Unlocking Economic Value: Smart Factories
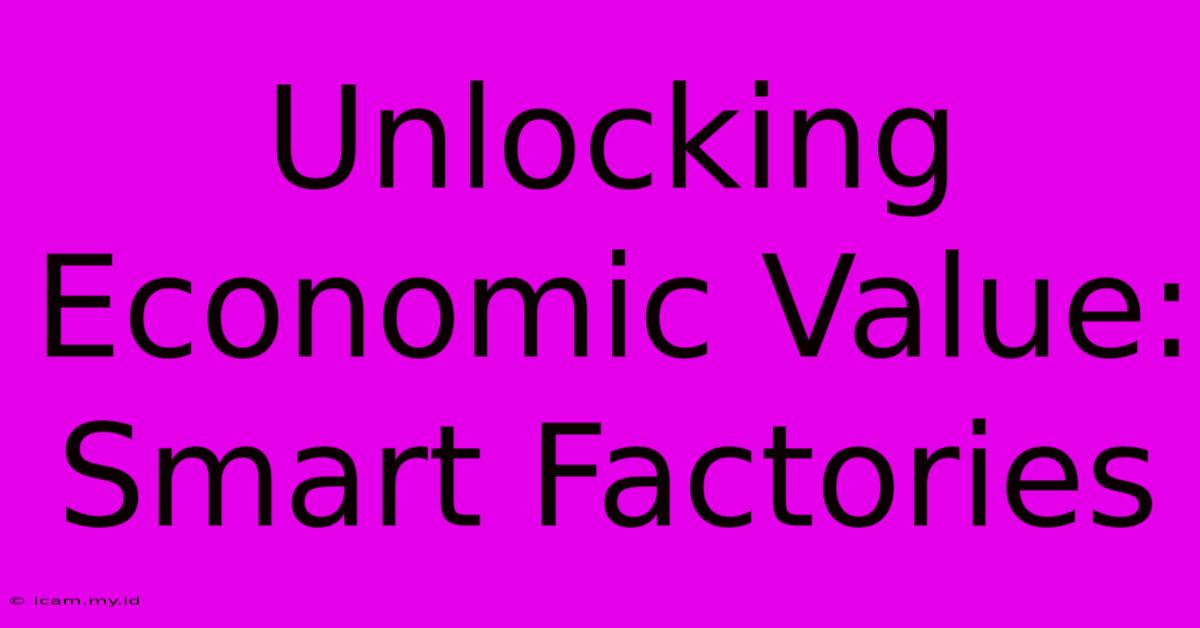
Find more detailed and interesting information on our website. Click the link below to start advanced information: Visit Best Website meltwatermedia.ca. Jangan lewatkan!
Table of Contents
Unlocking Economic Value: Smart Factories
The manufacturing landscape is undergoing a radical transformation, driven by the convergence of advanced technologies under the banner of "Smart Factories." No longer just automated production lines, these facilities leverage data-driven insights, interconnected systems, and advanced analytics to optimize every aspect of production, from design and planning to manufacturing, delivery, and even product lifecycle management. This article delves into the core components of smart factories, explores their significant economic advantages, and addresses the challenges involved in their implementation.
What is a Smart Factory?
A smart factory isn't merely about installing robots; it's a holistic approach to manufacturing that leverages the power of Industry 4.0 technologies. This encompasses a wide range of interconnected systems and technologies, including:
-
Internet of Things (IoT): Sensors and actuators embedded in machines, products, and the factory environment collect vast amounts of real-time data. This data provides invaluable insights into equipment performance, production processes, and potential bottlenecks.
-
Cloud Computing: The massive datasets generated by IoT devices are processed and analyzed using cloud-based platforms. This enables advanced analytics and predictive modeling, informing decision-making across the entire organization.
-
Big Data Analytics: Analyzing this vast amount of data helps identify trends, predict failures, optimize production schedules, and improve overall efficiency. Machine learning algorithms play a crucial role in extracting valuable insights from this data.
-
Artificial Intelligence (AI): AI algorithms drive automation, optimize processes, and enable predictive maintenance. AI-powered robots can perform complex tasks with greater precision and flexibility than traditional automation systems.
