Smart Manufacturing: Core Principles
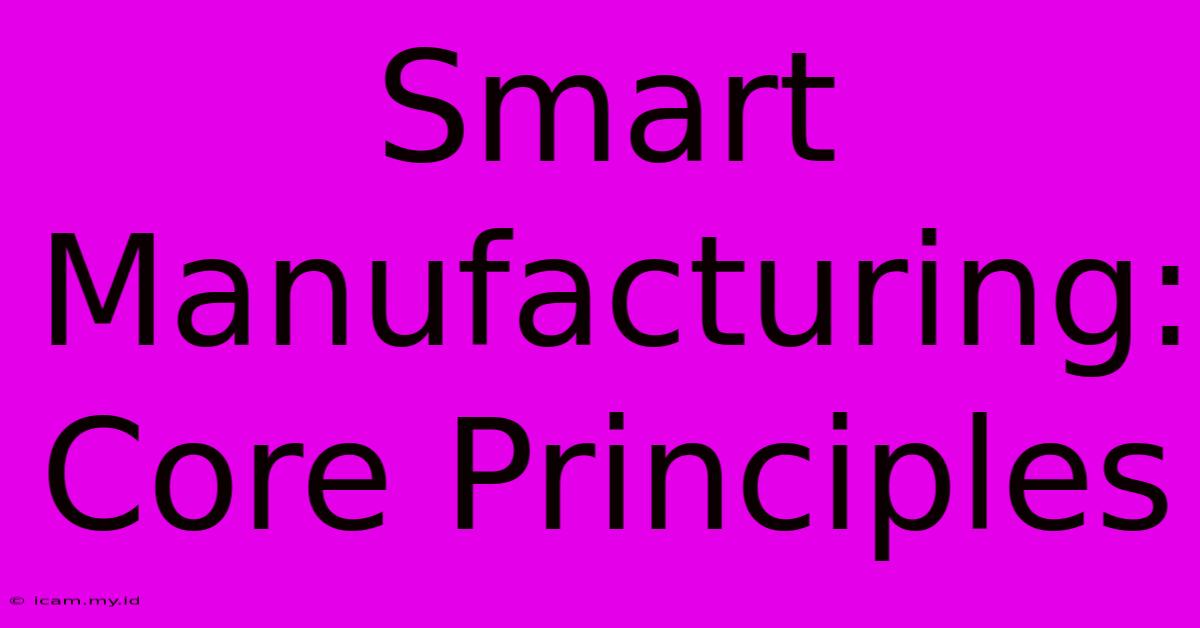
Find more detailed and interesting information on our website. Click the link below to start advanced information: Visit Best Website meltwatermedia.ca. Jangan lewatkan!
Table of Contents
Smart Manufacturing: Core Principles
Smart manufacturing represents a significant evolution in industrial processes, leveraging advanced technologies to optimize efficiency, productivity, and overall competitiveness. It's not just about automation; it's about intelligent automation, data-driven decision-making, and a holistic approach to manufacturing operations. Understanding the core principles underpinning smart manufacturing is crucial for businesses looking to embrace this transformative approach. This article delves deep into these principles, explaining their importance and how they contribute to a smarter, more resilient, and profitable manufacturing environment.
1. Data Acquisition and Integration: The Foundation of Intelligence
At the heart of smart manufacturing lies the ability to collect, analyze, and integrate vast amounts of data from diverse sources. This includes data from machines (sensors on equipment providing real-time performance metrics), processes (tracking production throughput and quality), supply chains (monitoring inventory levels and delivery times), and even external factors like market demand and economic indicators.
The importance of data integration cannot be overstated. Traditional manufacturing often suffers from data silos, where information is trapped within individual departments or systems. Smart manufacturing breaks down these silos through the use of advanced technologies like:
- Industrial Internet of Things (IIoT): Connecting machines and devices to the network allows for real-time data collection and monitoring.
- Cloud Computing: Provides scalable storage and processing power for massive datasets.
