Smart Manufacturing: Core Technologies
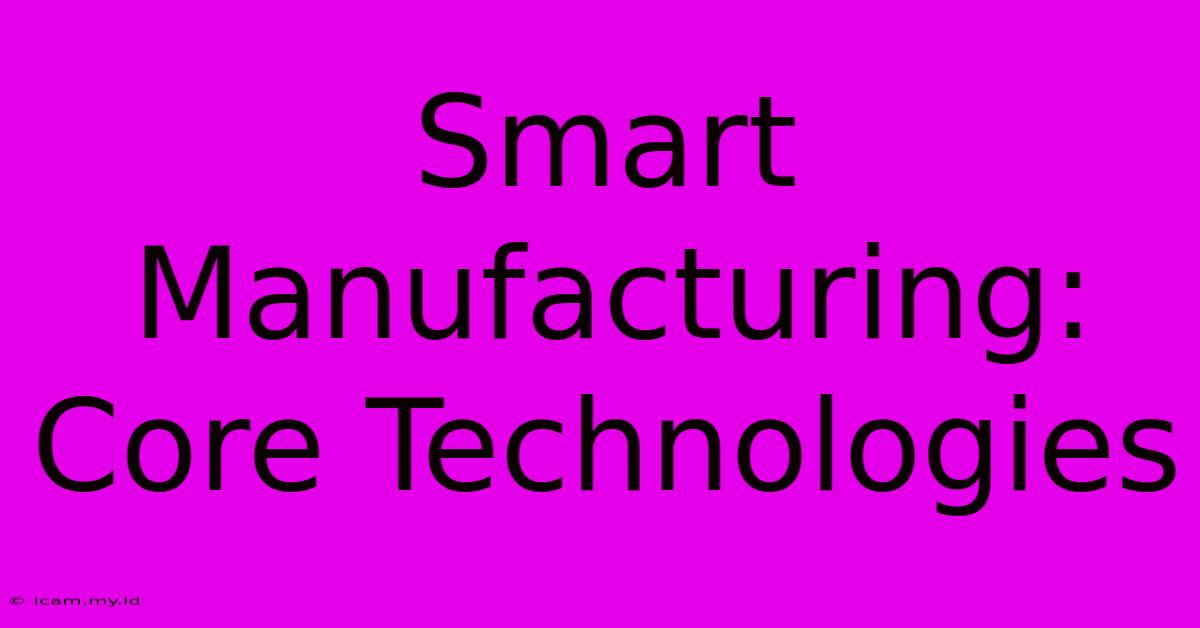
Find more detailed and interesting information on our website. Click the link below to start advanced information: Visit Best Website meltwatermedia.ca. Jangan lewatkan!
Table of Contents
Smart Manufacturing: Core Technologies Transforming the Industrial Landscape
Smart manufacturing, also known as Industry 4.0, is revolutionizing the industrial landscape by integrating advanced technologies to optimize processes, enhance efficiency, and improve overall productivity. This paradigm shift moves beyond traditional automation, focusing on data-driven decision-making, real-time insights, and flexible, responsive manufacturing systems. Understanding the core technologies driving this transformation is crucial for businesses looking to stay competitive in today's dynamic market.
This article will delve into the key technologies powering smart manufacturing, exploring their capabilities, applications, and the transformative impact they have on various industries.
1. Industrial Internet of Things (IIoT): The Nervous System of Smart Factories
The Industrial Internet of Things (IIoT) forms the foundation of smart manufacturing. It involves connecting machines, sensors, and other industrial assets to a network, enabling real-time data collection and analysis. This interconnected ecosystem allows for continuous monitoring of equipment performance, predictive maintenance, and optimized resource allocation.
Key Components of IIoT in Smart Manufacturing:
- Sensors: These devices collect data on various parameters like temperature, pressure, vibration, and speed, providing crucial insights into equipment health and operational efficiency.
- Actuators: These components respond to commands from the control system, adjusting parameters and executing actions based on real-time data analysis.
- Connectivity: Reliable and secure network infrastructure, including wired and wireless communication protocols, is essential for seamless data exchange. This includes technologies like Ethernet, Wi-Fi, 5G, and even newer technologies like LoRaWAN for long-range communication in challenging environments.
- Data Analytics: Advanced analytics platforms process the massive volumes of data generated by IIoT devices, extracting meaningful insights and supporting data-driven decision-making. This includes techniques like machine learning and artificial intelligence.
Impact of IIoT: IIoT enables predictive maintenance, reducing downtime and maintenance costs. It also facilitates optimized production scheduling, improves quality control, and enhances overall operational efficiency.
2. Big Data and Analytics: Unlocking the Power of Industrial Data
Smart manufacturing generates an enormous amount of data from various sources. Big data analytics techniques are essential for processing, analyzing, and interpreting this data to gain valuable insights. These insights can be used to improve decision-making, optimize processes, and identify potential problems before they occur.
