Smart Manufacturing: Beginner's Guide
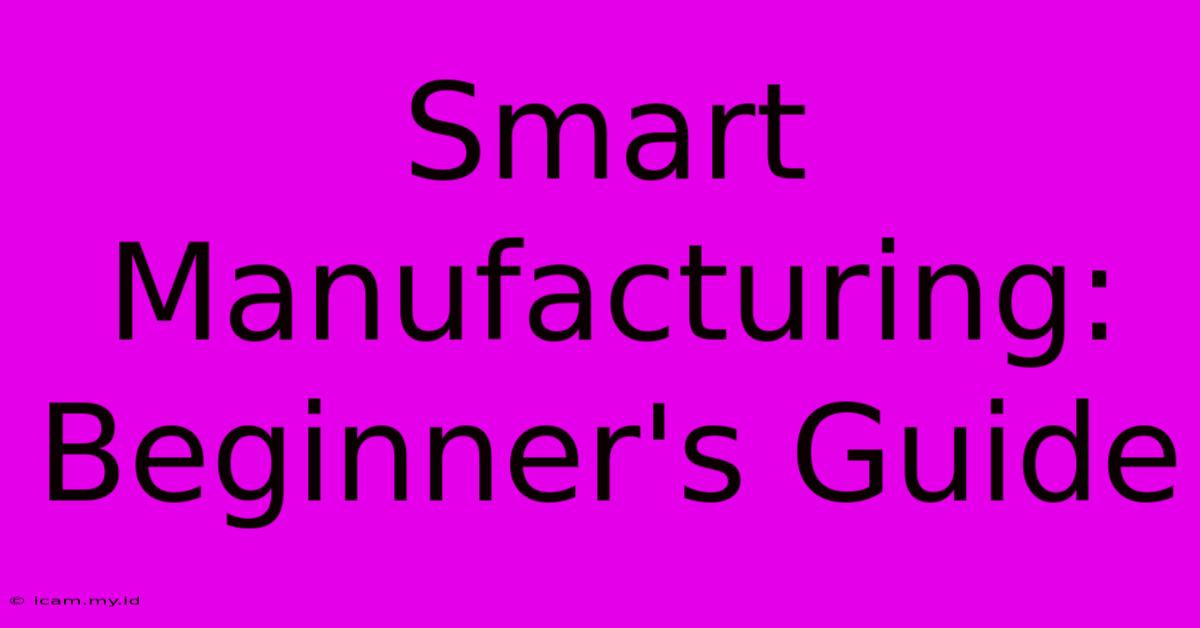
Find more detailed and interesting information on our website. Click the link below to start advanced information: Visit Best Website meltwatermedia.ca. Jangan lewatkan!
Table of Contents
Smart Manufacturing: A Beginner's Guide
Smart manufacturing, also known as Industry 4.0, is revolutionizing how goods are produced. It's no longer just about assembly lines; it's about leveraging data, automation, and connectivity to create a more efficient, responsive, and profitable manufacturing process. This beginner's guide will break down the key concepts, benefits, technologies, and challenges involved in this transformative approach.
What is Smart Manufacturing?
Smart manufacturing involves the integration of various technologies—including IoT (Internet of Things), big data analytics, cloud computing, artificial intelligence (AI), and machine learning (ML)—to optimize all aspects of the manufacturing process. This integrated approach allows for real-time data collection, analysis, and decision-making, leading to significant improvements in efficiency, productivity, and quality.
Instead of relying on traditional, isolated systems, smart manufacturing creates a connected ecosystem where machines, sensors, and software communicate seamlessly. This interconnectedness enables manufacturers to:
- Monitor processes in real-time: Gaining immediate insights into equipment performance, production rates, and potential issues.
- Predict and prevent failures: Utilizing predictive maintenance to minimize downtime and optimize maintenance schedules.
- Automate tasks: Reducing manual labor, improving consistency, and increasing throughput.
- Improve quality control: Implementing automated quality checks and reducing defects.
- Enhance supply chain management: Optimizing inventory levels, streamlining logistics, and improving responsiveness to customer demands.
- Increase agility and flexibility: Quickly adapting to changing market demands and customer preferences.
