Smart Factories: Economic Impact
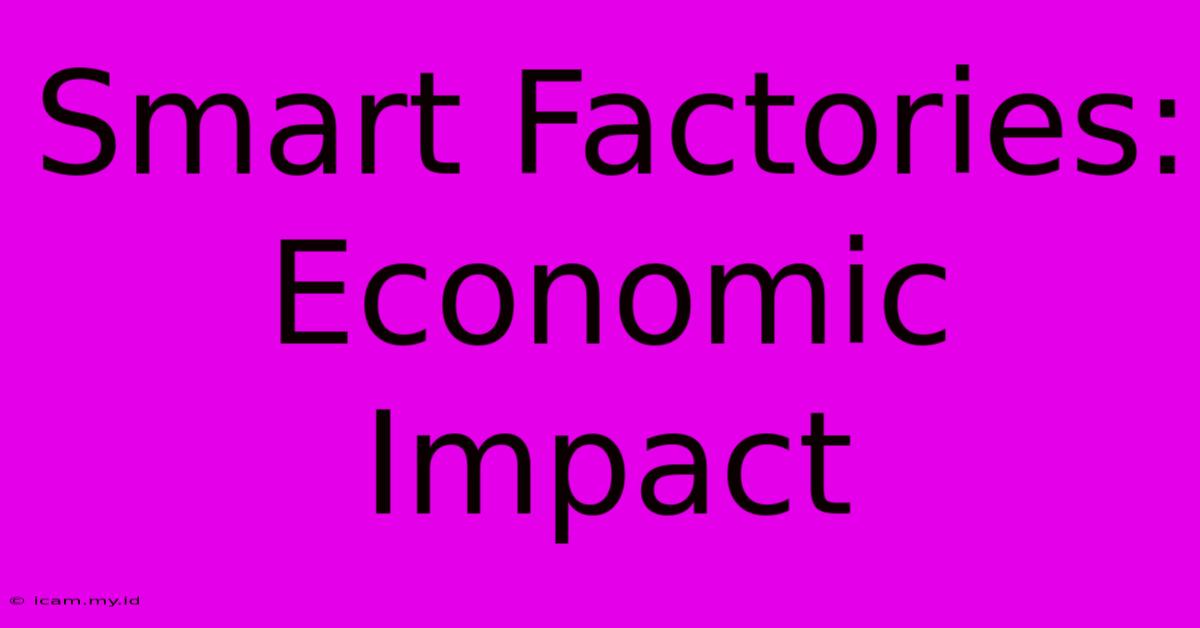
Find more detailed and interesting information on our website. Click the link below to start advanced information: Visit Best Website meltwatermedia.ca. Jangan lewatkan!
Table of Contents
Smart Factories: Economic Impact – A Deep Dive into Industry 4.0's Financial Repercussions
The rise of smart factories, powered by the convergence of technologies under Industry 4.0, is dramatically reshaping the manufacturing landscape. This isn't just about technological advancement; it's about a fundamental shift in economic impact, affecting everything from productivity and efficiency to job creation and global competitiveness. Understanding this economic impact is crucial for businesses, policymakers, and anyone interested in the future of manufacturing.
This article delves into the multifaceted economic effects of smart factories, examining both the opportunities and challenges they present.
The Positive Economic Impacts of Smart Factories
The transition to smart factories promises significant economic benefits across various sectors. Let's explore some key areas:
1. Increased Productivity and Efficiency:
This is arguably the most significant economic impact. Smart factories leverage automation, data analytics, and machine learning to optimize production processes. This leads to:
- Reduced downtime: Predictive maintenance, enabled by sensors and data analysis, minimizes unexpected equipment failures, significantly reducing costly downtime.
- Improved resource utilization: Real-time monitoring and optimization ensure resources like energy and materials are used efficiently, minimizing waste and lowering operational costs.
- Enhanced quality control: Automated quality checks and data-driven insights help identify and rectify defects early in the process, reducing waste and improving product quality.
- Faster production cycles: Automation and streamlined processes shorten lead times, enabling faster responses to market demands and quicker product launches.
2. Cost Reduction and Improved Profitability:
The increased efficiency translates directly into substantial cost savings:
- Lower labor costs: While automation may initially involve investment, it ultimately reduces reliance on manual labor in repetitive tasks, leading to long-term cost savings. This, however, necessitates retraining and upskilling of the workforce for higher-value roles.
- Reduced material waste: Optimized resource utilization minimizes material waste, leading to significant savings on raw materials and disposal costs.
- Improved energy efficiency: Smart factories leverage data analytics to identify and address energy inefficiencies, reducing energy consumption and lowering utility bills.
- Increased output: Higher productivity and efficiency lead to a greater volume of output, boosting revenue and profitability.
3. Enhanced Product Quality and Innovation:
Smart factories foster a culture of continuous improvement and innovation:
- Data-driven insights: Real-time data analysis provides valuable insights into product performance and customer preferences, enabling companies to develop better products and improve existing ones.
- Faster product development cycles: Automation and streamlined processes accelerate the product development lifecycle, enabling quicker responses to market trends and increased competitiveness.
- Customization and personalization: Smart factories facilitate mass customization, allowing companies to produce tailored products to meet specific customer needs. This can command higher prices and enhance customer loyalty.
4. Job Creation and Economic Growth:
While concerns exist about job displacement due to automation, smart factories also create new jobs:
- High-skilled jobs: The transition requires skilled workers in areas such as data science, software engineering, robotics, and cybersecurity.
- New industries: The development and implementation of smart factory technologies create opportunities in related industries, driving overall economic growth.
- Increased competitiveness: Companies that embrace smart factory technologies become more competitive, attracting investment and creating more job opportunities.