Key Applications of Big Data Analytics in Smart Manufacturing:
- Predictive Maintenance: By analyzing historical data on equipment performance, manufacturers can predict potential failures and schedule maintenance proactively, minimizing downtime.
- Quality Control: Real-time data analysis can identify defects and inconsistencies in the manufacturing process, enabling immediate corrective actions and improving product quality.
- Supply Chain Optimization: Analyzing data on inventory levels, demand patterns, and supplier performance can optimize supply chain logistics and reduce lead times.
- Process Optimization: By analyzing data from various stages of the manufacturing process, manufacturers can identify bottlenecks and inefficiencies, leading to process improvements.
Impact of Big Data and Analytics: Effective use of big data and analytics can significantly reduce operational costs, improve product quality, and increase overall productivity.
3. Cloud Computing: Scaling and Sharing Manufacturing Intelligence
Cloud computing offers a scalable and cost-effective solution for storing, processing, and analyzing the vast amounts of data generated by smart manufacturing systems. It provides access to powerful computing resources and advanced analytics tools, without the need for significant upfront investment in infrastructure.
Key Benefits of Cloud Computing in Smart Manufacturing:
- Scalability: Cloud computing resources can be scaled up or down based on demand, ensuring that manufacturers always have the computing power they need.
- Cost-Effectiveness: Cloud computing eliminates the need for significant investment in hardware and IT infrastructure.
- Data Security: Reputable cloud providers offer robust security measures to protect sensitive data.
- Collaboration: Cloud platforms facilitate collaboration between different departments and stakeholders, fostering a more integrated and efficient manufacturing ecosystem.
Impact of Cloud Computing: Cloud computing enables manufacturers to leverage advanced analytics tools and collaborate more effectively, improving efficiency and driving innovation.
4. Artificial Intelligence (AI) and Machine Learning (ML): Automating Decisions and Optimizing Processes
Artificial intelligence (AI) and machine learning (ML) are transforming smart manufacturing by automating decision-making, optimizing processes, and improving overall productivity. These technologies enable machines to learn from data, adapt to changing conditions, and make predictions about future outcomes.
Key Applications of AI and ML in Smart Manufacturing:
- Predictive Maintenance: AI algorithms can analyze sensor data to predict equipment failures with high accuracy, enabling proactive maintenance and minimizing downtime.
- Quality Control: AI-powered vision systems can automatically inspect products for defects, ensuring high quality and reducing waste.
- Process Optimization: AI algorithms can optimize manufacturing processes by adjusting parameters in real-time, improving efficiency and reducing costs.
- Robotics and Automation: AI enables advanced robotics to perform complex tasks autonomously, increasing efficiency and flexibility.
Impact of AI and ML: AI and ML are driving significant improvements in efficiency, productivity, and product quality in smart manufacturing environments.
5. Cybersecurity: Protecting the Integrity of Smart Manufacturing Systems
With the increasing interconnectedness of smart manufacturing systems, cybersecurity is paramount. Protecting sensitive data and preventing cyberattacks are essential to maintain the integrity and reliability of these systems.
Key Cybersecurity Considerations in Smart Manufacturing:
- Network Security: Implementing robust network security measures to protect against unauthorized access and cyberattacks is crucial. This includes firewalls, intrusion detection systems, and secure communication protocols.
- Data Security: Implementing strong data encryption and access control mechanisms to protect sensitive data is essential.
- Device Security: Securing individual devices and ensuring their firmware is up-to-date is vital to prevent vulnerabilities.
- Incident Response: Having a well-defined incident response plan to handle potential cyberattacks is essential to minimize damage.
Impact of Cybersecurity: Robust cybersecurity measures are essential for maintaining the reliability, integrity, and security of smart manufacturing systems.
6. Digital Twins: Creating Virtual Representations of Physical Assets
A digital twin is a virtual representation of a physical asset, process, or system. It allows manufacturers to simulate and analyze different scenarios, optimize processes, and predict future performance.
Key Applications of Digital Twins in Smart Manufacturing:
- Process Optimization: Digital twins can be used to simulate different manufacturing processes and identify potential bottlenecks and inefficiencies.
- Predictive Maintenance: By simulating the behavior of equipment, digital twins can predict potential failures and optimize maintenance schedules.
- Product Development: Digital twins can be used to simulate the performance of new products before they are manufactured, reducing development time and costs.
- Training and Simulation: Digital twins can provide a safe and controlled environment for training employees on new equipment and processes.
Impact of Digital Twins: Digital twins provide valuable insights into the performance of physical assets, enabling manufacturers to optimize processes, reduce costs, and improve efficiency.
