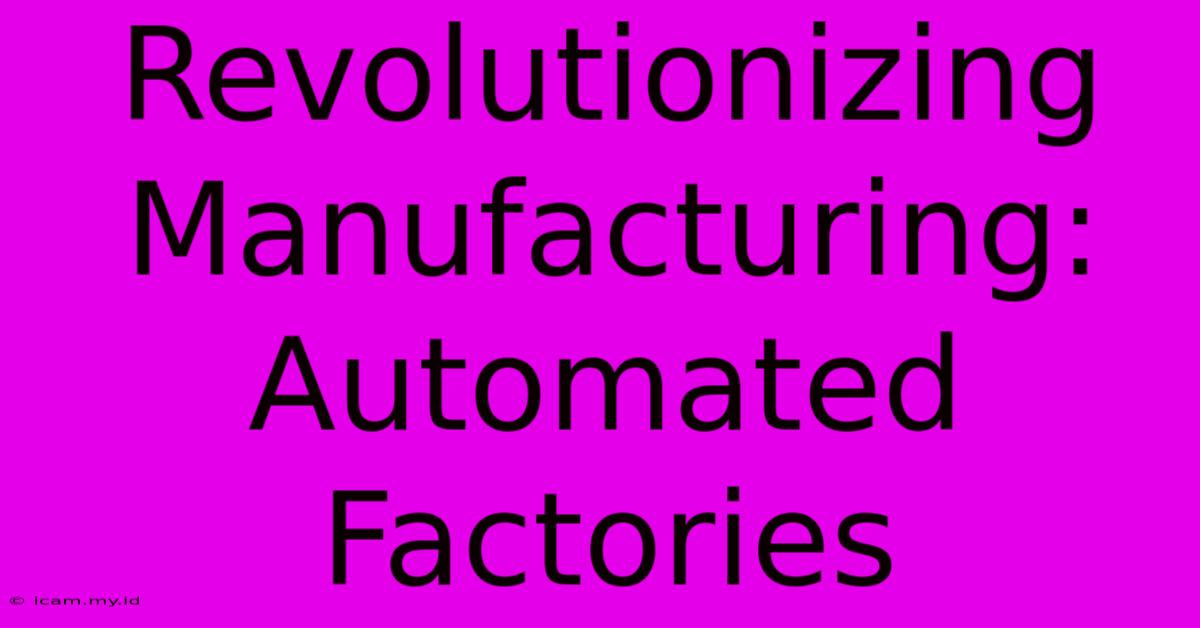
Find more detailed and interesting information on our website. Click the link below to start advanced information: Visit Best Website meltwatermedia.ca. Jangan lewatkan!
Table of Contents
Revolutionizing Manufacturing: Automated Factories
The manufacturing landscape is undergoing a dramatic transformation, driven by the relentless march of automation. Automated factories, once a futuristic fantasy, are rapidly becoming the norm, promising increased efficiency, reduced costs, and a leap forward in product quality. This revolution isn't just about replacing human workers; it's about augmenting human capabilities, creating smarter, more responsive, and ultimately more competitive manufacturing processes. This article delves deep into the heart of this automation revolution, exploring its driving forces, key technologies, benefits, challenges, and the future it promises.
The Driving Forces Behind Factory Automation
Several key factors are propelling the widespread adoption of automated factories:
1. The Demand for Increased Efficiency and Productivity:
In today's fast-paced global economy, manufacturers face intense pressure to deliver products faster, cheaper, and with higher quality. Automation offers a powerful solution. Robots and automated systems can work tirelessly around the clock, significantly boosting production rates and reducing lead times. This increased efficiency translates directly to higher profits and a stronger competitive edge.
2. The Rise of E-commerce and Mass Customization:
The explosive growth of e-commerce has created a surge in demand for personalized products. Automated factories are uniquely positioned to meet this demand. Flexible automation systems can adapt to produce customized products on a large scale, ensuring customers receive exactly what they want, when they want it. This agility is crucial for success in the modern marketplace.
3. The Need for Enhanced Product Quality and Consistency:
Automated systems are far less prone to human error than manual processes. This consistency leads to significantly improved product quality and reduced defects. By minimizing variability, automated factories ensure that each product meets the highest standards, leading to increased customer satisfaction and brand loyalty.