The Challenges and Economic Risks of Smart Factory Implementation
Despite the numerous benefits, the transition to smart factories also presents significant challenges:
1. High Initial Investment Costs:
Implementing smart factory technologies requires substantial upfront investment in new equipment, software, and infrastructure. This can be a significant barrier for smaller companies with limited resources.
2. Integration Complexity:
Integrating various technologies and systems within a smart factory can be complex and time-consuming, requiring specialized expertise and careful planning. Issues of interoperability between different systems can significantly hinder progress.
3. Cybersecurity Risks:
The interconnected nature of smart factories increases vulnerability to cyberattacks. Protecting sensitive data and ensuring the security of critical infrastructure is crucial to prevent costly disruptions and data breaches.
4. Workforce Reskilling and Training:
The shift towards automation necessitates retraining and upskilling the existing workforce to adapt to new roles and responsibilities. This requires significant investment in training programs and educational initiatives.
5. Data Management and Analytics:
The vast amounts of data generated by smart factories require robust data management and analytics capabilities. Companies need to invest in the necessary infrastructure and expertise to effectively collect, process, and interpret this data.
6. Lack of Skilled Labor:
A shortage of skilled workers in areas such as data science, robotics, and cybersecurity can hinder the successful implementation of smart factory technologies.
7. Regulatory and Policy Challenges:
The rapid advancement of smart factory technologies requires appropriate regulatory frameworks and policies to address potential risks and ensure responsible innovation. Standardization and interoperability are also crucial aspects to consider.
Conclusion: Navigating the Economic Landscape of Smart Factories
The economic impact of smart factories is transformative, presenting both significant opportunities and considerable challenges. While the initial investment costs and integration complexities can be daunting, the long-term benefits in terms of increased productivity, efficiency, and innovation are undeniable.
To fully realize the economic potential of smart factories, governments and businesses must collaborate to address the associated challenges. This includes investing in education and training programs to develop a skilled workforce, promoting cybersecurity best practices, and establishing supportive regulatory frameworks. By proactively addressing these challenges, we can unlock the full economic benefits of this technological revolution and usher in a new era of manufacturing prosperity. The future of manufacturing is smart, and its economic impact will continue to evolve and deepen in the years to come. Adapting and embracing this change will be key to remaining competitive in the global marketplace.
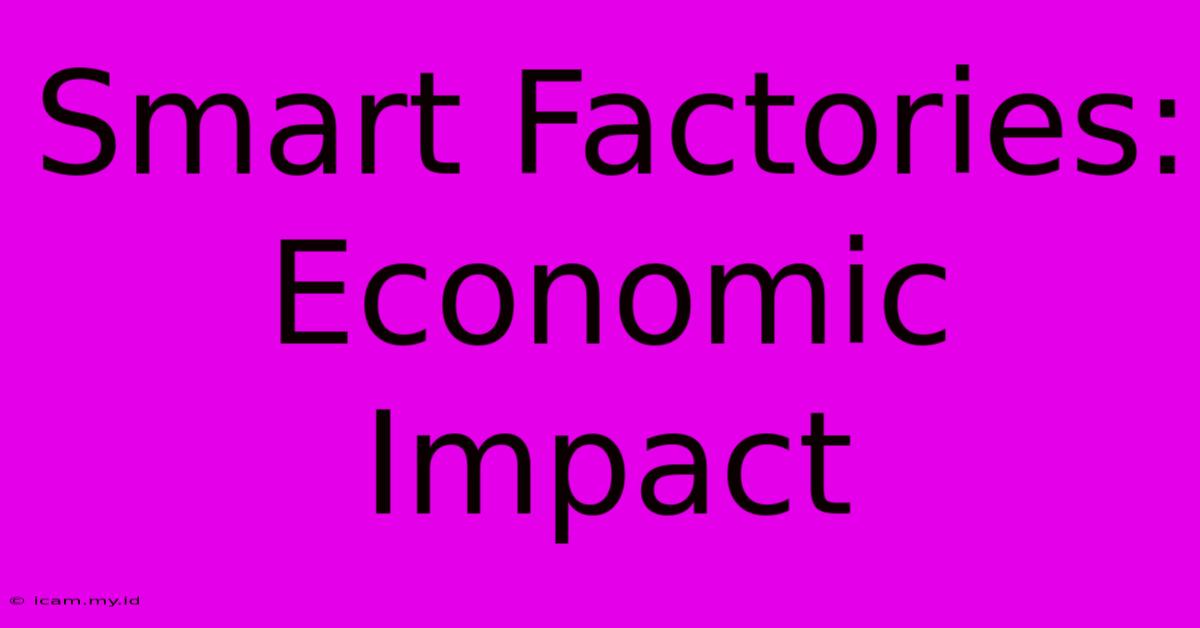
Thank you for visiting our website. Smart Factories: Economic Impact. We hope the information we provide is helpful to you. Feel free to contact us if you have any questions or need additional assistance. See you next time, and don't forget to save this page!
Kami berterima kasih atas kunjungan Anda untuk melihat lebih jauh. Smart Factories: Economic Impact. Informasikan kepada kami jika Anda memerlukan bantuan tambahan. Tandai situs ini dan pastikan untuk kembali lagi segera!
Featured Posts
-
Australias Social Media Ban Under 16
Nov 28, 2024
-
Delicious Pastries Tous Les Jours Bakery
Nov 28, 2024
-
Is Ancelotti Neglecting Vinicius Jr
Nov 28, 2024
-
Business Icon Ananda Krishnan Passes Away At 86
Nov 28, 2024
-
Rising Mma Premiums Strain Public Health
Nov 28, 2024