7. Augmented Reality (AR) and Virtual Reality (VR): Enhancing Human-Machine Interaction
Augmented reality (AR) and virtual reality (VR) are enhancing human-machine interaction in smart manufacturing. AR overlays digital information onto the real world, providing workers with real-time insights and guidance. VR creates immersive simulated environments for training and simulation.
Key Applications of AR and VR in Smart Manufacturing:
- Training and Simulation: VR can provide a safe and immersive environment for training employees on complex equipment and processes.
- Remote Assistance: AR can enable remote experts to provide assistance to workers on the factory floor.
- Maintenance and Repair: AR can provide workers with real-time information and guidance during maintenance and repair tasks.
- Quality Control: AR can overlay digital information onto physical products, enabling workers to easily identify defects.
Impact of AR and VR: AR and VR are improving worker productivity, reducing training costs, and enhancing the overall efficiency of smart manufacturing operations.
Conclusion: Embracing the Future of Manufacturing
Smart manufacturing is transforming the industrial landscape, enabling manufacturers to achieve greater efficiency, productivity, and competitiveness. By integrating these core technologies, manufacturers can unlock the full potential of Industry 4.0 and create smarter, more resilient, and more profitable operations. The continuous evolution of these technologies promises further advancements and even more transformative impacts on manufacturing in the years to come. Staying informed about these advancements and strategically integrating them into your operations is crucial for thriving in the future of manufacturing.
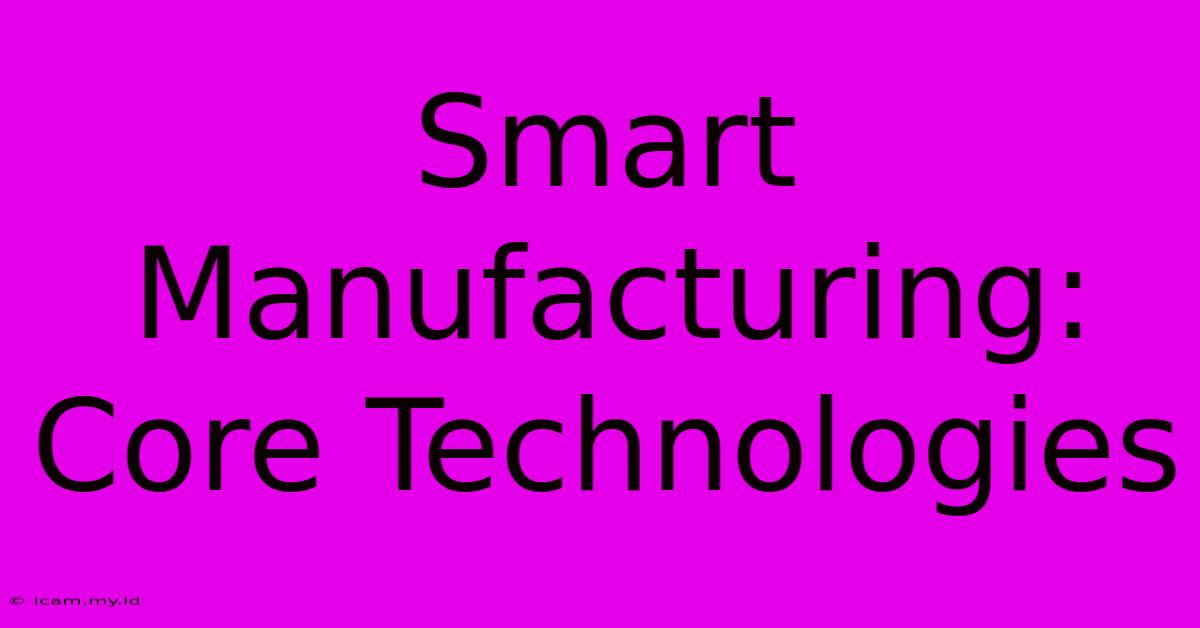
Thank you for visiting our website. Smart Manufacturing: Core Technologies. We hope the information we provide is helpful to you. Feel free to contact us if you have any questions or need additional assistance. See you next time, and don't forget to save this page!
Kami berterima kasih atas kunjungan Anda untuk melihat lebih jauh. Smart Manufacturing: Core Technologies. Informasikan kepada kami jika Anda memerlukan bantuan tambahan. Tandai situs ini dan pastikan untuk kembali lagi segera!
Featured Posts
-
Researchers Recover Lanthanum Metal
Nov 28, 2024
-
Social Media Ban For Kids In Australia
Nov 28, 2024
-
Australias Social Media Kid Ban Update
Nov 28, 2024
-
Singapore Gets Its First Tous Les Jours Bakery
Nov 28, 2024
-
2024 Macys Thanksgiving Day Parade
Nov 28, 2024