Smart Factories: Automated Manufacturing's Rise
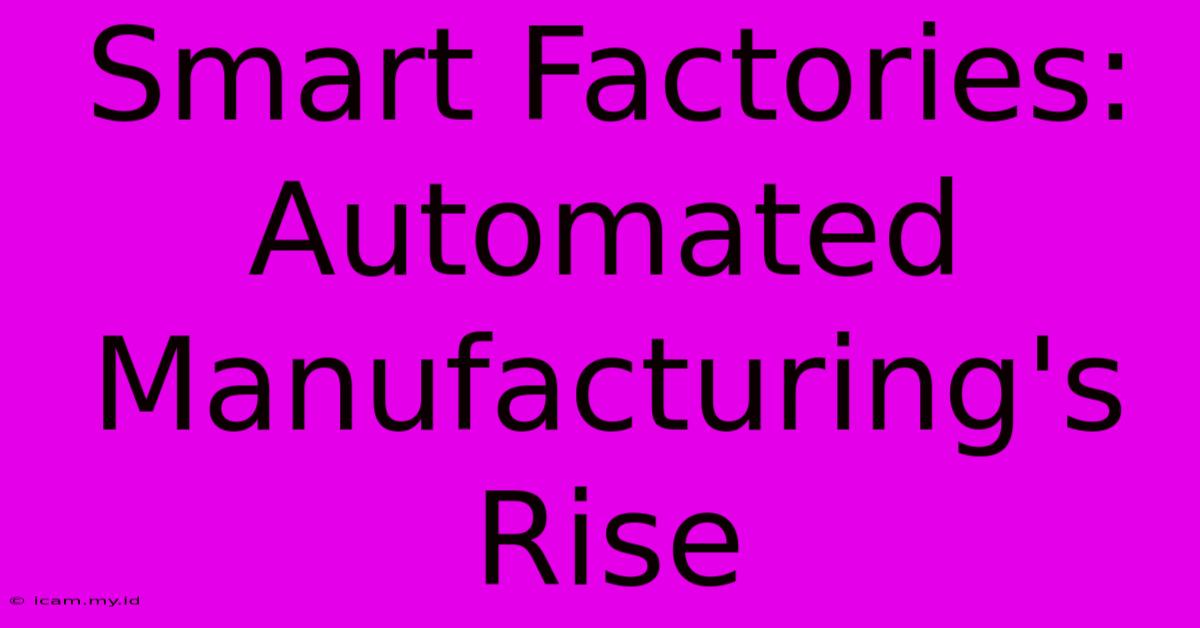
Find more detailed and interesting information on our website. Click the link below to start advanced information: Visit Best Website meltwatermedia.ca. Jangan lewatkan!
Table of Contents
Smart Factories: Automated Manufacturing's Rise
The manufacturing landscape is undergoing a dramatic transformation, driven by the rapid advancement of technology and the increasing demand for efficiency and agility. At the heart of this revolution lies the smart factory, a digitally connected ecosystem that leverages automation, data analytics, and artificial intelligence (AI) to optimize every aspect of the manufacturing process. This article delves into the rise of smart factories, exploring their key components, benefits, challenges, and the future of automated manufacturing.
Understanding the Smart Factory Ecosystem
A smart factory isn't simply about installing robots; it's a holistic approach to manufacturing that integrates various technologies to create a seamless and intelligent operation. Key components include:
1. Internet of Things (IoT) Connectivity:
The foundation of a smart factory is its extensive network of connected devices. IoT sensors embedded in machines, equipment, and products collect real-time data on everything from temperature and pressure to production speed and energy consumption. This data provides invaluable insights into the manufacturing process, enabling proactive maintenance and optimization.
2. Automation and Robotics:
Industrial robots and automated systems perform repetitive tasks with precision and speed, significantly increasing productivity and reducing human error. This includes tasks such as welding, painting, assembly, and material handling. Advanced robotics, such as collaborative robots (cobots), are increasingly being deployed to work alongside human workers, enhancing efficiency and safety.
