Smart Factory Economics: A Deep Dive
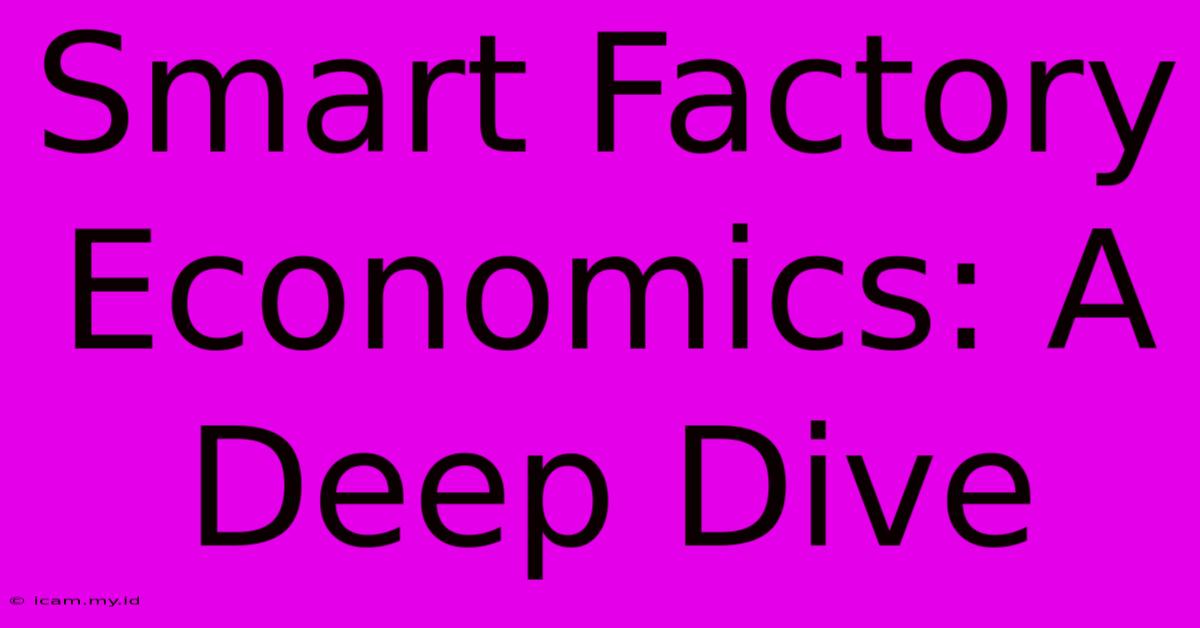
Find more detailed and interesting information on our website. Click the link below to start advanced information: Visit Best Website meltwatermedia.ca. Jangan lewatkan!
Table of Contents
Smart Factory Economics: A Deep Dive
The rise of the smart factory represents a significant shift in manufacturing, promising increased efficiency, reduced costs, and enhanced product quality. But the transition isn't simply a matter of installing new technology; it's a complex economic undertaking requiring careful planning, investment, and a clear understanding of the potential return on investment (ROI). This deep dive explores the economics of smart factories, examining the costs, benefits, and crucial factors to consider for successful implementation.
Understanding the Costs of Smart Factory Implementation
The initial investment in a smart factory can be substantial. It encompasses several key areas:
1. Hardware Investments: This is arguably the most visible cost, including:
- Automated Guided Vehicles (AGVs) and Robots: These automated systems replace manual labor in material handling and production processes. The cost varies greatly depending on the complexity and number of units required.
- Industrial Internet of Things (IIoT) Sensors and Devices: These sensors collect real-time data on various aspects of the manufacturing process, providing crucial insights for optimization. The cost depends on the number of sensors, their sophistication, and the required connectivity infrastructure.
- Computer Numerical Control (CNC) Machines and Advanced Manufacturing Equipment: These highly precise machines automate complex manufacturing tasks, significantly improving accuracy and efficiency. The price varies widely based on the specific capabilities and features.
- Enterprise Resource Planning (ERP) and Manufacturing Execution Systems (MES) Software: These integrated software systems manage and monitor all aspects of the manufacturing process, from planning to execution. Implementation costs include software licenses, customization, and integration with existing systems.