Key Technologies Driving Smart Manufacturing
Several technologies are central to the implementation of smart manufacturing:
1. Internet of Things (IoT)
IoT devices (sensors, actuators, and other connected equipment) gather data from across the manufacturing floor. This data provides a comprehensive picture of the production process, revealing bottlenecks, inefficiencies, and potential problems.
2. Big Data Analytics
The massive amounts of data generated by IoT devices require sophisticated analytics tools to extract meaningful insights. Big data analytics techniques help manufacturers identify trends, patterns, and anomalies that would be impossible to detect manually.
3. Cloud Computing
Cloud computing provides the scalability and flexibility needed to store and process the vast quantities of data generated by smart manufacturing systems. It also allows for remote access to data and applications, improving collaboration and decision-making.
4. Artificial Intelligence (AI) and Machine Learning (ML)
AI and ML algorithms enable machines to learn from data, make predictions, and automate complex tasks. In smart manufacturing, these technologies can be used for predictive maintenance, quality control, and process optimization.
5. Robotics and Automation
Robots and automated systems play a crucial role in increasing efficiency and productivity. They can perform repetitive tasks with greater speed and accuracy than humans, freeing up human workers for more complex and creative roles.
6. Additive Manufacturing (3D Printing)
3D printing allows for the creation of highly customized parts on demand, reducing lead times and inventory costs. This technology is particularly beneficial for prototyping and producing low-volume, high-value products.
7. Cybersecurity
With the increased connectivity of smart manufacturing systems, cybersecurity is paramount. Robust security measures are essential to protect against cyber threats and ensure the integrity and confidentiality of data.
Benefits of Implementing Smart Manufacturing
The benefits of adopting smart manufacturing practices are numerous and impactful:
- Increased Efficiency: Automation and optimized processes lead to significant improvements in efficiency and productivity.
- Reduced Costs: Predictive maintenance, reduced waste, and improved quality control contribute to lower operational costs.
- Improved Quality: Real-time monitoring and automated quality checks result in higher product quality and fewer defects.
- Enhanced Agility and Flexibility: Smart manufacturing enables manufacturers to quickly adapt to changing market demands and customer preferences.
- Better Decision-Making: Data-driven insights allow for more informed and effective decision-making.
- Improved Supply Chain Management: Optimized inventory levels and streamlined logistics enhance supply chain efficiency.
- Increased Innovation: Smart manufacturing fosters innovation by enabling the development of new products and processes.
Challenges of Implementing Smart Manufacturing
Despite the numerous benefits, implementing smart manufacturing presents several challenges:
- High Initial Investment: The cost of implementing new technologies and infrastructure can be substantial.
- Integration Complexity: Integrating various systems and technologies can be complex and time-consuming.
- Data Security and Privacy: Protecting sensitive data from cyber threats is critical.
- Skills Gap: A skilled workforce is essential to operate and maintain smart manufacturing systems.
- Legacy Systems: Integrating new technologies with existing legacy systems can be challenging.
- Change Management: Implementing smart manufacturing requires significant changes to business processes and workflows.
Getting Started with Smart Manufacturing
For businesses considering implementing smart manufacturing, a phased approach is often recommended. Start by identifying key areas for improvement and selecting technologies that address those specific needs.
1. Assess your current state: Evaluate your existing manufacturing processes, identify bottlenecks and inefficiencies, and determine your key performance indicators (KPIs).
2. Define your goals: Establish clear, measurable goals for your smart manufacturing initiative. This could include reducing production costs, improving quality, or increasing output.
3. Choose the right technologies: Select technologies that align with your goals and resources. Start with a pilot project to test the feasibility and effectiveness of the chosen technologies.
4. Implement a robust cybersecurity strategy: Security is paramount; ensure data integrity and privacy from the outset.
5. Develop a skilled workforce: Invest in training and development to equip your employees with the skills necessary to operate and maintain smart manufacturing systems.
6. Monitor and evaluate: Continuously monitor the performance of your smart manufacturing system and make adjustments as needed.