3. Data Analytics and AI:
The vast amounts of data generated by connected devices are analyzed using advanced analytics and AI algorithms. This allows manufacturers to identify trends, predict potential problems, and optimize production processes in real-time. Predictive maintenance, for example, uses AI to anticipate equipment failures and schedule maintenance before downtime occurs.
4. Cloud Computing:
Cloud computing provides the infrastructure for storing and processing the massive amounts of data generated by a smart factory. This enables access to data from anywhere, facilitating collaboration and decision-making across the entire supply chain.
5. Cyber-Physical Systems (CPS):
CPS integrates the physical and digital worlds, enabling real-time monitoring and control of manufacturing processes. This allows for dynamic adjustments to production based on changing conditions and demand.
The Benefits of Smart Factories
The transition to smart manufacturing offers a multitude of benefits, including:
1. Increased Productivity and Efficiency:
Automation and optimized processes significantly enhance productivity. Robots work tirelessly, reducing downtime and increasing output. Data analytics identifies bottlenecks and areas for improvement, further streamlining operations.
2. Improved Product Quality:
Automated systems perform tasks with greater precision than humans, resulting in higher product quality and consistency. Real-time monitoring and data analysis help identify and address quality issues proactively.
3. Reduced Costs:
Smart factories reduce costs in several ways: increased productivity, reduced waste, lower energy consumption, and minimized downtime. Predictive maintenance avoids costly unplanned outages.
4. Enhanced Flexibility and Agility:
Smart factories can quickly adapt to changing demands and market conditions. Automated systems can be reprogrammed easily to produce different products, enabling greater flexibility.
5. Improved Safety:
Automation reduces the risk of workplace accidents by automating hazardous tasks. Real-time monitoring systems can also identify potential safety hazards and alert workers.
6. Better Data-Driven Decision Making:
The abundance of data generated by a smart factory provides the foundation for informed decision-making. Data-driven insights enable manufacturers to optimize their operations, improve efficiency, and increase profitability.
Challenges in Implementing Smart Factories
Despite the numerous advantages, implementing a smart factory presents several challenges:
1. High Initial Investment:
The cost of implementing smart factory technologies can be substantial. Investing in new equipment, software, and integration services requires significant upfront capital.
2. Integration Complexity:
Integrating various technologies and systems can be complex and challenging. Ensuring seamless communication and data exchange between different components is crucial.
3. Data Security Concerns:
The large amounts of data generated by a smart factory make it a potential target for cyberattacks. Robust cybersecurity measures are essential to protect sensitive data.
4. Skill Gaps:
Operating and maintaining smart factory technologies requires specialized skills. The workforce needs to be trained to manage and utilize these advanced technologies effectively.
5. Legacy Systems:
Integrating new smart factory technologies with existing legacy systems can be difficult and time-consuming. Upgrading or replacing outdated systems may be necessary.
The Future of Automated Manufacturing
The future of manufacturing is undeniably smart. We can expect to see continued advancements in:
- Artificial Intelligence (AI) and Machine Learning (ML): AI and ML will play an increasingly important role in optimizing manufacturing processes, predicting equipment failures, and improving product quality.
- Digital Twins: Digital twins, virtual representations of physical assets, will be used to simulate and optimize manufacturing processes before they are implemented in the real world.
- Additive Manufacturing (3D Printing): 3D printing will become increasingly prevalent in manufacturing, enabling the creation of customized products and reducing waste.
- Robotics and Automation: More advanced robots and automated systems will be developed, leading to greater efficiency and flexibility in manufacturing.
- Sustainable Manufacturing: Smart factories will play a crucial role in creating more sustainable manufacturing processes, reducing waste, and minimizing environmental impact.