- Cloud Computing Infrastructure: Many smart factory solutions rely on cloud-based data storage and processing, incurring ongoing costs for storage, computing power, and bandwidth.
2. Software and Integration Costs:
Beyond the hardware, significant costs are associated with software development, integration, and maintenance. This includes:
- Software Development and Customization: Integrating various systems and developing custom applications to meet specific needs can be time-consuming and expensive.
- Data Analytics and Business Intelligence Software: Tools for analyzing the vast amounts of data generated by a smart factory are essential for effective decision-making. These tools require investment in both software and skilled personnel.
- Cybersecurity Measures: Protecting the sensitive data generated and processed by a smart factory is paramount. This necessitates investment in robust cybersecurity infrastructure and personnel training.
3. Human Capital Costs:
The transition to a smart factory requires significant investment in human capital:
- Training and Reskilling: Existing employees need training to operate and maintain the new technology. This involves time and financial investment in training programs.
- Hiring Specialized Personnel: Smart factories require specialized expertise in areas like data analytics, cybersecurity, and automation engineering. Attracting and retaining these skilled workers can be challenging and costly.
- Change Management: The transition to a smart factory involves significant organizational changes. Effective change management strategies are crucial to minimize disruption and ensure smooth adoption.
4. Ongoing Operational Costs:
Even after initial implementation, ongoing operational costs are significant:
- Maintenance and Repair: Automated equipment and software require regular maintenance and repairs, adding to the operational budget.
- Software Updates and Upgrades: Keeping software up-to-date requires ongoing investment in licenses and upgrades.
- Energy Consumption: Smart factories often consume more energy than traditional factories, leading to higher energy bills.
- Data Storage and Processing: The cost of storing and processing the vast amounts of data generated by a smart factory can be substantial.
The Economic Benefits of Smart Factories
Despite the significant initial investment, the potential economic benefits of smart factories are substantial:
1. Increased Efficiency and Productivity: Automation and data-driven optimization significantly improve efficiency, leading to increased output with fewer resources.
2. Reduced Production Costs: Automation reduces labor costs, material waste, and downtime, ultimately lowering production costs.
3. Improved Product Quality: Automated processes and real-time monitoring reduce errors and improve consistency, leading to higher product quality.
4. Enhanced Flexibility and Responsiveness: Smart factories can adapt quickly to changing market demands and customer needs, allowing for greater flexibility in production.
5. Better Inventory Management: Real-time data on inventory levels allows for optimized inventory management, reducing storage costs and minimizing stockouts.
6. Improved Supply Chain Management: Improved visibility and communication across the supply chain optimize logistics and reduce lead times.
7. Data-Driven Decision Making: The vast amounts of data generated by a smart factory provide valuable insights for improved decision-making across all aspects of the business.
8. Enhanced Customer Satisfaction: Improved product quality, faster delivery times, and greater customization contribute to enhanced customer satisfaction.
Assessing the ROI of Smart Factory Investments
A thorough ROI analysis is crucial before implementing a smart factory. This involves:
- Quantifying the Costs: Accurately estimate all costs involved, including hardware, software, human capital, and ongoing operational expenses.
- Projecting the Benefits: Develop realistic projections of the benefits, such as increased efficiency, reduced costs, and improved product quality.
- Defining Key Performance Indicators (KPIs): Establish clear KPIs to track the progress and measure the success of the smart factory implementation. These might include production output, defect rates, inventory turnover, and customer satisfaction.
- Considering the Time Horizon: The ROI of a smart factory is often realized over a longer time horizon. Consider the long-term benefits when evaluating the investment.
- Utilizing Simulation and Modeling: Simulate different scenarios to assess the potential impact of different implementation strategies and technologies.
- Performing a Sensitivity Analysis: Assess the impact of potential uncertainties and variations in cost and benefits.
Critical Success Factors for Smart Factory Economics
Successful smart factory implementation requires careful attention to several crucial factors:
- Clear Business Case and Strategic Alignment: Develop a strong business case that justifies the investment and aligns with overall business objectives.
- Phased Implementation: Implement the smart factory in phases, starting with a pilot project to test and refine the approach.
- Data Integration and Management: Ensure seamless integration of data from different sources and develop a robust data management strategy.
- Cybersecurity Measures: Implement strong cybersecurity measures to protect the sensitive data generated by the smart factory.