- Enterprise Resource Planning (ERP) Systems: Integrate data from various departments into a unified platform.
- Manufacturing Execution Systems (MES): Provide real-time visibility into shop floor operations.
Effective data integration allows for:
- Improved visibility: Real-time insights into all aspects of the manufacturing process.
- Predictive maintenance: Identifying potential equipment failures before they occur.
- Optimized production scheduling: Adjusting schedules based on real-time data and demand.
- Enhanced quality control: Identifying and addressing quality issues early in the process.
2. Advanced Analytics and Decision-Making: Turning Data into Action
Collecting data is only half the battle; the real value comes from analyzing that data to extract meaningful insights and inform better decision-making. Smart manufacturing leverages advanced analytics techniques, including:
- Machine Learning (ML): Algorithms that learn from data to identify patterns and predict future outcomes.
- Artificial Intelligence (AI): Enabling autonomous decision-making and problem-solving.
- Predictive Modeling: Forecasting future events based on historical data and trends.
- Big Data Analytics: Processing and analyzing large, complex datasets to uncover hidden patterns.
By applying advanced analytics, manufacturers can:
- Optimize resource allocation: Efficiently allocating resources based on predicted demand and capacity.
- Improve product quality: Identifying and eliminating sources of defects.
- Reduce production costs: Optimizing processes and minimizing waste.
- Enhance supply chain resilience: Predicting and mitigating potential supply chain disruptions.
3. Automation and Robotics: Enhancing Efficiency and Productivity
Automation is a key component of smart manufacturing, but it's not just about replacing human workers. Instead, it's about augmenting human capabilities and improving efficiency through the strategic deployment of:
- Industrial Robots: Performing repetitive, high-precision tasks.
- Automated Guided Vehicles (AGVs): Transporting materials and goods within the factory.
- Computer Numerical Control (CNC) Machines: Automated machining processes.
- Collaborative Robots (Cobots): Working alongside human workers to enhance productivity.
The benefits of automation in smart manufacturing include:
- Increased productivity: Faster production cycles and higher output.
- Improved quality consistency: Reduced human error and variation.
- Enhanced safety: Minimizing risks associated with hazardous tasks.
- Reduced labor costs: Automating repetitive tasks frees up human workers for more complex tasks.
4. Cybersecurity: Protecting the Connected Enterprise
The interconnected nature of smart manufacturing introduces significant cybersecurity risks. Protecting sensitive data and ensuring the integrity of manufacturing systems is paramount. Key cybersecurity considerations include:
- Network security: Protecting the manufacturing network from unauthorized access and cyberattacks.
- Data security: Encrypting sensitive data and implementing access control measures.
- Device security: Securing industrial control systems (ICS) and other connected devices.
- Incident response: Developing and implementing procedures to respond to security incidents.
A robust cybersecurity strategy is critical for:
- Protecting intellectual property: Safeguarding valuable designs and processes.
- Maintaining operational continuity: Preventing disruptions caused by cyberattacks.
- Ensuring data integrity: Maintaining the accuracy and reliability of manufacturing data.
- Complying with regulations: Meeting industry-specific cybersecurity standards.
5. Human-Machine Collaboration: The Future of Work
Smart manufacturing is not about replacing human workers; it's about enhancing their capabilities and creating a collaborative environment between humans and machines. This involves:
- Upskilling and reskilling the workforce: Providing training and development opportunities to equip workers with the skills needed to operate and maintain smart manufacturing systems.
- Creating user-friendly interfaces: Making it easier for workers to interact with automated systems.
- Designing ergonomic workspaces: Creating a comfortable and safe work environment for human-machine collaboration.
- Leveraging human expertise: Utilizing human judgment and decision-making in areas where automation is not yet feasible.
Effective human-machine collaboration leads to:
- Improved worker satisfaction: Empowering workers to perform more challenging and rewarding tasks.
- Enhanced productivity and efficiency: Combining human ingenuity with the precision and speed of automation.
- Increased innovation: Fostering a collaborative environment where new ideas and solutions can emerge.