Conclusion
The rise of smart factories represents a paradigm shift in manufacturing. By embracing automation, data analytics, and AI, manufacturers can significantly increase productivity, improve product quality, reduce costs, and enhance flexibility. While challenges exist, the benefits of smart manufacturing are undeniable, and its adoption will continue to accelerate in the years to come. The factories of the future will be intelligent, connected, and sustainable, driving innovation and economic growth across the globe. Understanding and adapting to this transformation is crucial for manufacturers seeking to remain competitive in today's dynamic market.
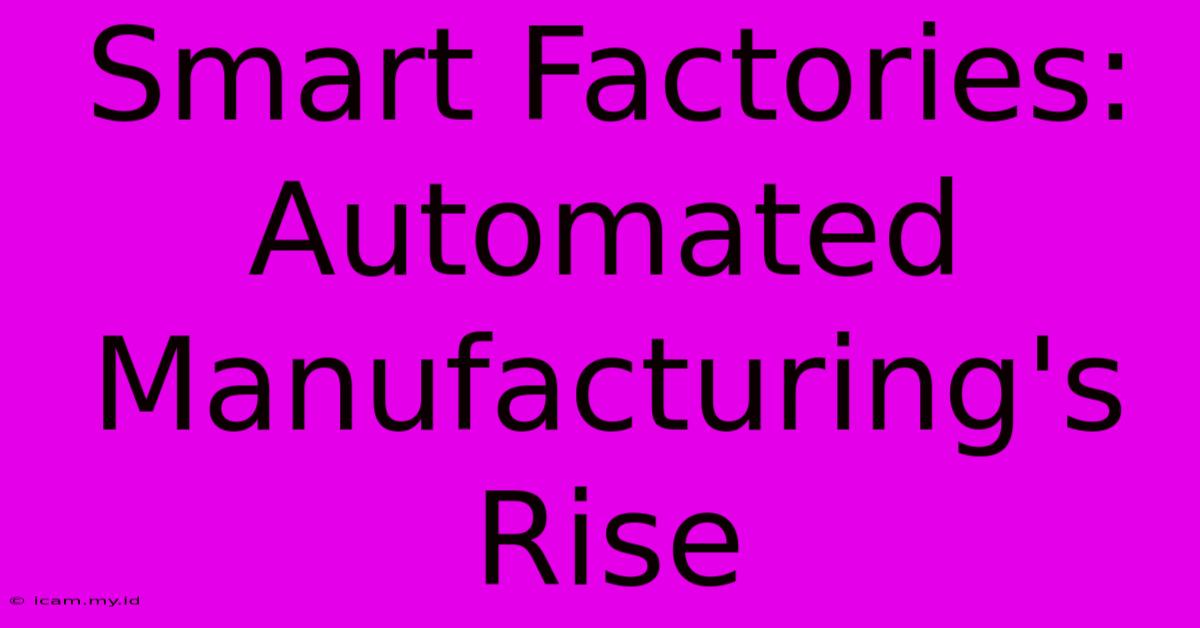
Thank you for visiting our website. Smart Factories: Automated Manufacturing's Rise. We hope the information we provide is helpful to you. Feel free to contact us if you have any questions or need additional assistance. See you next time, and don't forget to save this page!
Kami berterima kasih atas kunjungan Anda untuk melihat lebih jauh. Smart Factories: Automated Manufacturing's Rise. Informasikan kepada kami jika Anda memerlukan bantuan tambahan. Tandai situs ini dan pastikan untuk kembali lagi segera!
Featured Posts
-
Malaysian Businessman Ananda Krishnan Passes
Nov 28, 2024
-
Acl 2 Can Selangor Reach The Round Of 16
Nov 28, 2024
-
Ananda Krishnan Obituary Of A Media Icon 86
Nov 28, 2024
-
Selangor Football Kinoshis First Match
Nov 28, 2024
-
Australias Under 16 Social Media Ban Approved
Nov 28, 2024