-
Cybersecurity: With interconnected systems comes increased vulnerability to cyberattacks. Robust cybersecurity measures are crucial to protecting sensitive data and maintaining operational continuity.
-
Advanced Robotics: Robots play a vital role in automating tasks, improving productivity, and enhancing product quality. Collaborative robots (cobots) work alongside human workers, enhancing their capabilities and improving safety.
-
Digital Twins: Virtual representations of physical assets and processes enable simulations and predictive modeling, allowing manufacturers to optimize designs, troubleshoot problems, and train personnel without disrupting production.
The Economic Value Proposition of Smart Factories
The economic benefits of adopting smart factory technologies are substantial and far-reaching:
1. Increased Efficiency and Productivity:
By automating repetitive tasks, optimizing production schedules, and minimizing downtime, smart factories significantly boost efficiency and productivity. Real-time data analysis allows for rapid identification and resolution of bottlenecks, leading to faster production cycles and reduced lead times.
2. Reduced Costs:
Smart factories contribute to significant cost reductions in several ways:
- Lower labor costs: Automation reduces the need for manual labor in repetitive tasks.
- Minimized waste: Data-driven optimization reduces material waste and energy consumption.
- Improved quality control: Fewer defects mean lower rework costs and improved customer satisfaction.
- Predictive maintenance: By predicting equipment failures, smart factories minimize downtime and associated costs.
3. Enhanced Product Quality:
The precision and consistency of automated processes, coupled with real-time quality monitoring, leads to higher product quality and fewer defects. This improves customer satisfaction and strengthens brand reputation.
4. Improved Supply Chain Management:
Smart factories integrate seamlessly with supply chain partners, allowing for real-time tracking of materials, improved inventory management, and streamlined logistics. This enhances agility and responsiveness to market demands.
5. Data-Driven Decision Making:
The wealth of data generated by smart factories empowers manufacturers to make informed, data-driven decisions across all aspects of their operations. This leads to better resource allocation, improved strategies, and enhanced profitability.
6. Innovation and New Product Development:
The ability to rapidly prototype and test new products using digital twins accelerates innovation and allows manufacturers to respond quickly to market trends. This leads to the development of new products and services.
7. Improved Employee Engagement and Skill Development:
While automation reduces the need for manual labor in repetitive tasks, it also creates new opportunities for employees to develop advanced skills in areas such as data analytics, AI, and robotics. This enhances employee engagement and fosters a culture of continuous improvement.
Challenges in Implementing Smart Factories
Despite the significant economic benefits, implementing smart factories presents several challenges:
1. High Initial Investment Costs:
The initial investment required to implement smart factory technologies can be substantial, requiring careful planning and financial modeling.
2. Data Security and Privacy Concerns:
The increased connectivity and data collection inherent in smart factories raise concerns about data security and privacy. Robust cybersecurity measures are crucial to mitigate these risks.
3. Integration Complexity:
Integrating diverse systems and technologies can be complex and challenging, requiring careful planning and expertise.
4. Skills Gap:
The adoption of advanced technologies requires a skilled workforce capable of operating and maintaining complex systems. Bridging the skills gap through training and education is essential.
5. Legacy Systems:
Integrating smart factory technologies with legacy systems can be difficult and may require significant modifications or replacements.
6. Lack of Standardization:
The lack of industry standards for communication protocols and data formats can hinder interoperability between different systems and technologies.
Overcoming the Challenges: A Strategic Approach
Successfully implementing a smart factory requires a strategic approach that addresses these challenges:
-
Phased Implementation: A phased approach, starting with pilot projects in specific areas, allows for gradual integration and minimizes risks.
-
Strong Leadership and Collaboration: Successful implementation requires strong leadership, cross-functional collaboration, and clear communication.
-
Investment in Training and Development: Investing in training and development programs helps bridge the skills gap and ensure that employees have the necessary skills to operate and maintain smart factory technologies.
-
Cybersecurity Measures: Implementing robust cybersecurity measures is crucial to protecting sensitive data and preventing cyberattacks.
