Introduction To Smart Manufacturing
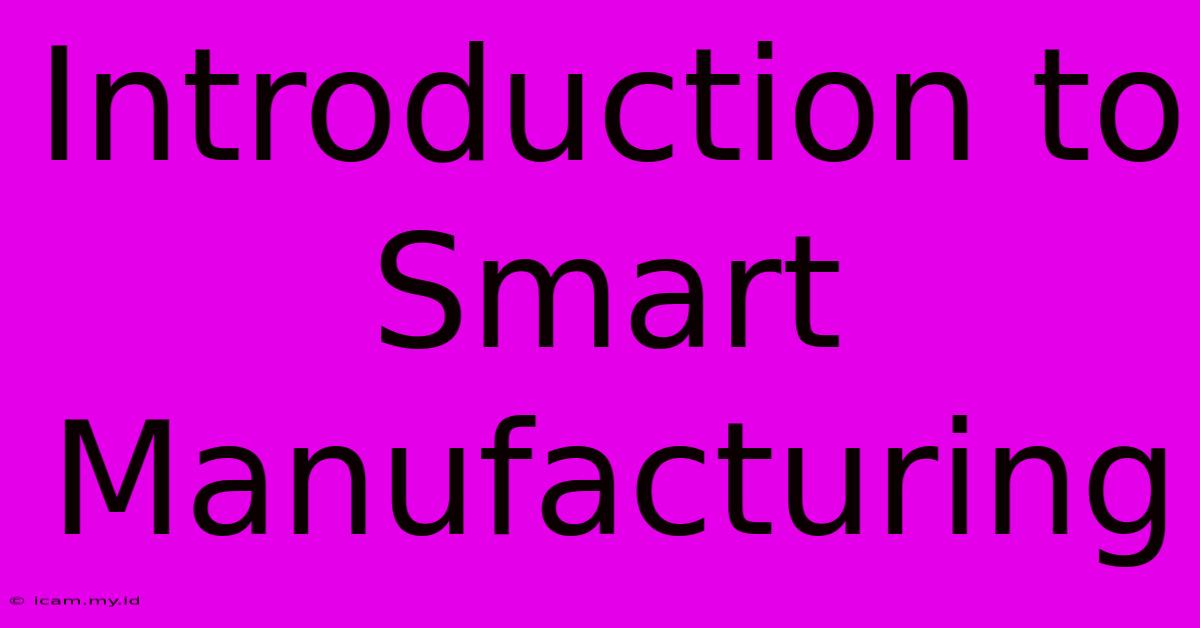
Find more detailed and interesting information on our website. Click the link below to start advanced information: Visit Best Website meltwatermedia.ca. Jangan lewatkan!
Table of Contents
Introduction to Smart Manufacturing: A Comprehensive Guide
Smart manufacturing, also known as Industry 4.0, represents a paradigm shift in how goods are produced. It leverages advanced technologies to create a more efficient, flexible, and responsive manufacturing environment. This comprehensive guide delves into the core concepts, technologies, benefits, and challenges associated with smart manufacturing, providing a thorough understanding for both beginners and experienced professionals.
What is Smart Manufacturing?
Smart manufacturing goes beyond automation; it's about creating a connected and intelligent manufacturing ecosystem. It integrates various technologies like IoT (Internet of Things), AI (Artificial Intelligence), Machine Learning (ML), cloud computing, big data analytics, and robotics to optimize every stage of the manufacturing process, from design and planning to production, delivery, and even product lifecycle management. The goal is to achieve increased efficiency, improved quality, reduced costs, and enhanced agility in responding to market demands.
Key Characteristics of Smart Manufacturing:
- Connectivity: Seamless communication and data exchange between machines, systems, and people across the entire manufacturing value chain.
- Data-driven Decision Making: Utilizing real-time data analytics to identify trends, optimize processes, and make informed decisions.
- Automation: Automating repetitive tasks and processes to increase efficiency and reduce human error.
- Flexibility and Adaptability: Quickly adapting to changing market demands and production requirements.
- Predictive Maintenance: Using data analysis to predict equipment failures and prevent downtime.
- Improved Quality Control: Implementing automated quality checks and real-time monitoring to reduce defects.