4. Labor Shortages and Rising Labor Costs:
Many developed nations face a growing shortage of skilled manufacturing workers. Automation offers a viable solution to this problem by filling labor gaps and reducing reliance on human workers for repetitive or dangerous tasks. While some jobs may be displaced, automation also creates new opportunities in areas like system maintenance, programming, and data analysis.
5. Technological Advancements:
Rapid advancements in robotics, artificial intelligence (AI), machine learning (ML), and the Internet of Things (IoT) are driving down the cost and increasing the capabilities of automation technologies. These advancements make automation more accessible to a wider range of manufacturers, regardless of size or industry.
Key Technologies Powering Automated Factories
Several key technologies are at the forefront of this manufacturing revolution:
1. Industrial Robots:
Robots are the workhorses of automated factories, performing a wide range of tasks, from welding and painting to assembly and packaging. Collaborative robots (cobots) are especially noteworthy, working safely alongside human workers to enhance productivity and efficiency. These robots are designed with safety features to prevent accidents and injuries.
2. Artificial Intelligence (AI) and Machine Learning (ML):
AI and ML are revolutionizing manufacturing by enabling predictive maintenance, quality control, and process optimization. AI-powered systems can analyze vast amounts of data from sensors and machines to identify potential problems before they occur, minimizing downtime and maximizing efficiency. ML algorithms continuously learn and improve, making automation systems increasingly sophisticated over time.
3. Computer Numerical Control (CNC) Machines:
CNC machines are computer-controlled tools that automate the manufacturing of parts with high precision and accuracy. They are essential for a wide range of applications, from machining metal parts to creating complex plastic components. These machines significantly reduce lead times and improve overall quality.
4. Computer-Aided Design (CAD) and Computer-Aided Manufacturing (CAM):
CAD/CAM software integrates the design and manufacturing processes, allowing for seamless transitions between digital design and physical production. This integrated approach reduces errors and speeds up the entire manufacturing cycle.
5. The Internet of Things (IoT):
The IoT connects machines, sensors, and systems within the factory, enabling real-time data collection and analysis. This connectivity enhances visibility and control over the manufacturing process, allowing for immediate adjustments and optimizations. IoT facilitates predictive maintenance and efficient resource management.
Benefits of Automated Factories
The benefits of adopting automated factories are numerous and far-reaching:
1. Increased Productivity and Efficiency:
Automated systems operate continuously, boosting output significantly and reducing manufacturing lead times. This increased efficiency translates to higher profits and a greater ability to meet market demands.
2. Improved Product Quality and Consistency:
Automation minimizes human error, leading to significantly improved product quality and fewer defects. This consistency builds brand reputation and enhances customer satisfaction.
3. Reduced Labor Costs:
While automation requires an initial investment, it can lead to significant long-term savings on labor costs. Automated systems can operate around the clock, reducing the need for large human workforces.
4. Enhanced Safety:
Automation can eliminate or significantly reduce the risk of workplace accidents by handling hazardous tasks. This leads to a safer and healthier work environment for human employees.
5. Greater Flexibility and Adaptability:
Automated systems can be easily reprogrammed to adapt to changes in product design or demand. This flexibility allows manufacturers to respond quickly to market trends and customer needs.
6. Improved Data Collection and Analysis:
Automated factories generate vast amounts of data, providing valuable insights into the manufacturing process. This data can be used to identify areas for improvement and optimize efficiency.
Challenges of Implementing Automated Factories
While the benefits of automated factories are substantial, several challenges need to be addressed:
1. High Initial Investment Costs:
Implementing automated systems requires a significant upfront investment in equipment, software, and training. This can be a barrier to entry for smaller manufacturers.
2. Integration Complexity:
Integrating different automated systems and legacy equipment can be a complex and challenging undertaking. It requires careful planning and expertise to ensure seamless operation.
3. Cybersecurity Risks:
Automated factories are increasingly vulnerable to cyberattacks. Robust cybersecurity measures are critical to protect sensitive data and prevent disruptions to operations.
4. Job Displacement Concerns:
Automation can lead to job displacement for certain workers. Retraining and upskilling initiatives are crucial to mitigate this impact and prepare the workforce for new roles.
5. Maintenance and Repair:
Automated systems require regular maintenance and repair, which can be costly and time-consuming. Proper maintenance schedules and skilled technicians are essential for minimizing downtime.