- Employee Training and Engagement: Invest in employee training and actively engage employees in the transition process.
- Strong Partnerships and Collaboration: Establish partnerships with technology providers and other stakeholders to ensure a successful implementation.
- Continuous Improvement: Implement a culture of continuous improvement to optimize the smart factory's performance over time.
Conclusion: Navigating the Economics of Smart Factory Transformation
The economics of smart factory implementation are complex, requiring careful planning, investment, and a clear understanding of the potential ROI. While the initial investment can be substantial, the long-term benefits of increased efficiency, reduced costs, and enhanced product quality can significantly outweigh the costs. By carefully assessing the costs and benefits, defining clear KPIs, and focusing on critical success factors, manufacturers can successfully navigate the economic challenges and reap the substantial rewards of smart factory transformation. A well-planned and executed smart factory strategy can deliver a significant competitive advantage in today's rapidly evolving manufacturing landscape.
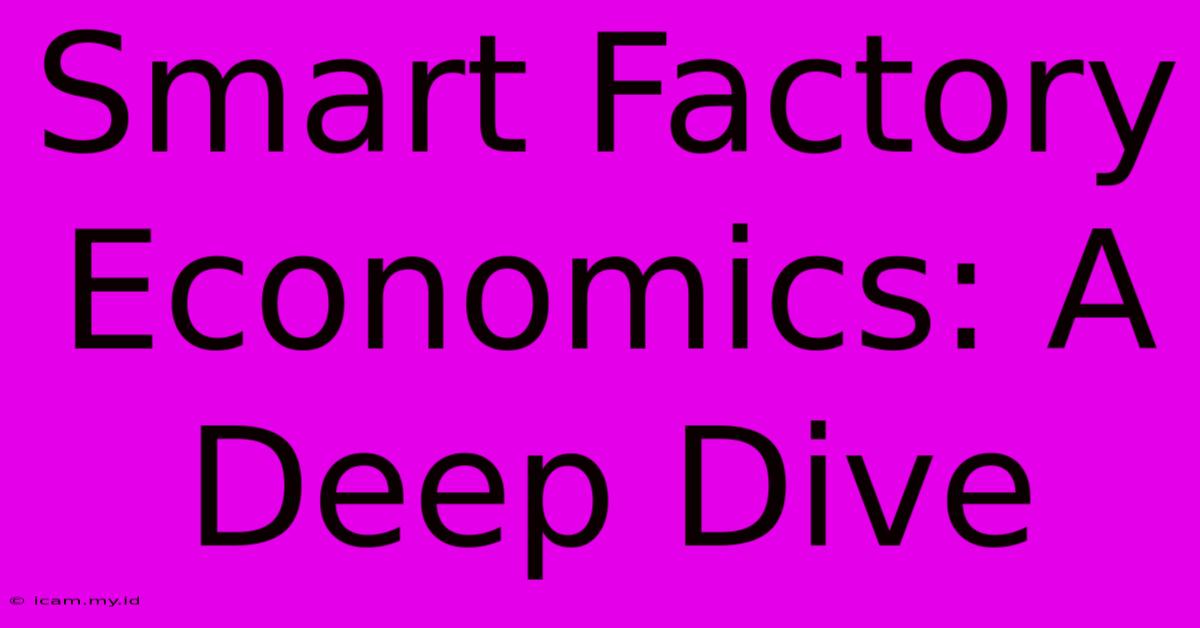
Thank you for visiting our website. Smart Factory Economics: A Deep Dive. We hope the information we provide is helpful to you. Feel free to contact us if you have any questions or need additional assistance. See you next time, and don't forget to save this page!
Kami berterima kasih atas kunjungan Anda untuk melihat lebih jauh. Smart Factory Economics: A Deep Dive. Informasikan kepada kami jika Anda memerlukan bantuan tambahan. Tandai situs ini dan pastikan untuk kembali lagi segera!
Featured Posts
-
Peer Review Validates Covid Vaccine Death Risk
Nov 28, 2024
-
Demand For Cocktail Straws In 2024
Nov 28, 2024
-
New Coach Inspires Team
Nov 28, 2024
-
Analyzing The Cocktail Straw Market
Nov 28, 2024
-
Southern Thailand Floods Impact 100 Residences
Nov 28, 2024