- Enhanced Collaboration: Fostering better collaboration between different departments, suppliers, and customers.
Core Technologies Driving Smart Manufacturing
Several technologies underpin the capabilities of smart manufacturing. Understanding these technologies is crucial to implementing successful smart manufacturing initiatives.
1. Internet of Things (IoT):
IoT forms the backbone of smart manufacturing. It connects machines, sensors, and other devices to collect and exchange data in real-time. This data provides valuable insights into production processes, allowing for better monitoring, control, and optimization. Examples include connected machines that report on their operational status, sensors monitoring environmental conditions, and RFID tags tracking materials throughout the production process.
2. Artificial Intelligence (AI) and Machine Learning (ML):
AI and ML are essential for analyzing the vast amounts of data generated by IoT devices. These technologies enable predictive maintenance, quality control, and process optimization. ML algorithms can identify patterns and anomalies in data, predicting potential equipment failures and enabling proactive maintenance. AI can be used to automate decision-making processes, such as optimizing production schedules or adjusting machine parameters in real-time.
3. Cloud Computing:
Cloud computing provides scalable and cost-effective storage and processing for the massive datasets generated in smart manufacturing. It allows for centralized data management, facilitating data analysis and collaboration across different locations. Cloud platforms also offer various tools and services that support smart manufacturing initiatives.
4. Big Data Analytics:
Big data analytics is critical for extracting meaningful insights from the large volumes of data collected in smart manufacturing environments. Sophisticated analytical techniques are used to identify trends, patterns, and anomalies, enabling informed decision-making and process optimization. This analysis can reveal areas for improvement in efficiency, quality, and cost reduction.
5. Robotics and Automation:
Robotics and automation play a significant role in automating repetitive and dangerous tasks, increasing efficiency and improving safety. Robots can perform tasks with higher precision and speed than humans, leading to improved quality and reduced production time. Automated guided vehicles (AGVs) and automated storage and retrieval systems (AS/RS) further enhance efficiency in material handling and logistics.
6. Cybersecurity:
With increased connectivity comes increased vulnerability to cyberattacks. Robust cybersecurity measures are critical to protecting sensitive data and ensuring the integrity and reliability of smart manufacturing systems. This includes implementing strong authentication protocols, network security measures, and data encryption.
Benefits of Implementing Smart Manufacturing
Adopting smart manufacturing strategies offers numerous advantages, leading to significant improvements across various aspects of the business.
1. Increased Efficiency and Productivity:
Automation and optimized processes significantly increase manufacturing efficiency and productivity. Real-time data analysis helps identify bottlenecks and inefficiencies, enabling timely interventions and improvements.
2. Improved Quality and Reduced Defects:
Real-time monitoring and quality control measures ensure consistent product quality and minimize defects. Predictive maintenance prevents equipment failures that can lead to production delays and quality issues.
3. Reduced Costs and Waste:
Optimized processes, predictive maintenance, and reduced defects lead to significant cost savings. Minimizing waste through efficient resource utilization also contributes to cost reduction.
4. Enhanced Agility and Responsiveness:
Smart manufacturing enables faster response to changing market demands and customer requirements. Flexible production systems can quickly adapt to new product designs and production volumes.
5. Improved Supply Chain Management:
Real-time visibility into the supply chain enables better inventory management, improved logistics, and optimized supplier relationships. This leads to more efficient and cost-effective supply chain operations.
6. Better Data-Driven Decision Making:
Access to real-time data and advanced analytics allows for more informed decision-making across all aspects of manufacturing. This leads to more effective strategic planning and operational improvements.
Challenges of Implementing Smart Manufacturing
Despite the numerous benefits, implementing smart manufacturing also presents several challenges.
1. High Initial Investment:
Implementing smart manufacturing technologies requires significant upfront investment in hardware, software, and skilled personnel. This can be a barrier for smaller companies with limited resources.
2. Data Security and Privacy Concerns:
Increased connectivity brings increased risks of cyberattacks and data breaches. Implementing robust cybersecurity measures is crucial to protect sensitive data and ensure system reliability.
3. Integration Complexity:
Integrating various smart manufacturing technologies can be complex and challenging, requiring specialized expertise and careful planning. Interoperability issues between different systems can also create problems.