The Future of Smart Manufacturing
Smart manufacturing is constantly evolving, with new technologies and innovations emerging regularly. The future of smart manufacturing will likely see even greater levels of automation, increased use of AI and ML, and a greater emphasis on sustainability and digital twins. The adoption of digital twins—virtual representations of physical assets—will allow for even more accurate simulations and predictive maintenance, further optimizing manufacturing processes and reducing downtime. Sustainability will also play a crucial role, with manufacturers leveraging smart manufacturing technologies to reduce waste, energy consumption, and their environmental footprint.
In conclusion, smart manufacturing offers significant opportunities for manufacturers to improve efficiency, productivity, and profitability. By embracing these transformative technologies and addressing the associated challenges, manufacturers can position themselves for success in the increasingly competitive global market. The journey to smart manufacturing requires careful planning, investment, and a commitment to continuous improvement, but the rewards are well worth the effort.
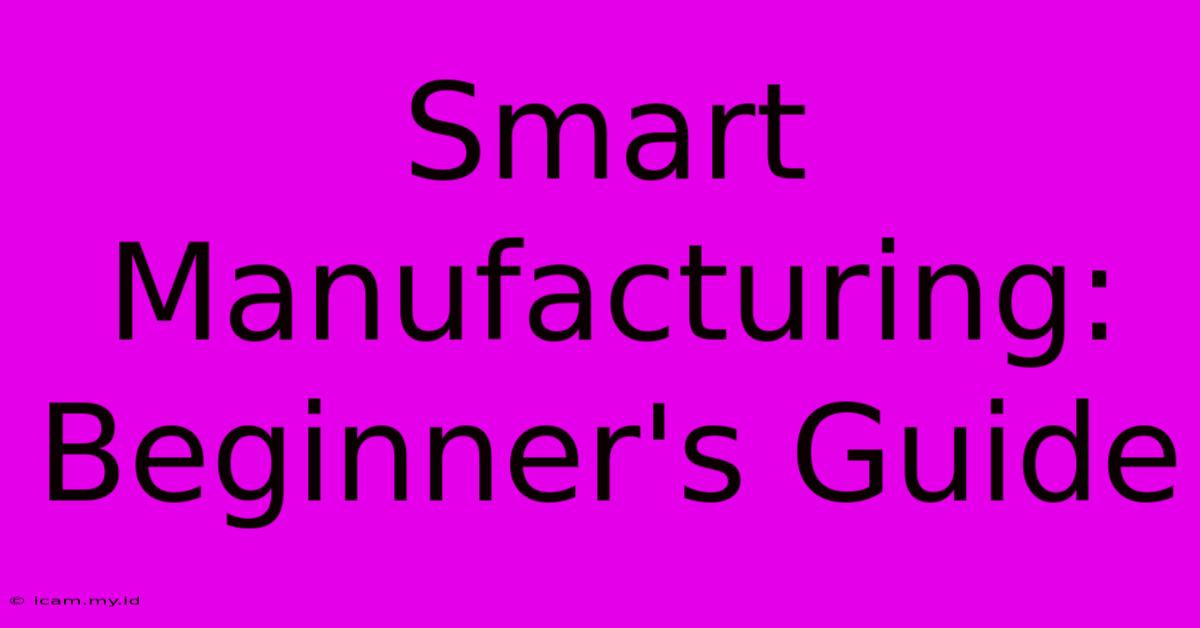
Thank you for visiting our website. Smart Manufacturing: Beginner's Guide. We hope the information we provide is helpful to you. Feel free to contact us if you have any questions or need additional assistance. See you next time, and don't forget to save this page!
Kami berterima kasih atas kunjungan Anda untuk melihat lebih jauh. Smart Manufacturing: Beginner's Guide. Informasikan kepada kami jika Anda memerlukan bantuan tambahan. Tandai situs ini dan pastikan untuk kembali lagi segera!
Featured Posts
-
Thanksgiving 2024 Whats Open Closed
Nov 28, 2024
-
Malaysia Airlines New A330neo Days Away
Nov 28, 2024
-
Karius Retirement Thoughts
Nov 28, 2024
-
Mindfulness Meditation App Market 2024
Nov 28, 2024
-
Macys Parade 2024 11 Bands
Nov 28, 2024