-
Data Management and Analytics Strategies: Developing robust data management and analytics strategies is crucial to effectively leverage the wealth of data generated by smart factories.
-
Partnerships and Collaboration: Collaborating with technology providers, system integrators, and other industry partners can help overcome implementation challenges.
Conclusion: Embracing the Future of Manufacturing
Smart factories represent a paradigm shift in manufacturing, offering immense economic value through increased efficiency, reduced costs, enhanced product quality, and improved supply chain management. While implementing these technologies presents significant challenges, a strategic approach that addresses these challenges head-on will pave the way for manufacturers to unlock their full potential and thrive in the increasingly competitive global marketplace. The future of manufacturing is undeniably smart, and embracing this transformation is crucial for long-term success and economic prosperity.
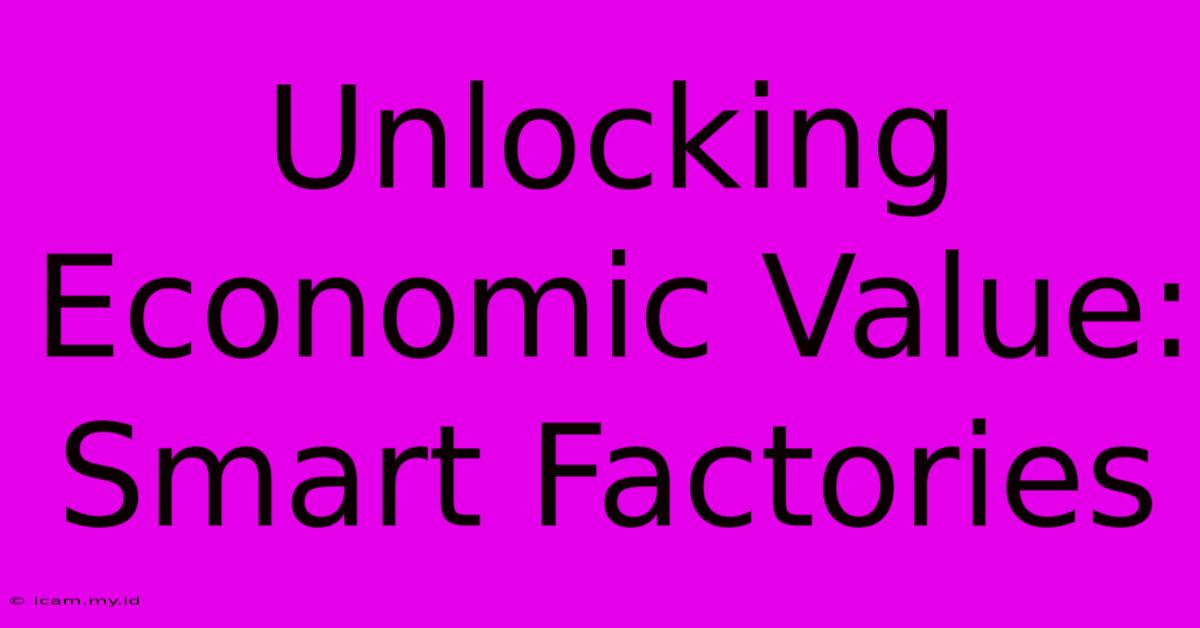
Thank you for visiting our website. Unlocking Economic Value: Smart Factories. We hope the information we provide is helpful to you. Feel free to contact us if you have any questions or need additional assistance. See you next time, and don't forget to save this page!
Kami berterima kasih atas kunjungan Anda untuk melihat lebih jauh. Unlocking Economic Value: Smart Factories. Informasikan kepada kami jika Anda memerlukan bantuan tambahan. Tandai situs ini dan pastikan untuk kembali lagi segera!
Featured Posts
-
Ballon D Or And Award Snub For Vinicius
Nov 28, 2024
-
Paper Straw Market To Boom Key Players
Nov 28, 2024
-
Ananda Krishnan Billionaire Tycoon Passes Away
Nov 28, 2024
-
Malaysian Billionaire Ananda Krishnan Passes Away
Nov 28, 2024
-
Kinoshi Appointed Selangor Fc Manager
Nov 28, 2024