The Future of Automated Factories
The future of manufacturing is undeniably intertwined with automation. We can expect to see even more sophisticated and integrated systems, fueled by advancements in AI, ML, and IoT. The factory of the future will be a highly connected, data-driven environment where machines and humans work collaboratively to achieve unprecedented levels of efficiency, quality, and flexibility. The focus will shift from mass production to mass customization, with automated systems capable of adapting to individual customer needs. Sustainability will also play a larger role, with automated systems optimized for energy efficiency and waste reduction.
The revolution in manufacturing driven by automated factories is transforming industries and shaping the future of work. While challenges remain, the potential benefits are too significant to ignore. By embracing automation and addressing the associated challenges proactively, manufacturers can position themselves for success in an increasingly competitive global marketplace. The journey toward fully automated factories is an ongoing process, but the destination—a future of higher efficiency, improved quality, and greater flexibility—is worth the effort.
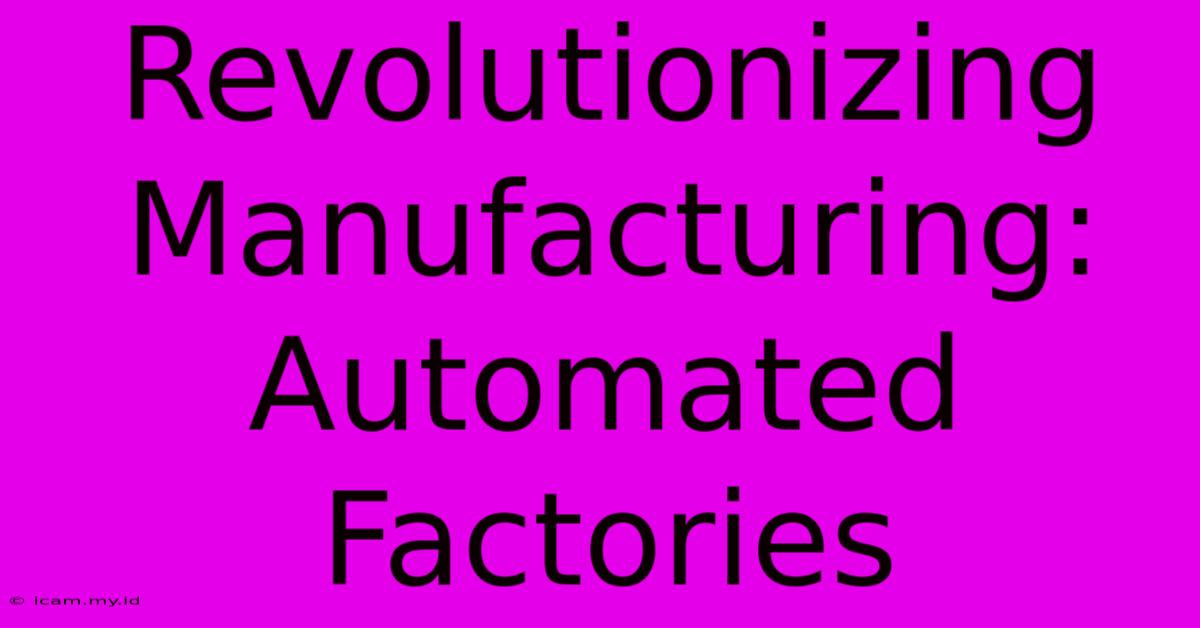
Thank you for visiting our website. Revolutionizing Manufacturing: Automated Factories. We hope the information we provide is helpful to you. Feel free to contact us if you have any questions or need additional assistance. See you next time, and don't forget to save this page!
Kami berterima kasih atas kunjungan Anda untuk melihat lebih jauh. Revolutionizing Manufacturing: Automated Factories. Informasikan kepada kami jika Anda memerlukan bantuan tambahan. Tandai situs ini dan pastikan untuk kembali lagi segera!
Featured Posts
-
Northpoint City New Tous Les Jours Location
Nov 28, 2024
-
Southampton Loss Liverpool Leads By Eight
Nov 28, 2024
-
Thai Opposition For Selangors New Coach
Nov 28, 2024
-
Ui Tm Cadet Fatality Tudm Inquiry
Nov 28, 2024
-
Kinoshi Appointed Selangor Fc Head Coach
Nov 28, 2024