- Greater adaptability to change: Creating a flexible and responsive manufacturing environment.
Conclusion: Embracing the Smart Manufacturing Transformation
Smart manufacturing is not a single technology but a holistic approach to manufacturing that leverages advanced technologies to optimize efficiency, productivity, and competitiveness. By focusing on the core principles of data integration, advanced analytics, automation, cybersecurity, and human-machine collaboration, manufacturers can successfully navigate the transformation and reap the significant benefits of this transformative approach. The future of manufacturing is smart, connected, and collaborative, and those who embrace these principles will be best positioned to thrive in the increasingly competitive global marketplace.
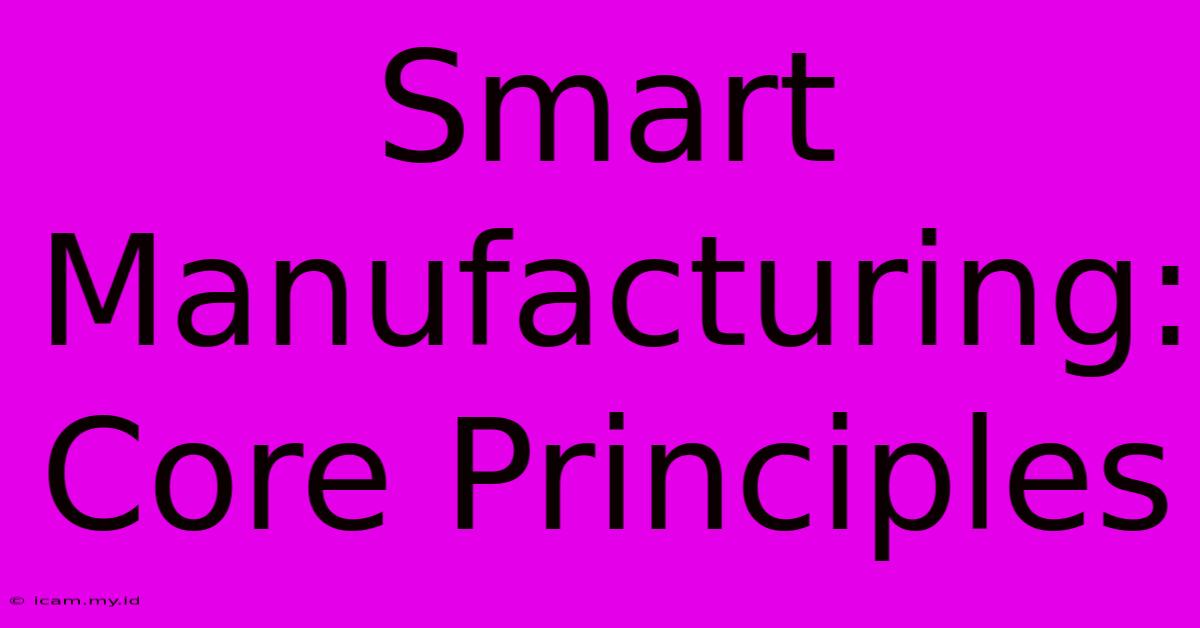
Thank you for visiting our website. Smart Manufacturing: Core Principles. We hope the information we provide is helpful to you. Feel free to contact us if you have any questions or need additional assistance. See you next time, and don't forget to save this page!
Kami berterima kasih atas kunjungan Anda untuk melihat lebih jauh. Smart Manufacturing: Core Principles. Informasikan kepada kami jika Anda memerlukan bantuan tambahan. Tandai situs ini dan pastikan untuk kembali lagi segera!
Featured Posts
-
Ananda Krishnan Obituary Media Mogul 86
Nov 28, 2024
-
Ananda Krishnan Passes Official Confirmation
Nov 28, 2024
-
Tributes Pour In After Ananda Krishnans Death At 86
Nov 28, 2024
-
Selangors Acl 2 A Tough Road Ahead
Nov 28, 2024
-
Death Of Billionaire Ananda Krishnan Statement
Nov 28, 2024