4. Skills Gap:
The adoption of smart manufacturing technologies requires a workforce with the necessary skills and expertise to operate and maintain these systems. Bridging the skills gap through training and education is essential.
5. Change Management:
Implementing smart manufacturing requires significant changes to existing processes and workflows. Effective change management strategies are needed to ensure smooth transitions and employee buy-in.
Conclusion
Smart manufacturing is transforming the manufacturing industry, offering significant benefits in terms of efficiency, productivity, quality, and agility. While challenges exist, the potential rewards are substantial. Companies that successfully embrace smart manufacturing technologies will be well-positioned to compete in the increasingly demanding global marketplace. The future of manufacturing is undeniably smart, and understanding its intricacies is crucial for success in the years to come. Continued investment in research and development, along with a focus on workforce training and collaboration, will be key to unlocking the full potential of this transformative technology.
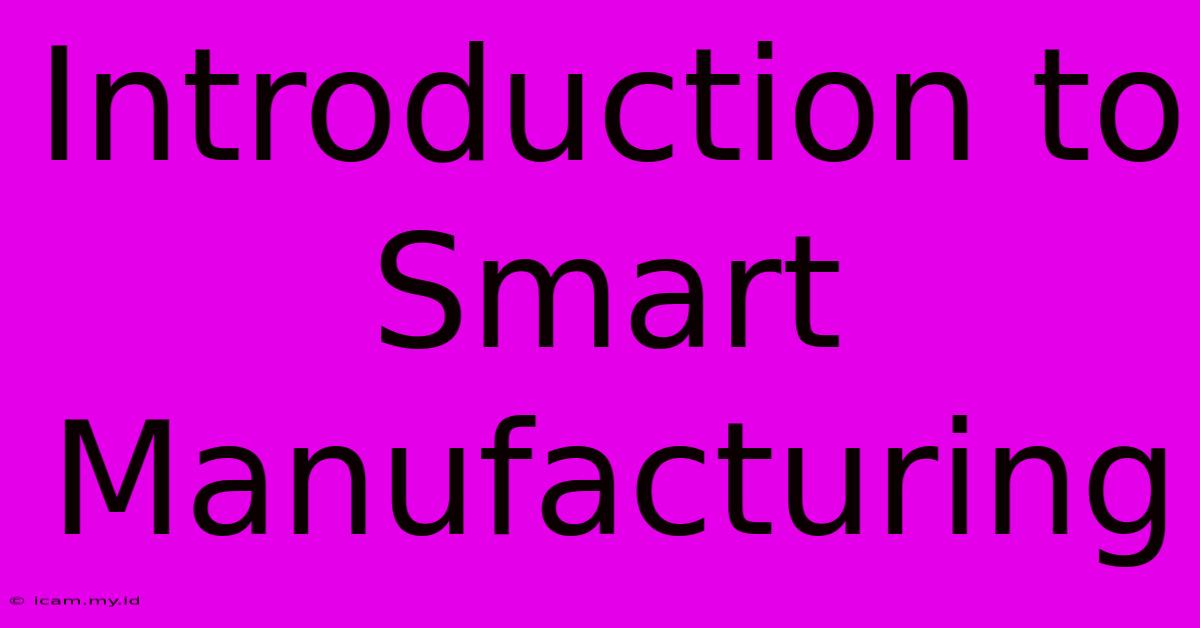
Thank you for visiting our website. Introduction To Smart Manufacturing. We hope the information we provide is helpful to you. Feel free to contact us if you have any questions or need additional assistance. See you next time, and don't forget to save this page!
Kami berterima kasih atas kunjungan Anda untuk melihat lebih jauh. Introduction To Smart Manufacturing. Informasikan kepada kami jika Anda memerlukan bantuan tambahan. Tandai situs ini dan pastikan untuk kembali lagi segera!
Featured Posts
-
Civil Servants Travel Net Zero Impact
Nov 28, 2024
-
Toni Kroos Awarded Golden Man
Nov 28, 2024
-
Autopsy Review Covid 19 Vaccine Deaths
Nov 28, 2024
-
Impact Of Automated Factories On Manufacturing
Nov 28, 2024
-
Another Award Snub For Vinicius Junior
Nov 28, 2024